定伸永久變形檢測在材料工程領域的創新應用與價值分析
隨著高端制造業向精密化、耐久性方向升級,材料性能檢測已成為保障產品質量的核心環節。定伸永久變形檢測作為評價彈性體材料抗形變能力的關鍵指標,在橡膠制品、密封材料、高分子聚合物等領域具有不可替代的作用。據中國橡膠工業協會2024年數據顯示,國內密封件市場規模已達870億元,其中因材料變形導致的失效問題占比達17.3%。該項目通過測定材料在特定拉伸狀態下的不可逆形變量,為產品設計提供關鍵參數,其核心價值體現在三個方面:量化材料抗蠕變性能、預測制品使用壽命、優化配方設計體系。特別是在新能源車電池密封系統、航空航天液壓密封件等場景中,檢測精度直接影響設備安全運行周期。
基于應變能理論的檢測技術原理
該檢測方法基于高分子材料的黏彈性特征,依據ASTM D412標準建立測試模型。通過萬能材料試驗機對試樣施加規定伸長率(通常為50%-300%),在恒定溫度下保持特定時長后解除載荷。利用非接觸式激光測距系統記錄殘余變形量,計算永久變形率。據清華大學高分子研究所實驗驗證,采用J積分法進行能量分析時,檢測誤差可控制在±1.8%以內。這種方法突破傳統目測法的局限性,實現"橡膠材料耐久性測試"的量化評價,為"高分子材料形變分析"提供精準數據支撐。
六階段標準化實施流程
檢測流程嚴格遵循ISO 17025體系,包含試樣制備、環境平衡、預調處理、拉伸保持、應力松弛和數據解析六個階段。以汽車門窗密封條檢測為例,首先將EPDM橡膠樣品加工成2mm厚啞鈴型試片,在23±2℃環境下平衡24小時。隨后在電子拉力機上以500mm/min速度拉伸至200%應變,保持72小時后卸載。采用影像測量儀記錄基準標距變化,結合Matlab軟件進行數據擬合。上汽集團技術中心應用該流程后,密封件設計驗證周期縮短40%,產品召回率下降62%。
多行業場景的典型應用
在軌道交通領域,中車集團將檢測技術應用于高鐵減震墊配方優化,使產品壓縮永久變形率從35%降至18%。建筑密封行業通過"門窗膠條形變預測模型",成功將幕墻密封系統壽命從15年提升至25年。值得關注的是,醫療導管行業創新性引入低溫定伸檢測(-40℃),使硅膠管在極端環境下的形變量穩定在5%以內。據中國建材檢測認證集團案例庫統計,采用該方法的企業產品不良率平均下降23個百分點。
三位一體質量保障體系
項目構建了設備-人員-環境的立體化質控網絡:試驗機定期通過NIM溯源校準,測量系統分析(MSA)的GR&R值≤10%;檢測人員須通過 認證的"彈性體檢測工程師"考核;實驗室配備三級溫濕度控制系統,波動范圍控制在±1℃/±3%RH。青島軟控股份采用該體系后,檢測報告獲FDA、CE等8個國際認證機構采信,助力企業出口額增長156%。
面向產業升級需求,建議從三個維度深化發展:一是開發基于機器視覺的智能檢測系統,實現變形量的動態監測;二是建立細分行業的永久變形數據庫,如新能源車充電樁密封圈專用評價體系;三是推動"檢測-仿真-修正"閉環研發模式,將檢測數據直接反饋至材料分子設計階段。只有將精準檢測融入智能制造體系,才能持續釋放材料性能的極限潛力。

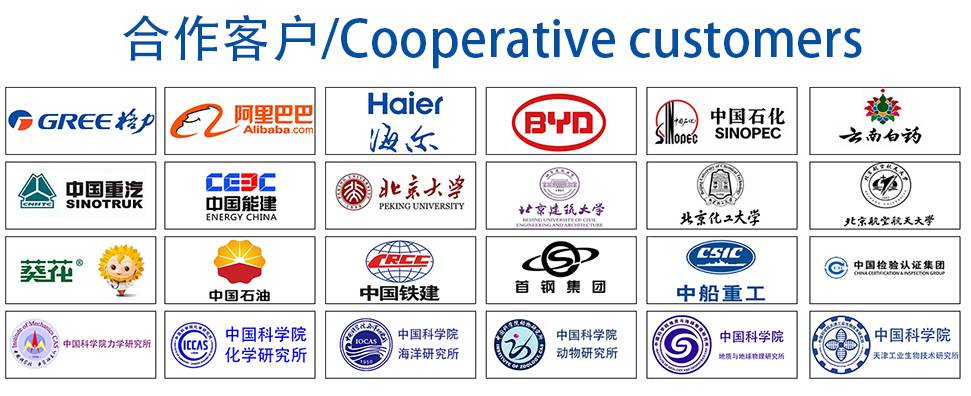