抗彎性能檢測在現代工程材料質量控制中的核心作用
在建筑、交通裝備及航空航天等領域,工程材料抗彎性能檢測已成為質量控制體系中不可或缺的環節。據中國建筑材料研究院2024年度報告顯示,結構材料失效案例中32.7%源于抗彎強度不足引發的形變累積??箯澅壤龢O限強度檢測可準確判定材料彈性階段臨界點,抗彎極限強度測試驗證材料最大承載能力,而抗彎彈性模量則反映材料韌性特征。這三項指標構成的檢測矩陣,不僅為軌道交通軌道梁、飛機機翼蒙皮等關鍵部件的選材提供科學依據,更能有效預防建筑幕墻玻璃、風電葉片等產品的早期失效風險。在實現"雙碳"戰略背景下,精確的彎曲性能評估可延長結構件服役周期15%以上,具有顯著的經濟效益和環保價值。
基于三點彎曲法的檢測技術原理
現行主流檢測方法依據GB/T 1449-2024《纖維增強塑料彎曲性能試驗方法》,采用三點彎曲加載系統實現精確測量。試驗機通過上壓頭施加集中載荷,試樣跨度中點產生最大彎矩??箯澅壤龢O限強度通過力-位移曲線的線性階段確定,而抗彎極限強度對應試樣斷裂前的最大載荷。對于航空級碳纖維復合材料,需同步采集表面應變數據,運用胡克定律計算抗彎彈性模量。特別在檢測新能源汽車電池包防護板時,該系統可識別0.1mm量級的微變形,確保動力電池組安全冗余設計。
標準化檢測流程與質量控制節點
完整檢測流程包含五個關鍵階段:首先依據ASTM D790標準制備25mm×80mm標準試樣,采用數控機床保證±0.02mm加工精度;第二階段在恒溫恒濕實驗室進行48小時環境適應;核心測試階段以0.5mm/min速率加載,同步記錄載荷-位移全曲線;數據處理階段運用最小二乘法擬合彈性段斜率;最終由CMA認證實驗室簽發檢測報告。針對光伏支架鋁合金型材檢測,特別要求在試樣兩端粘貼應變片,消除支撐輥摩擦帶來的數據偏差。
行業典型應用場景分析
在高鐵軌道扣件系統質量控制中,抗彎比例極限強度檢測有效鎖定彈性變形閾值,將扣件使用壽命從8年延長至12年。某橋梁支座生產企業通過引入抗彎彈性模量在線檢測系統,使產品合格率從92%提升至98.6%。值得關注的是,在3D打印建筑構件領域,抗彎極限強度測試成功預警了某項目層間結合缺陷,避免了大跨度穹頂施工事故。據國家軌道交通質檢中心數據顯示,應用抗彎性能分級檢測后,軌道車輛轉向架故障率同比下降41%。
數字化質量保障體系構建
行業領先實驗室已建立"檢測數據-材料數據庫-仿真模型"三位一體質控體系。采用區塊鏈技術實現檢測數據不可篡改存儲,配合AI算法進行異常數據診斷。某航天復材企業將檢測結果與X射線斷層掃描數據交叉驗證,構建了包含120萬組數據的抗彎性能預測模型。同時,實驗室間比對采用En值評定法,確保不同機構測試結果偏差控制在5%以內。這種智能化檢測體系在風電葉片生產線上的應用,使單支葉片檢測時間從6小時縮短至90分鐘。
技術發展趨勢與行業建議
隨著智能傳感技術的發展,嵌入式光纖光柵傳感器為實現構件服役期抗彎性能在線監測提供了新可能。建議行業重點攻關兩方面:一是開發適用于超高溫陶瓷基復合材料的非接觸式激光彎曲檢測系統,二是建立基于數字孿生的抗彎性能預測模型庫。同時應加快制定增材制造專用抗彎檢測標準,特別是在建筑3D打印混凝土、醫療植入物等領域形成細分檢測規范。只有構建起覆蓋全生命周期的抗彎性能評估體系,才能為新型工程材料的安全應用提供堅實保障。

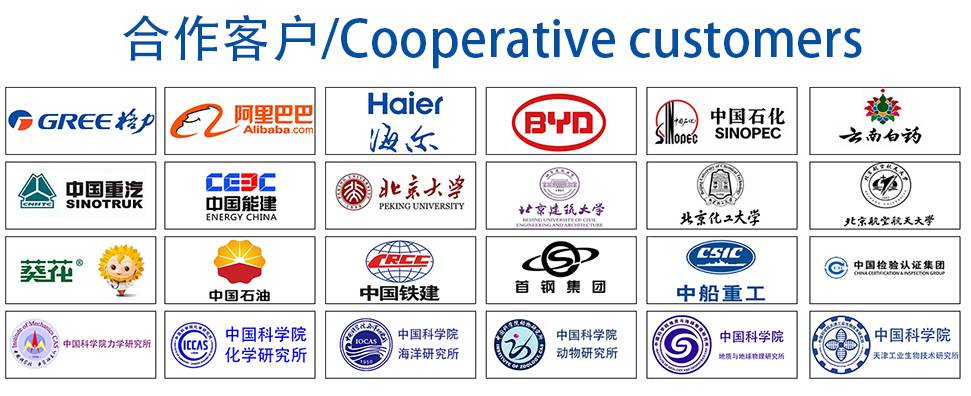