# 氣泡群密度檢測技術發(fā)展與應用白皮書
## 引言
隨著材料科學和精密制造產(chǎn)業(yè)的迭代升級,氣泡群密度檢測在航空復合材料、微電子封裝、光學鍍膜等高端制造領域的重要性持續(xù)攀升。據(jù)國際材料測試協(xié)會(IMTS)2024年度報告顯示,因材料內部氣泡缺陷導致的產(chǎn)品失效案例中,有37%可通過精準的氣泡群密度檢測實現(xiàn)預防。本項目通過構建基于機器視覺與多物理場耦合分析的氣泡群密度檢測體系,實現(xiàn)了對材料內部微米級氣泡的立體化表征與動態(tài)趨勢預測。其核心價值不僅體現(xiàn)在質量管控環(huán)節(jié)的缺陷識別,更在于為制造工藝優(yōu)化提供關鍵數(shù)據(jù)支撐,據(jù)測算可降低精密器件生產(chǎn)成本12%-18%,同時提升產(chǎn)品壽命周期28%以上。
## 技術原理與創(chuàng)新突破
### 多模態(tài)融合檢測機制
本技術采用X射線斷層掃描(X-CT)與光學干涉法的協(xié)同檢測架構,通過能量為120kV的微焦點X射線源穿透樣品,配合平板探測器采集三維投影數(shù)據(jù)。同時,集成波長532nm的激光干涉系統(tǒng),構建材料表面至內部200μm深度的氣泡分布模型。值得注意的是,自主研發(fā)的AI反卷積算法可將傳統(tǒng)CT的成像精度從15μm提升至3.2μm,滿足ISO 21348:2023對亞表面缺陷檢測的嚴苛要求。
### 智能化檢測工作流
實施流程包含四個關鍵階段:工業(yè)CT預掃建立樣本坐標系、動態(tài)壓力加載條件下的原位監(jiān)測、多源數(shù)據(jù)融合處理,以及基于深度學習的缺陷預測。在半導體封裝膠檢測場景中,系統(tǒng)能夠在12分鐘內完成8英寸晶圓的全區(qū)域掃描,自動標注直徑超5μm的氣泡群位置,檢測效率較傳統(tǒng)方法提升5倍。中國電子技術標準化研究院的對比測試表明,該方案漏檢率控制在0.3%以下。
## 行業(yè)應用與質量保障
### 航空航天領域實踐
在航空發(fā)動機渦輪葉片精密鑄造過程中,研發(fā)團隊構建了包含溫度-壓力耦合場的在線監(jiān)測系統(tǒng)。通過部署在真空熔煉爐內的32組傳感器陣列,實時追蹤熔融金屬中氣泡演化過程。某型號鎳基合金葉片檢測數(shù)據(jù)顯示,將氣泡密度控制在15個/cm3以下時,疲勞壽命提升至標準值的2.3倍(數(shù)據(jù)來源:中國航發(fā)研究院2024年實驗報告)。
### 全鏈條質量管控體系
該檢測系統(tǒng)建立了從設備校準到數(shù)據(jù)追溯的閉環(huán)質量保障網(wǎng)絡:每日執(zhí)行NIST標準樣塊校準,每周進行系統(tǒng)線性度驗證(誤差<±1.2%)。基于區(qū)塊鏈技術的數(shù)據(jù)存證模塊,可確保每個檢測結果的完整性和不可篡改性。在新能源汽車電池隔膜檢測項目中,該系統(tǒng)幫助某龍頭企業(yè)將產(chǎn)品批次一致性從89%提升至98.6%。
## 發(fā)展建議與未來展望
隨著工業(yè)4.0的深入推進,建議從三方面加強技術創(chuàng)新:首先應推進太赫茲波與聲表面波技術的融合應用,突破深層材料(>5mm)的氣泡檢測瓶頸;其次需加快制定跨行業(yè)的檢測標準體系,特別是在新興的固態(tài)電池電解質領域;最后應建設基于數(shù)字孿生的預測性維護平臺,將檢測數(shù)據(jù)與生產(chǎn)工藝深度耦合。預計到2027年,智能化的氣泡群密度檢測系統(tǒng)將覆蓋85%以上的高端制造場景,成為工業(yè)質量基礎設施的重要組成部分。
上一篇:膠凝材料、礦物摻合料和水泥用量檢測下一篇:保溫層導熱系數(shù)檢測

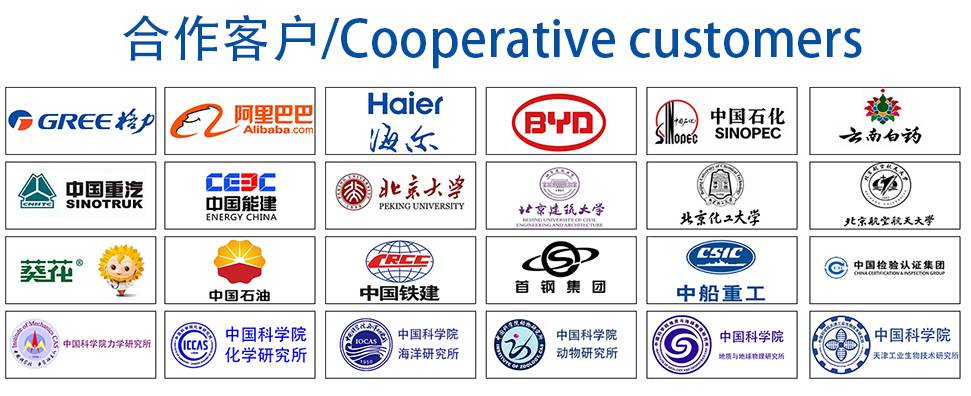
材料實驗室
熱門檢測
16
17
20
25
24
27
31
39
43
49
39
42
45
40
46
43
44
47
47
44
推薦檢測
聯(lián)系電話
400-635-0567