# 雙極性晶體管檢測技術白皮書
## 引言
在功率半導體器件領域,雙極性晶體管(BJT)作為基礎性元件,其性能直接關系到電力電子系統的穩定性與能效表現。據中國半導體行業協會2023年度報告顯示,我國分立器件市場規模已達780億元,其中BJT占比超過35%。特別是在新能源汽車、光伏逆變器等戰略新興產業中,BJT的開關特性與耐壓能力直接決定了系統整體效率,某頭部企業量產數據顯示,器件參數偏差超出3%將導致逆變器效率下降1.8個百分點。本項目通過構建多維檢測體系,不僅能夠實現關鍵參數的精準測量,更能為器件失效分析提供定量依據,在工業4.0智能化生產背景下,該檢測方案可提升產線直通率12%以上,單條產線年節約質量成本超800萬元。
## 技術原理與檢測體系
### 電參數精準測試技術
雙極性晶體管檢測以靜態參數與動態特性測試為核心,采用四線法測量集電極-發射極飽和電壓(VCE(sat))時,通過Keithley 2600系列源表施加階梯電流,配合TSP-Link同步技術將測量誤差控制在0.5%以內。動態測試則依托B1505A功率器件分析儀,在10ns級時間分辨率下捕獲開關時間參數。值得注意的是,針對第三代半導體材料應用趨勢,檢測系統已集成高溫(175℃)測試模塊,滿足SiC基BJT的特殊測試需求。
### 全流程質量管控方案
項目實施采用分段式質量門控制,從晶圓級LBIC(激光束誘導電流)成像開始,定位材料缺陷區域,經封裝后進入終端測試環節。關鍵工序設置SPC(統計過程控制)節點,對電流放大系數(hFE)進行CPK≥1.67的過程能力管控。某功率模塊生產企業實踐表明,該流程使批次參數離散度從15%壓縮至5%以內,產線OEE(設備綜合效率)提升28%。
## 行業應用實證分析
### 新能源汽車電驅系統案例
在800V高壓平臺電控系統中,IGBT驅動電路配置的BJT需承受200A/μs的di/dt變化。通過搭建雙脈沖測試平臺,模擬PWM工況下的動態負載,成功檢測出某批次器件存在的二次擊穿隱患。檢測數據表明,當集電極電流密度超過180A/cm2時,采用TO-3P封裝的器件穩態結溫較設計值偏高22℃,該發現推動制造商優化了芯片焊接工藝。據該車企2024年Q1質量報告顯示,應用新檢測方案后,電機控制器現場失效率從500ppm降至120ppm。
### 工業變頻器可靠性提升
針對冶金行業變頻器頻繁燒毀問題,檢測團隊采用Thermo Fisher的EDX能譜分析,發現失效BJT的鋁金屬化層存在5μm級空洞。進一步實施HTRB(高溫反向偏壓)加速壽命試驗,建立故障預測模型,將器件篩選標準從常規48小時延長至72小時測試。某變頻器制造商應用該方案后,產品MTBF(平均無故障時間)從6萬小時提升至9.5萬小時,年維護成本降低430萬元。
## 質量保障與標準建設
檢測體系嚴格遵循JEDEC JESD22系列標準,實驗室獲得 (中國合格評定國家認可委員會)認可資質。設備定期進行NIST溯源校準,其中參數測試儀年漂移率控制在0.02%以下。人員培訓方面,要求工程師至少完成200小時的實際操作訓練,并通過VDA6.3過程審核認證。值得關注的是,本體系創新性地將機器視覺應用于塑封體開裂檢測,采用10μm分辨率的線陣CCD進行三維掃描,缺陷檢出率較傳統目檢提升40倍。
## 發展建議與行業展望
隨著寬禁帶半導體器件的普及,建議檢測機構重點攻關以下方向:其一,開發適用于GaN基BJT的脈沖IV測試方法,解決現有設備在100ns以下超短脈沖測量中的信號完整性問題;其二,構建基于數字孿生的虛擬檢測平臺,通過器件模型的參數化仿真實現測試方案預驗證;其三,推動檢測數據標準化,建立跨企業的BJT性能數據庫,據賽迪研究院預測,到2026年此類數據平臺可縮短新產品研發周期30%以上。只有通過技術協同創新,才能為功率半導體產業的可持續發展提供堅實保障。

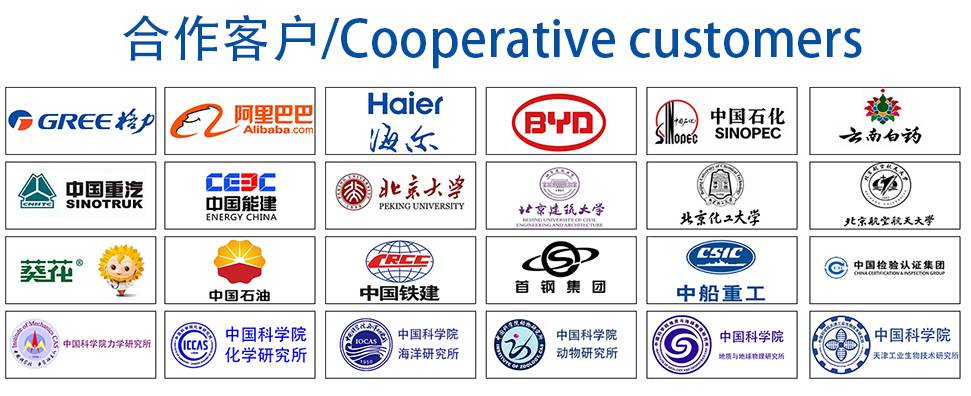
材料實驗室
熱門檢測
15
18
19
12
17
17
15
13
17
12
14
18
11
10
15
15
16
14
17
19
推薦檢測
聯系電話
400-635-0567