可調性檢測:核心檢測項目與技術解析
一、核心檢測項目清單
-
- 目的:確定被測對象參數可調整的上下限及中間值的有效性。
- 方法:
- 逐步調整參數至最大值、最小值,記錄系統響應。
- 測試中間關鍵點(如額定值的50%、80%)的性能表現。
- 判定標準:在極限范圍內無功能失效或結構性損傷。
-
- 目的:檢測實際輸出值與設定值的偏差。
- 方法:
- 使用高精度傳感器(如激光測距儀、扭矩儀)測量輸出參數。
- 對比設定值與實測值,計算誤差率(如±0.5%)。
- 案例:工業機器人關節角度調整精度需控制在±0.1°以內。
-
- 目的:驗證多次調整后結果的一致性。
- 方法:
- 在同一條件下重復調整參數(如10次循環),記錄數據。
- 統計分析標準差(SD)或極差(Range)。
- 標準:重復性誤差需低于行業規定閾值(如ISO 9283對機器人路徑重復性的要求)。
-
- 目的:檢測長時間運行或極端環境下的參數保持能力。
- 方法:
- 持續運行被測對象(如24小時),監測關鍵參數漂移。
- 模擬高溫、振動等環境,觀察調整功能是否受影響。
- 工具:環境試驗箱、振動臺。
-
- 目的:測量從調整指令發出到系統穩定的時間。
- 方法:
- 使用高速數據采集卡記錄指令執行至輸出穩定的時間差。
- 應用場景:伺服電機轉速調整需在50ms內達到目標值。
-
- 目的:驗證多系統聯動調整時的兼容性。
- 方法:
- 在集成環境中測試調整指令的沖突與協作(如PLC與機械臂通訊)。
- 檢查數據傳輸協議(如CAN總線、EtherCAT)的匹配性。
-
- 目的:確保調整過程符合安全規范與環境標準。
- 檢測項:
- 過載保護功能(如電流過載時自動切斷)。
- 電磁兼容性(EMC)測試,避免干擾其他設備。
二、檢測流程與工具
- 流程設計
- 制定測試計劃→搭建檢測環境→執行單項測試→數據記錄與分析→生成報告。
- 關鍵工具
- 數據采集系統(如NI LabVIEW)、高精度傳感器、環境模擬設備。
- 分析軟件:MATLAB(用于誤差分析)、Minitab(統計過程控制)。
三、行業應用差異
- 汽車制造:側重動力總成部件的可調性(如變速箱換擋邏輯)。
- 半導體設備:強調溫控系統的微調精度(±0.1℃)。
- 航空航天:需通過極端條件(高低溫、真空)下的穩定性測試。
四、檢測報告要點
- 明確列出不合格項及其影響(如精度超差導致良率下降)。
- 提供數據圖表(折線圖顯示參數漂移趨勢)。
- 建議整改措施(如更換高精度伺服閥)。
上一篇:輸入偏置電流檢測下一篇:荷電保持能力及恢復容量檢測

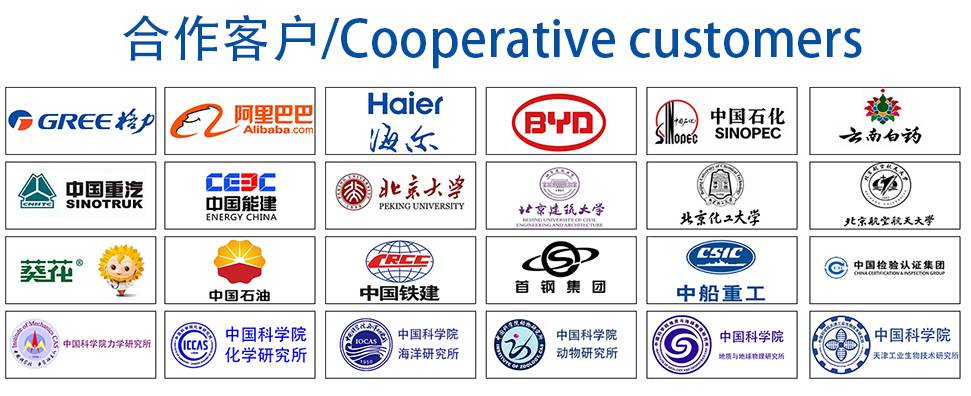
材料實驗室
熱門檢測
12
13
17
15
15
20
16
20
12
17
17
19
20
21
19
17
20
17
19
18
推薦檢測
聯系電話
400-635-0567