高溫環境下模制殼體應力檢測技術及關鍵檢測項目
引言
一、高溫應力檢測的核心檢測項目
1. 殘余應力檢測
- 檢測意義: 模制殼體在鑄造、焊接或注塑成型過程中可能產生殘余應力,高溫環境下殘余應力會與熱應力疊加,加速疲勞失效。
- 檢測方法:
- X射線衍射法(XRD):通過測量晶格畸變計算殘余應力,適用于金屬及陶瓷殼體,精度可達±20 MPa。
- 超聲波法:利用聲速與材料應力的相關性,適用于大體積殼體的快速無損檢測。
- 參考標準: ASTM E915(X射線法)、ISO 21457(超聲波法)。
2. 熱應力模擬與分布分析
- 技術原理: 通過有限元分析(FEA)模擬殼體在高溫下的熱-力耦合場,預測應力集中區域(如拐角、焊接接頭)。
- 關鍵參數: 材料熱膨脹系數(CTE)、彈性模量溫度依賴性、對流換熱系數。
- 實驗驗證: 結合熱電偶測溫與光纖光柵傳感器(FBG)實測數據,修正模擬結果誤差(通常需控制在5%以內)。
3. 動態應力實時監測
- 高溫應變測量技術:
- 光纖光柵傳感器(FBG):耐溫可達800°C,通過波長偏移量直接反映應變(精度±1με)。
- 高溫電阻應變片:鎳鉻合金基底應變片,耐溫400°C,需配合高溫膠黏劑使用。
- 應用場景: 燃氣輪機葉片在啟停階段的瞬態熱應力監測。
4. 高溫力學性能測試
- 測試項目:
- 高溫拉伸/壓縮試驗:測定材料屈服強度、彈性模量隨溫度的變化曲線(如TC4鈦合金在600°C時強度下降40%)。
- 蠕變試驗:評估材料在高溫長期載荷下的變形速率(如鎳基合金在800°C/100MPa下的穩態蠕變速率)。
- 設備要求: 配備高溫爐的萬能試驗機(如Instron 8860),溫度控制精度±1°C。
5. 金相組織與缺陷關聯分析
- 檢測流程:
- 從高溫服役后的殼體取樣,制備金相試樣。
- 掃描電鏡(SEM)觀察顯微裂紋、孔洞等缺陷。
- 電子背散射衍射(EBSD)分析晶粒取向與應力分布關系。
- 典型案例: 某航空鋁合金殼體在500°C下服役后,晶界處析出脆性相(Al2Cu),導致應力腐蝕開裂。
二、典型應用案例解析
案例1:航空航天發動機鈦合金殼體檢測
- 問題:發動機在超音速巡航時,殼體局部溫度達650°C,出現微裂紋。
- 檢測方案:
- 采用紅外熱像儀定位高溫區,結合FEA模擬熱應力分布。
- 使用FBG傳感器實時監測裂紋擴展速率。
- 結果:優化冷卻通道設計后,最大應力降低32%。
案例2:化工反應釜高溫襯里檢測
- 問題:玻璃鋼襯里在200°C酸性環境中發生分層剝離。
- 檢測方案:
- 超聲波C掃描檢測分層缺陷,XRD測量殘余應力。
- 實驗室模擬加速老化試驗,評估應力腐蝕敏感性。
- 結果:改用碳纖維/聚醚醚酮(PEEK)復合材料后,使用壽命延長3倍。
三、檢測技術的挑戰與對策
技術難點:
- 傳感器耐高溫限制:商用應變片在500°C以上易失效。
- 多物理場耦合復雜性:熱-力-化學交互作用難以精確建模。
- 現場檢測效率低:傳統方法需停機拆卸,影響生產連續性。
創新解決方案:
- 新型傳感器技術: 基于碳化硅(SiC)的MEMS傳感器,耐溫可達1000°C。
- 多物理場耦合仿真: 結合COMSOL Multiphysics實現熱-力-流耦合分析。
- 在線監測系統: 集成無線傳感網絡與機器學習算法,實現應力異常實時預警。
四、
參考文獻
- 《高溫合金應力檢測技術》(ASM International, 2019)
- ASTM E837-20 殘余應力測試標準
- 張偉等, "基于FBG的高溫應變監測系統設計", 《儀器儀表學報》, 2022.
上一篇:串擾衰減(多重放大器)檢測下一篇:動態條件下的總電源電流檢測

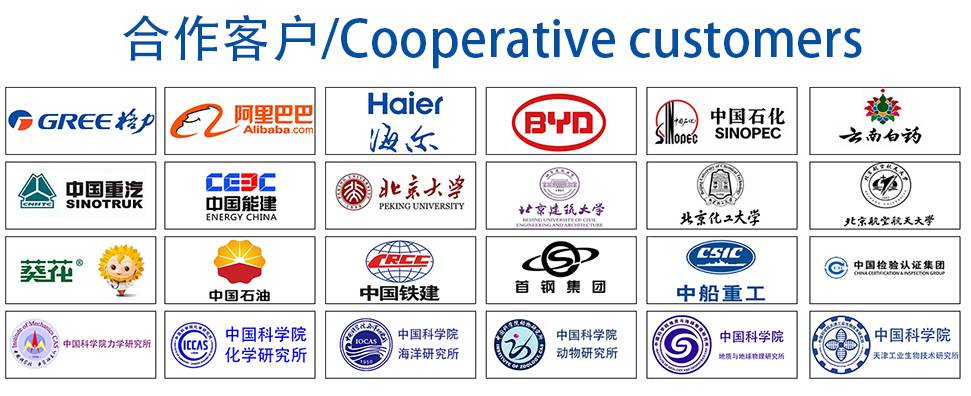
材料實驗室
熱門檢測
18
17
17
16
17
21
19
18
16
16
22
23
25
29
21
29
24
25
27
32
推薦檢測
聯系電話
400-635-0567