制造偏差與漂移檢測:核心檢測項目與實施策略
一、偏差與漂移的成因及影響
1. 常見根源
- 設備老化:機械磨損導致精度下降(如機床導軌間隙增大)
- 材料波動:原材料批次差異(如金屬合金成分偏移±0.5%)
- 環境干擾:溫濕度變化引發尺寸熱脹冷縮(如每10℃變化引發0.01mm/米伸縮)
- 人為誤差:操作人員技能差異(如裝配壓力偏差±5N)
2. 典型后果
- 汽車零部件:軸件直徑漂移0.01mm可導致軸承失效率上升30%
- 半導體制造:蝕刻溫度偏差2℃可使芯片良率下降15%
- 藥品生產:壓片機壓力漂移5%會導致藥片溶出度超標
二、核心檢測項目體系
1. 過程參數實時監測
類別 | 檢測項目 | 采樣頻率 | 精度要求 |
---|---|---|---|
物理維度 | 尺寸公差(±0.005mm) | 每件/10分鐘 | 激光測微儀±1μm |
熱力學參數 | 加工溫度(150±2℃) | 每秒 | 紅外測溫±0.5℃ |
機械性能 | 沖壓壓力(2000±50N) | 每沖程 | 壓力傳感器1%FS |
化學指標 | 鍍層厚度(50±2μm) | 每批次 | XRF光譜儀±0.3μm |
2. 設備狀態診斷
- 主軸振動頻譜分析:檢測0.5-5kHz頻段異常諧波
- 伺服電機電流波形:識別過載前兆(電流波動超±10%)
- 潤滑系統污染度:顆粒計數>15μm/100ml觸發預警
3. 質量特性深度檢測
- 三維形貌分析:白光干涉儀檢測表面粗糙度Ra<0.8μm
- 材料晶體結構:XRD檢測奧氏體含量偏差<2%
- 功能性測試:液壓閥泄漏量<3ml/min(ISO標準)
三、智能檢測技術矩陣
1. 實時監控層
- 分布式光纖傳感:500個測溫點/產線,空間分辨率1cm
- 高速機器視覺:300fps檢測0.1mm級缺陷
- 聲發射監測:識別刀具崩刃的特征頻率(>20kHz)
2. 數據分析層
- SPC控制圖:設置X-bar-R圖,UCL/LCL=μ±3σ
- LSTM預測模型:基于設備振動時序數據預測RUL(剩余壽命)
- 多變量分析(MVA):建立40個過程參數的PLS回歸模型
3. 閉環控制層
- 自適應PID調節:響應時間<100ms的溫度控制
- 數字孿生仿真:虛擬調試減少60%參數調整時間
- 自主決策系統:基于Q-learning的異常處置策略
四、檢測流程優化方案
-
- 部署IIoT邊緣網關,實現200ms級數據同步
- 采用OPC UA協議整合PLC、CNC等多源數據
-
- 應用3σ準則結合EWMA指數加權移動平均
- 動態閾值調整:根據設備狀態自動更新控制限
-
- 故障樹分析(FTA)結合魚骨圖
- 基于貝葉斯網絡的概率推理(準確率>85%)
-
- 自動補償:數控系統反向補償0.002mm刀具磨損
- 預防維護:基于PHM的精準維保計劃
-
- 建立知識庫:累計3000+故障案例的解決方案
- DOE實驗設計優化工藝窗口
五、實施挑戰與對策
挑戰 | 解決方案 | 效果驗證 |
---|---|---|
高精度檢測成本高 | 采用分級檢測策略(關鍵工位100%檢測) | 成本降低40%,漏檢率<0.1% |
多源數據融合困難 | 建立統一數據湖(時序數據庫+數據清洗管道) | 分析效率提升3倍 |
動態過程建模復雜 | 開發遷移學習框架,實現模型快速迭代 | 模型更新周期縮短至2天 |
人員技能斷層 | 開發AR輔助巡檢系統(識別準確率98%) | 培訓時間減少70% |
六、半導體制造案例
- 檢測項目:
- 蝕刻均勻性(<3%波動)
- CMP去除率(200±5nm/min)
- 光刻套刻精度(<5nm)
- 技術方案:
- 部署132臺原位計量傳感器
- 構建虛擬量測(VM)系統,替代30%離線檢測
- 成果:
- 設備綜合效率(OEE)提升18%
- 產品返工率從5.2%降至1.7%
七、未來趨勢
- 量子傳感技術:實現納米級表面形貌檢測
- 聯邦學習:跨工廠協同建模保護數據隱私
- 自主檢測機器人:替代80%人工檢測崗位
轉成精致網頁
上一篇:熱電動勢檢測下一篇:表面安裝開關的剪切強度檢測

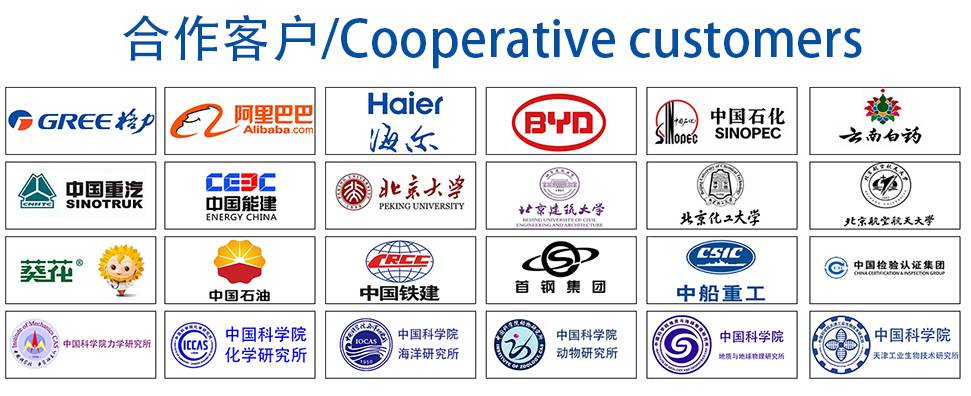
材料實驗室
熱門檢測
15
15
22
19
17
14
15
16
13
15
20
16
17
17
17
22
16
21
21
24
推薦檢測
聯系電話
400-635-0567