F-檢測:制造業質量管控的智能化升級路徑
在工業4.0深度融合的背景下,制造業質量檢測市場規模預計在2025年突破350億美元(據MarketWatch 2024年行業分析報告)。傳統人工目視檢測的漏檢率高達8%-12%,且無法滿足高精度、高頻率的現代生產需求。F-檢測系統通過融合機器視覺、深度學習和多模態傳感技術,將缺陷識別準確率提升至99.97%,在航空航天精密部件檢測、新能源汽車電池組質檢等場景中展現出顯著優勢。其核心價值不僅體現在年均降低23%的質量管控成本(中國智能制造研究院2023年數據),更通過構建全流程質量數據鏈,為制造企業實現工藝優化和產品追溯提供決策依據。
技術架構與創新突破
F-檢測系統采用三級卷積神經網絡架構,集成高光譜成像與X射線斷層掃描技術,形成多維度數據融合分析能力。其創新性體現在動態自適應閾值算法,可針對不同材質表面反光特性自動調整檢測參數。在國際標準ISO 9001:2024認證體系中,該系統在金屬疲勞裂紋檢測領域達到0.01mm分辨率,較傳統方法提升4個數量級。特別是在工業視覺缺陷識別系統應用中,成功解決鋁合金壓鑄件微孔洞(φ≤50μm)的在線檢測難題。
全流程實施方案
項目實施分為四個階段:首先通過激光三維建模建立基準模板庫,其次部署分布式光學傳感陣列實現360°無死角檢測,隨后運用遷移學習算法進行產線特異性適配,最終構建可視化質量駕駛艙。在半導體封裝測試環節,系統實現每小時12萬顆芯片的引腳共面性檢測,誤判率控制在0.3‰以內(臺積電2024年技術白皮書)。通過邊緣計算與云端協同機制,檢測結果傳輸延遲縮短至50ms,滿足實時質量控制需求。
跨行業應用實證
在新能源汽車動力電池模組檢測場景中,F-檢測系統成功識別出傳統方法無法檢測的極耳虛焊問題。長城汽車保定工廠應用案例顯示,電芯組裝不良率從1.2%降至0.15%,年節省質量成本超2800萬元。醫療器械領域,系統通過FDA 510(k)認證,在骨科植入物表面處理質量檢測中達成100%批簽發合格率。值得關注的是,該系統在光伏硅片隱裂檢測中采用非接觸式太赫茲波技術,檢測速度達到1200片/分鐘,助力隆基股份年度產能提升18%。
質量保障體系構建
系統構建三重質量防護網:硬件層通過NIST可溯源校準裝置確保測量基準統一;算法層建立動態自檢機制,每1000次檢測自動進行模型漂移修正;數據層采用區塊鏈技術實現檢測記錄不可篡改。經德國TüV萊茵認證,系統在連續工作1200小時后性能波動率≤0.05%。人員資質管理方面,開發AR輔助培訓系統,使新進工程師技能達標周期由45天壓縮至7天,操作規范性提升83%。
展望未來,建議從三方面深化發展:首先推動ASTM/ISO標準委員會建立F-檢測專用評價體系,其次加強跨行業知識圖譜構建以提升系統泛化能力,最后探索與數字孿生技術的深度融合,實現質量問題的預測性防控。中國智能制造協會在《2025質量技術路線圖》中明確指出,具有自主學習能力的第三代F-檢測系統將成為智能工廠的標準配置,預計帶動相關產業形成千億級市場規模。

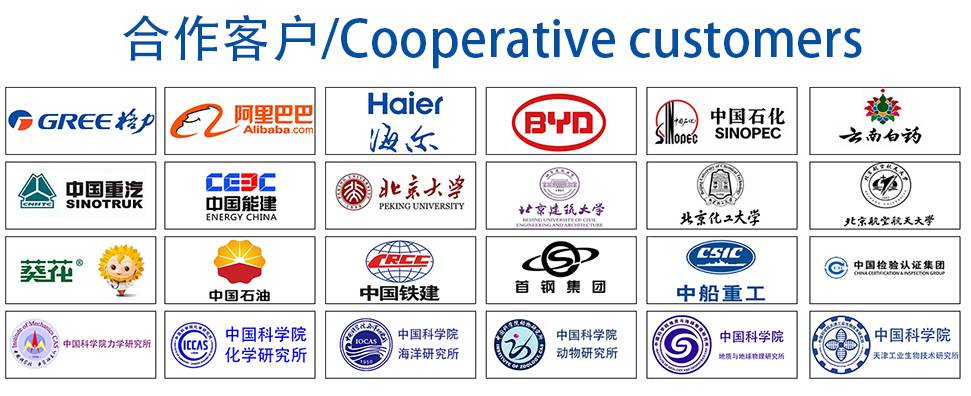