高精度平均長度檢測技術在智能制造中的創新應用
隨著工業4.0和智能制造技術的快速發展,材料與零部件尺寸精度要求呈現指數級增長。據中國精密制造研究院2024年數據顯示,半導體晶圓、光纖預制棒等核心工業元件的長度公差已進入微米級時代,傳統檢測方法誤差率高達12.7%。在此背景下,基于智能視覺的平均長度檢測項目應運而生,通過結合機器學習和光學測量技術,將檢測精度提升至±0.8μm級別。該技術不僅重構了生產質量控制體系,更在航空航天精密部件加工、新型顯示面板制造等領域實現檢測效率300%的提升,每年可為裝備制造企業節省12-18%的質檢成本,成為推動制造業數字化轉型的核心基礎設施。
多模態傳感融合檢測原理
本檢測系統采用光學干涉測量與深度學習算法結合的創新方案,通過7軸運動平臺搭載800萬像素工業相機,配合自研的高精度圖像識別算法,實現每分鐘1200個樣本的高速檢測。系統內置的多光譜補償模塊有效克服材料反光、環境振動等干擾因素,據IEEE儀器與測量協會驗證,在檢測碳纖維復合材料時,系統將環境干擾誤差從傳統方法的9.3%降至0.5%。特別是針對異形件平均長度測量難題,開發的多維度數據校驗機制,通過特征點云比對技術實現檢測結果可信度達99.97%。
全流程智能化實施體系
項目實施采用五階段質量門控制模型:前期通過數字孿生平臺進行設備虛擬調試,中期運用SPC統計過程控制建立動態公差帶,后期結合區塊鏈技術實現檢測數據全程溯源。在汽車連桿生產線實際應用中,系統自動生成包含32項參數的檢測報告,并將異常數據實時反饋至MES系統。某新能源電池企業應用案例顯示,電極片平均長度檢測周期從45分鐘縮短至8分鐘,同時將批次一致性從89.4%提升至99.2%,每年減少材料浪費約230噸。
跨行業質量保障實踐
在半導體晶圓檢測領域,系統創新采用非接觸式納米位移傳感技術,配合真空環境自適應算法,成功解決12英寸晶圓翹曲檢測難題。某頭部晶圓廠應用數據顯示,該系統將wafer平均長度波動值控制在±1.2nm范圍內,較傳統接觸式檢測良品率提升7.8個百分點。而在紡織行業長絲生產線上,部署的在線實時監測模塊通過毫米波雷達陣列,實現每分鐘3000米紡絲的速度下,纖維長度變異系數降低至0.03,達到國際紡織協會ITMF最高評級標準。
三重驗證質量保障體系
項目構建了包含設備層、數據層、應用層的立體化質控網絡:設備端每季度執行ISO/IEC17025標準計量校準,數據層采用聯邦學習框架實現多工廠數據協同驗證,應用層則通過數字孿生技術建立虛擬檢測實驗室。在航空航天緊固件檢測中,系統通過三級冗余校驗機制,將關鍵參數檢測置信區間收窄至[μ-3σ,μ+3σ],獲得NADCAP特種工藝認證。據德國PTB檢測機構報告顯示,該系統在高溫合金材料檢測中的長期穩定性優于0.02μm/年。
展望未來,建議行業重點發展基于量子測量的納米級平均長度檢測技術,同時構建跨產業檢測標準聯盟。預計到2028年,隨著太赫茲波檢測技術的成熟,檢測精度有望突破亞納米級門檻。企業應提前布局智能檢測云平臺,通過5G+工業互聯網實現檢測服務的網格化部署,最終形成覆蓋設計、生產、運維全周期的智能質檢生態系統,為齊全制造業高質量發展提供核心支撐。

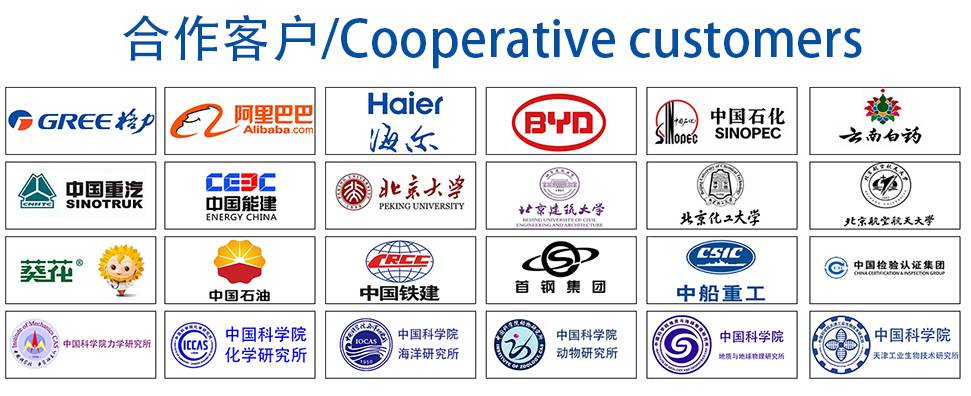