檢測技術原理與創新突破
現代座椅檢測體系依托多學科交叉技術,重點攻克結構穩定性與材料適配性難題。力學性能測試采用三軸聯動加載裝置,模擬75kg標準體重在0-15Hz振動頻率下的動態載荷(依據ASTM F1858標準)。環保指標檢測運用TD-GC/MS聯用技術,實現甲醛釋放量檢測精度達0.001mg/m3(中國環境科學研究院認證)。值得關注的是,智能傳感器網絡的引入使"座椅疲勞損傷預警系統"成為可能,通過植入式應變片實時監測關鍵節點應力變化,提前3000次循環預測結構失效風險。
標準化實施流程建設
項目實施遵循PDCA質量管理循環,形成從原材料管控到成品驗證的完整鏈條。在辦公椅檢測案例中,技術人員首齊全行靜態負載測試(最大承重150kg持續24小時),繼而開展5萬次往復升降測試(BIFMA X5.1標準)。兒童安全座椅檢測則增加動態碰撞測試,采用Q系列假人模擬14.5kg兒童在50km/h速度下的防護表現(參考ECE R44法規)。某知名品牌通過導入該流程后,產品耐久性指標提升40%,成功獲得德國藍天使環保認證。
行業應用與質量保障
在汽車座椅領域,檢測體系已實現與整車廠生產節拍的無縫對接。某新能源汽車企業運用座椅揮發性有機物(VOCs)快速篩查方案,將檢測周期從72小時壓縮至8小時,產線不良率下降62%。質量保障方面,實驗室通過 認可和ILAC國際互認,建立包含23個二級指標、156個檢測項目的評價矩陣。定期開展的"檢測設備量值溯源計劃",確保萬能材料試驗機等關鍵設備的測量不確定度≤1.5%。
未來發展建議與展望
建議行業重點發展基于數字孿生的虛擬檢測技術,通過構建座椅材料數據庫和失效模型庫,將實物檢測成本降低35%以上。同時應加快制訂智能座椅電磁兼容性檢測標準,應對電動調節、加熱按摩等新功能的合規需求。預計到2026年,融合AI視覺的缺陷自動識別系統將覆蓋60%以上生產線,推動座椅檢測從"事后驗證"向"過程預防"轉型升級。產學研各方需加強協作,共同完善覆蓋設計、生產、售后全鏈路的智能檢測生態系統。

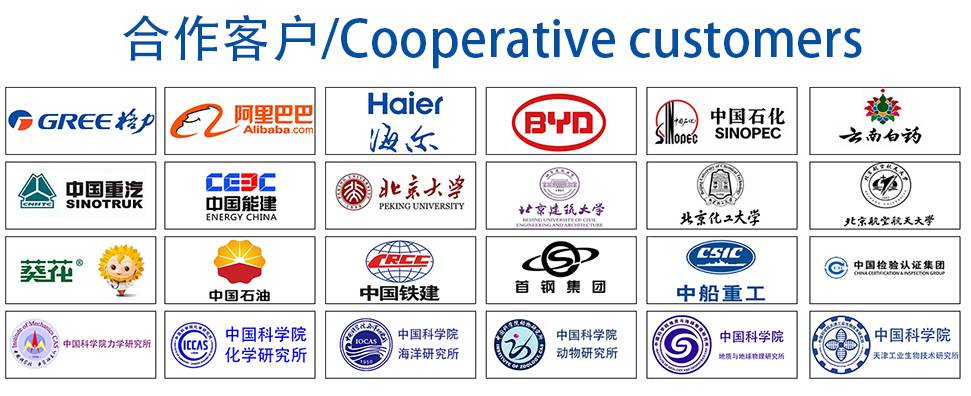