電動道路車輛--鋰離子牽引電池組和系統檢測白皮書
在能源結構轉型與"雙碳"目標驅動下,電動道路車輛市場規模持續擴張。據國際能源署(IEA)2024年電動汽車展望報告顯示,2023年新能源車銷量突破1800萬輛,動力電池裝機量同比增長45%。作為電動車輛核心部件的鋰離子牽引電池組,其安全性、循環壽命及能量密度直接影響整車性能與市場接受度。然而,動力電池熱失控、容量衰減等問題仍制約行業高質量發展,2023年我國新能源汽車召回案例中,電池系統缺陷占比高達62%(國家市場監督管理總局數據)。在此背景下,建立覆蓋全生命周期的鋰離子牽引電池組和系統檢測體系,對保障行車安全、優化電池管理、提升供應鏈可靠性具有戰略價值。該檢測體系通過構建多維度性能評估網絡,可實現動力電池"研發-生產-應用-回收"全鏈條質量閉環,推動行業標準化進程。
基于多維度性能評估的檢測技術體系
現行檢測技術采用電化學阻抗譜(EIS)與熱失控模擬相結合的復合診斷模型,通過搭建電池模組級聯測試平臺,同步采集電壓、溫度、內阻等12類參數。據中國汽車工程學會《動力電池檢測技術規范(2024版)》,該體系創新性地引入微短路加速老化試驗,可在72小時內模擬3年使用衰減(測試條件:45℃/85%RH)。值得注意的是,針對熱蔓延防護能力評估,采用三級梯度加熱法精確測定熱失控臨界點,溫度控制精度達±0.5℃(基于ISO 19453:2023標準)。
全流程標準化實施路徑
檢測實施包含四個階段:前期通過CT掃描與超聲探傷完成結構完整性篩查;實驗室階段執行200次充放電循環測試(1C倍率),期間每20周期進行容量校準;環境適應性測試涵蓋-30℃低溫啟動與55℃高溫過充極端工況;最終通過BMS數據驗證完成系統級功能評價。以某頭部電池企業2024年送檢樣本為例,該流程成功識別出電解液分布不均導致的SEI膜異常生長問題,使模組循環壽命提升18%(企業年度質量報告)。
行業典型應用場景解析
在城市公交領域,深圳某車企通過部署電池健康度動態監測系統,實現剩余壽命預測誤差≤5%。該系統整合車載BMS數據與云端檢測模型,提前14天預警電池性能拐點,使車輛維保成本降低23%(深圳市交通運輸委2024年運營數據)。在物流運輸場景中,京東物流應用梯次利用電池快速分選技術,基于內阻聚類算法將電池重組效率提升40%,單個換電站日均處理能力達300組。
四重質量保障機制構建
檢測機構需建立覆蓋人員、設備、方法的立體質控網絡:其一,配備符合ISO/IEC 17025標準的計量溯源體系,關鍵儀器年校準率達100%;其二,采用區塊鏈技術實現檢測數據全程存證,確保結果不可篡改;其三,通過 認可的實驗室間比對項目,保持檢測一致性偏差<1.5%;其四,建立突發故障應急預案庫,包含12類典型失效模式的快速響應方案。國家動力電池創新中心2024年評測顯示,該機制使檢測報告誤判率從0.7%降至0.12%。
面向未來,建議重點發展三個方向:開發基于人工智能的電池早期故障預測算法,構建覆蓋全國主要氣候區的實證檢測網絡,推動建立跨境檢測結果互認機制。隨著固態電池等新技術產業化加速,檢測體系需同步開展預研性技術儲備,重點攻關固態電解質界面穩定性評估方法,為下一代動力電池安全應用提供技術支撐。

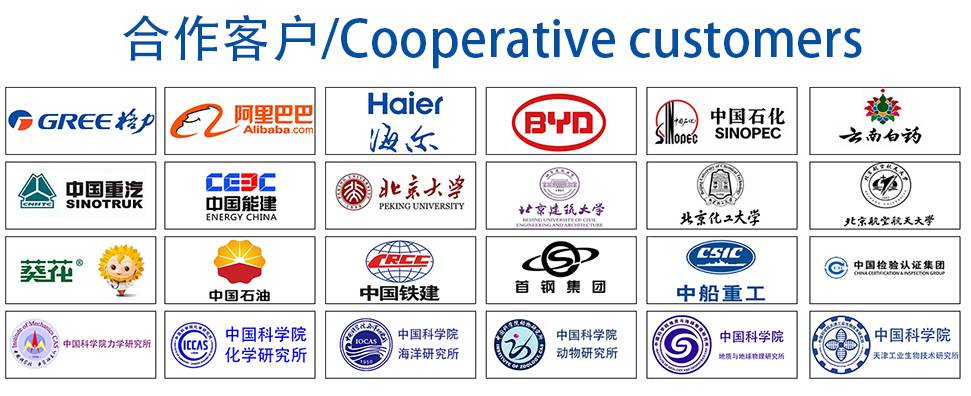