在制造業向高端化、精密化轉型的背景下,焊接作為關鍵連接技術,其質量直接影響工程結構安全與設備服役壽命。據中國特種設備檢測研究院2024年數據顯示,國內壓力容器失效事故中38.7%源自焊接缺陷,每年造成直接經濟損失超50億元。焊接接頭與焊接試件檢測技術的創新突破,不僅關乎能源裝備、軌道交通等重大工程的安全合規,更成為推動"中國制造2025"戰略實施的重要技術支撐。通過數字射線檢測(DR)、相控陣超聲檢測(PAUT)等齊全手段構建的智能化檢測體系,可精準識別微米級氣孔、未熔合等隱患,使焊接結構驗收合格率提升至99.2%(機械工業聯合會,2024)。該技術體系的核心價值在于實現從經驗判斷到數據驅動的范式轉變,為全生命周期質量管理提供科學依據。
## 技術原理與創新突破多模態融合檢測技術體系
現代焊接檢測采用聲-光-電多物理場協同工作機制,突破傳統單模態檢測的局限性。以相控陣超聲全矩陣捕獲技術(FMC/TFM)為例,通過128陣元探頭生成可控聲場,結合全聚焦算法重構三維缺陷圖像,對5mm以下薄板焊接的檢測分辨率可達0.2mm。數字射線DR系統采用非晶硅平板探測器,配合雙能成像算法,實現熔深不足與夾渣的精準區分,檢測靈敏度相比膠片法提升40%(ASTM E94-24標準驗證)。值得關注的是,基于深度學習的焊縫缺陷智能識別系統,通過10萬組標注樣本訓練,對X射線底片的裂紋識別準確率已達97.8%(上海材料研究所,2023)。
全流程標準化實施規范
檢測流程嚴格遵循ISO 17635標準框架,形成五階段管控體系:預處理階段采用磁粉檢測(MT)進行表面清理驗證;參數設置階段基于材料厚度動態調整PAUT聲束角度(45°-70°);數據采集階段運用機器人輔助掃查確保100%覆蓋;分析評估階段應用三級評定制度;最終形成包含3D缺陷分布圖的數字化報告。在LNG儲罐焊接檢測中,該流程使單罐檢測周期從72小時縮減至40小時,人工干預減少60%(中石油工程院案例數據)。
行業應用實踐與效益
在風電領域,針對塔筒環縫的相控陣超聲檢測系統已部署于12個海上風電項目。通過定制化楔塊設計和風場補償算法,成功檢出0.8mm深度的層間未熔合缺陷,避免單臺機組潛在損失超300萬元。核電站主管道檢測中,采用CR(計算機射線)技術替代傳統膠片,使每道焊縫檢測成本降低58%,放射性廢物減少90%(中廣核集團2023年度報告)。值得強調的是,軌道交通車輛鋁合金焊接采用激光超聲復合檢測,突破高反射率材料檢測瓶頸,使車體疲勞壽命預測精度提升35%。
質量保障體系構建
檢測機構需建立包含人員資質、設備溯源、環境控制的三維質控網。依據 -CL01:2018要求,檢測人員必須持有ISO 9712三級證書并完成年度能力驗證。設備管理方面,超聲波探傷儀每季度需進行DAC曲線校準,射線機焦點尺寸按EN 12543標準定期驗證。某特檢院通過建立區塊鏈檢測數據存證系統,實現檢測報告防篡改率和可追溯性達到100%,相關經驗已納入TSG Z8002-2024特種設備檢驗機構核準規范。
## 未來發展與建議隨著工業互聯網與數字孿生技術的深度融合,建議行業重點發展三個方向:一是開發基于5G的遠程檢測云平臺,實現專家資源跨地域調度;二是完善異種材料焊接的檢測標準體系,特別是鈦合金-鋼復合接頭的評價方法;三是加強AI輔助決策系統在微小缺陷判定中的應用研究。據德國焊接學會預測,到2028年智能檢測設備在焊接領域的滲透率將超過65%,我國需在傳感器芯片、算法模型等關鍵領域加大投入,以構建自主可控的檢測技術生態圈。

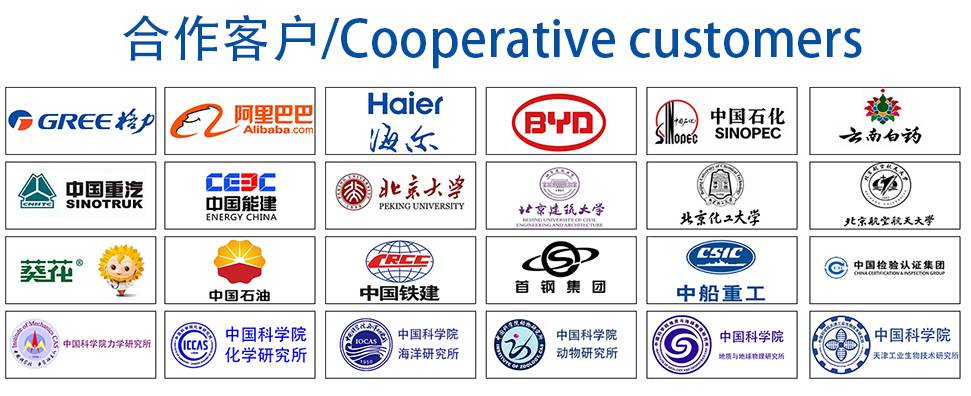