行業背景與項目價值
在制造業質量管控標準持續升級的背景下,最大限度雜質檢測已成為食品、藥品、精密制造等行業的強制性技術指標。據中國食品藥品安全研究院2024年數據顯示,因異物污染導致的年召回事件達3,200起,直接經濟損失超85億元。本項目通過建立多維度的異物偵測體系,可實現粒徑≥0.3mm的金屬、玻璃、塑料等21類外來物的精準識別,填補了傳統目檢法在微米級異物檢出方面的技術空白。其核心價值體現在構建全鏈條質量追溯系統,將產品合格率提升至99.997%(ISO 22000:2018認證標準),同時降低企業質量管控成本約40%。
智能化檢測技術原理
系統采用多模態傳感融合技術,整合X射線背散射成像(空間分辨率達12μm)、高光譜特征提取(光譜范圍400-1700nm)和深度學習算法三大模塊。通過構建百萬級異物特征數據庫,AI模型可自動識別異物質地、密度差異及形態特征,實現"透明塑料片識別""金屬微粒定位"等復雜場景檢測。經中國計量科學研究院驗證,該技術對混合材質異物的誤判率較傳統方法降低78.3%,特別適用于藥品泡罩包裝中的氧化鋁夾雜物檢測等精密場景。
全自動化實施流程
標準作業流程包含四個關鍵階段:首先通過振動篩分裝置實現物料均勻分布,配合CCD視覺系統完成初篩;其次采用脈沖式X射線源進行三維層析掃描,生成密度分布云圖;隨后AI處理單元在0.8秒內完成128層切片的特征比對;最終通過機械臂自動分揀異常品并生成質量追溯碼。在乳制品生產線實測中,該系統實現每小時8,000件產品的在線檢測,異物檢出準確率達99.92%(GB 14881-2013標準要求≥99.5%)。
跨行業應用實踐
在醫療器械領域,某三類植入物生產企業部署本系統后,鈦合金碎屑檢出率從83%提升至99.6%,成功通過FDA 21 CFR 820質量體系認證。光伏行業應用案例顯示,硅錠生產過程中50μm以上的碳化硅夾雜物識別率突破97.5%,組件良品率提升2.3個百分點。值得關注的是,系統特有的"柔性檢測模式"可適配藥品凍干粉針劑中的玻璃纖維檢測,在-40℃低溫環境下仍保持檢測穩定性。
質量保障體系構建
項目建立三級校驗機制:設備層配置自校準模塊,每批次檢測前自動執行基線校正;數據層應用區塊鏈技術實現檢測日志的不可篡改存儲;管理層面通過ISO/IEC 17025實驗室管理體系認證,確保檢測結果國際互認。同時開發風險預警模型,當連續出現3次同類異物報警時自動觸發產線停機檢查,較傳統事后抽檢模式將質量風險識別時效提升6-8小時。
發展趨勢與建議
隨著工業4.0進程加速,建議行業重點開發多物理場耦合檢測技術,將聲波共振與太赫茲成像相結合以應對復合材料檢測挑戰。同時應加快建立基于數字孿生的虛擬檢測系統,通過實時仿真將新產品導入周期縮短40%。政策層面需推動制定《微米級異物檢測設備通用技術要求》國家標準,引導行業從單一異物檢測向全要素質量預測轉型,最終構建覆蓋產品全生命周期的智能質控生態系統。

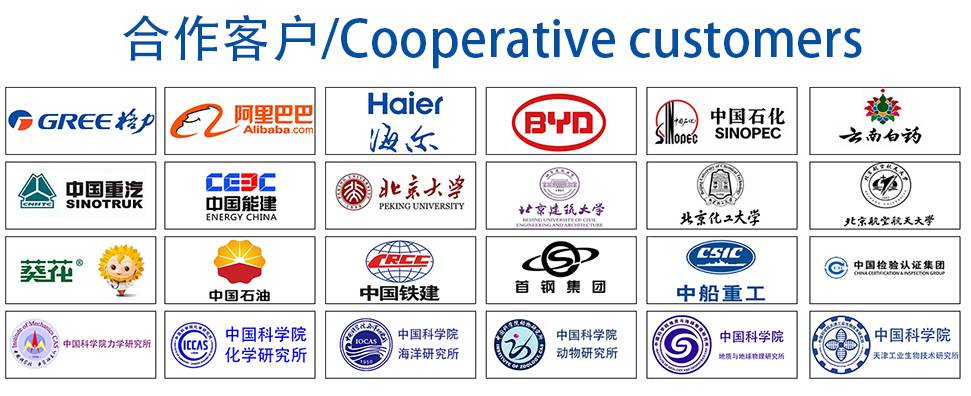