鋼鋁復合帶檢測的重要性與應用領域
鋼鋁復合帶作為電力、交通、建筑等行業的重要材料,其性能直接影響設備的安全性和使用壽命。該材料通過冷軋工藝將鋼帶與鋁帶復合而成,兼具鋼的高強度和鋁的耐腐蝕性。為確保其滿足行業標準及使用要求,需通過系統的檢測項目對物理性能、化學特性及復合層質量進行全面分析。近年來,隨著新能源裝備、高鐵等領域的快速發展,鋼鋁復合帶檢測技術的精準性和效率需求顯著提升。
核心檢測項目與技術要求
1. 原材料基礎性能檢測
需對鋼帶和鋁帶的化學成分、力學性能進行驗證:采用光譜分析儀檢測元素含量(如Al純度≥99.5%),通過拉伸試驗機測試抗拉強度(鋼層≥350MPa,鋁層≥80MPa)、延伸率等指標,并利用金相顯微鏡觀察晶粒度是否符合工藝要求。
2. 復合層結合強度測試
通過剝離試驗測定界面結合力(≥50N/cm),使用超聲波探傷儀檢測復合層是否存在空洞、裂紋等缺陷,高溫熱循環試驗需滿足300次循環后結合強度下降率<10%的嚴苛標準。
3. 耐腐蝕性能驗證
執行中性鹽霧試驗(500小時無基體腐蝕)、濕熱試驗(40℃/95%RH條件下1000小時)以及電化學阻抗譜分析,評估材料在惡劣環境下的防護能力,同時需檢測表面氧化膜厚度(8-15μm)及致密性。
4. 尺寸精度與表面質量檢測
使用激光測厚儀檢測厚度公差(±0.02mm),配備工業視覺系統掃描表面劃痕、壓痕等缺陷,波紋度需控制在≤0.3mm/m范圍內,邊緣毛刺高度不得超過0.05mm。
5. 特殊環境適應性試驗
針對不同應用場景增加專項測試:電氣行業需檢測電阻率(≤0.028Ω·mm2/m)和電磁屏蔽效能,軌道交通領域需進行-50℃低溫沖擊測試,建筑用途則需滿足防火等級B1標準。
檢測技術發展趨勢
隨著智能化檢測設備的普及,X射線三維成像技術可實現復合層缺陷的立體定位,機器視覺系統能實現表面質量的在線實時監測。同時,基于大數據的質量追溯系統正在推動檢測數據與生產工藝的深度聯動,為提升鋼鋁復合帶產品一致性提供技術保障。

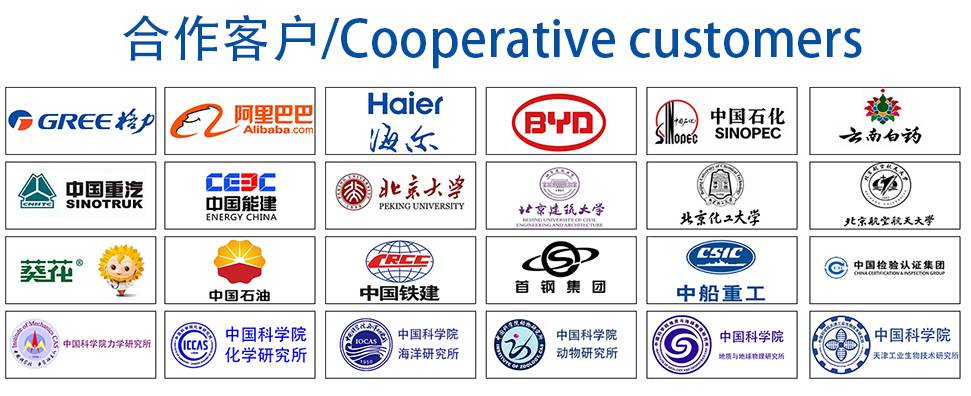