鋼制管法蘭檢測概述
鋼制管法蘭是工業管道系統中不可或缺的連接部件,廣泛應用于石油、化工、電力、船舶等領域。其主要功能是實現管道與設備、閥門之間的密封連接,承受系統內的壓力和溫度變化。法蘭的制造材料通常包括碳鋼、合金鋼、不銹鋼等,需根據使用環境選擇對應的材質和工藝標準(如GB/T、HG、ASME等)。由于法蘭的密封性、強度及尺寸精度直接影響整個管道系統的安全性和穩定性,因此嚴格的檢測流程是確保其質量的核心環節。鋼制管法蘭檢測需覆蓋原材料、加工工藝、成品性能等多個維度,確保其符合設計要求和行業規范。
關鍵檢測項目及方法
1. 尺寸精度檢測
法蘭的外徑、螺栓孔中心距、孔徑、厚度等幾何尺寸是檢測的核心內容。需使用卡尺、千分尺、三坐標測量儀等工具對關鍵部位進行測量,確保公差符合GB/T 9112-2010或ASME B16.5標準。對于密封面的平面度,需采用專用平尺或激光掃描設備進行高精度校驗。
2. 密封面加工質量檢測
密封面的粗糙度(Ra值)需使用表面粗糙度儀測定,通常要求Ra≤3.2μm。同時需目視檢查密封面是否存在劃痕、凹坑或銹蝕,并使用滲透檢測(PT)或磁粉檢測(MT)排查微觀裂紋。對于凹凸面、榫槽面等特殊結構,需驗證配合間隙的均勻性。
3. 力學性能測試
包括拉伸試驗、沖擊試驗(如夏比V型缺口沖擊)及硬度測試(布氏/洛氏硬度),以驗證材料的抗拉強度、屈服強度和韌性是否達標。試樣需取自法蘭本體或同批次材料,并依據ASTM A105或GB/T 12228標準進行判定。
4. 無損探傷檢測
對鍛造成型法蘭需進行超聲波檢測(UT)以發現內部氣孔、夾雜等缺陷;射線檢測(RT)適用于焊縫區域的完整性評估;磁粉檢測(MT)則用于表面及近表面裂紋的排查,尤其適用于高壓法蘭的驗收。
5. 密封性能試驗
通過水壓試驗或氣壓試驗模擬實際工況,檢測法蘭與墊片的配合密封性。試驗壓力一般為設計壓力的1.5倍,保壓時間不少于10分鐘,期間需觀察是否有泄漏或變形現象。
6. 防腐與表面處理檢測
對于鍍鋅、噴塑或涂漆法蘭,需使用涂層測厚儀檢測防腐層厚度,并執行鹽霧試驗驗證耐腐蝕性。若采用橡膠襯里,需檢查襯里與金屬基體的粘結強度及完整性。
7. 材料成分分析
通過光譜分析儀(OES)或化學滴定法對法蘭材料的碳、錳、鉻、鉬等元素含量進行定量分析,確保符合材料證書要求,避免因成分偏差導致強度不足或耐腐蝕性下降。
檢測結果應用與質量控制
檢測數據需形成完整的報告,并與設計文件、采購規范進行對比驗證。對于不合格項需追溯至生產環節(如鍛造溫度控制、機加工參數等),并采取返修或報廢處理。第三方實驗室的復檢可進一步提升結果可信度,尤其適用于核電、LNG等高風險領域。通過系統化的檢測流程,可有效降低法蘭在服役中發生泄漏、斷裂的風險,保障工業裝置的長期穩定運行。

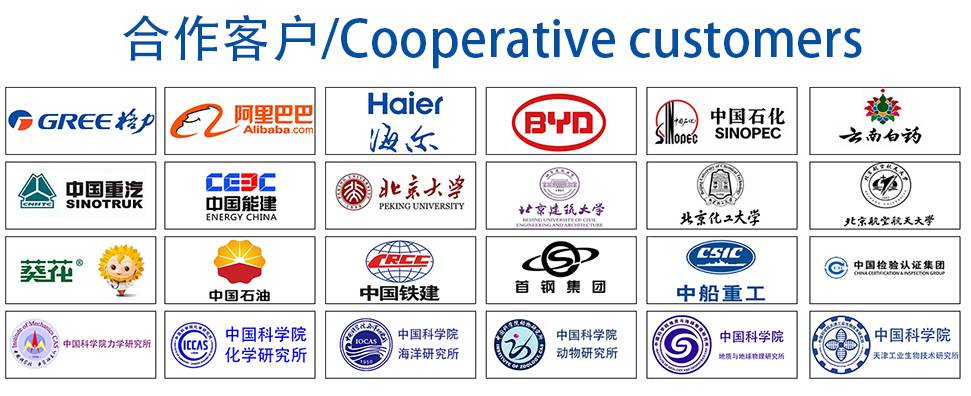