制冷裝置用壓力容器檢測的重要性
制冷裝置用壓力容器作為制冷系統的核心承壓部件,其安全性直接關系到設備運行效率和人員生命財產安全。由于長期承受周期性溫度變化、介質腐蝕及交變載荷作用,容器易出現材料疲勞、焊縫裂紋或局部腐蝕等隱患。依據《固定式壓力容器安全技術監察規程》(TSG 21)和GB 150《壓力容器》標準要求,定期開展系統性檢測是預防泄漏、爆炸事故的關鍵手段。檢測過程需覆蓋設計、制造、使用全生命周期,尤其對于低溫工況下的容器,需重點關注材料的低溫脆性轉變特性。
主要檢測項目及實施要點
1. 材料與結構完整性檢測
通過光譜分析驗證殼體材質與設計文件的一致性,使用超聲波測厚儀測量壁厚減薄量(允許誤差≤10%)。對封頭過渡區、接管角焊縫等應力集中部位進行磁粉檢測(MT)或滲透檢測(PT),發現表面裂紋需立即評定處理。
2. 焊縫質量評估
采用X射線檢測(RT)或超聲相控陣技術(PAUT)對縱環焊縫進行內部缺陷篩查,氣孔、夾渣等缺陷應符合NB/T 47013標準驗收等級。對返修焊縫需進行200%擴探復查。
3. 耐壓試驗驗證
按照1.25倍設計壓力進行水壓試驗,保壓時間不少于30分鐘,觀察有無異常變形或滲漏。氨系統容器需額外進行氣密性試驗,采用氦質譜檢漏儀檢測微量泄漏(泄漏率≤1×10?? Pa·m3/s)。
4. 安全附件校驗
壓力表精度等級應達1.6級且每半年校驗一次,安全閥起跳壓力偏差不超過設定值±3%。爆破片裝置需核對標定爆破壓力與系統最大工作壓力的匹配性。
5. 腐蝕與防護檢測
對蒸發器、冷凝器等接觸冷媒的部件,使用內窺鏡檢查晶間腐蝕情況。涂層附著力采用劃格法測試(達到ISO 2409標準1級),犧牲陽極保護系統需測量保護電位(-0.85~-1.05V vs.CSE)。
檢測周期與風險管控
首次全面檢驗應在投用后3年內進行,后續檢驗周期根據安全狀況等級確定(最長不超過9年)。對R717(氨)系統容器、存在CL-離子腐蝕的沿海設備,應縮短20%檢驗周期。建立基于風險檢驗(RBI)的評估體系,運用聲發射在線監測技術實現動態預警,確保制冷壓力容器全生命周期安全可控。

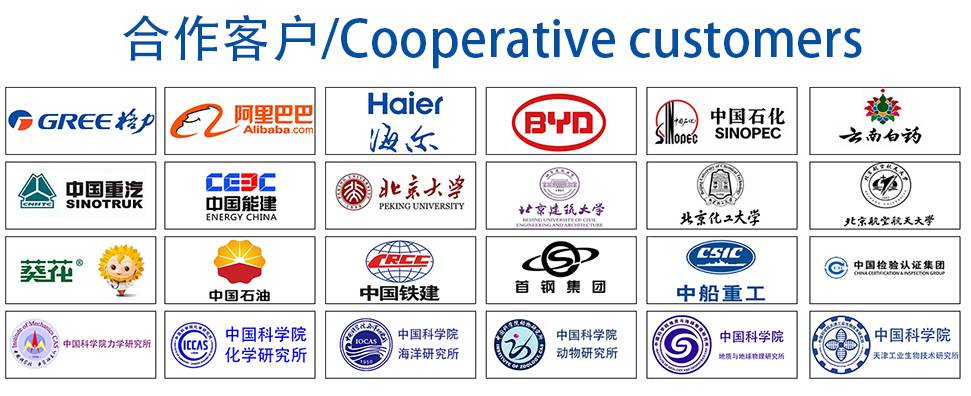