航天滾動軸承檢測關鍵技術解析
在航天工業領域中,滾動軸承作為運載火箭發動機、衛星姿態控制機構及空間站機械臂等核心部件的關鍵傳動單元,其性能穩定性直接關系著航天器的運行安全與任務成功率。由于航天器需經歷發射階段的劇烈振動、太空極端溫度(-180℃至+300℃)以及超高真空等嚴苛環境考驗,對滾動軸承的檢測提出了遠超民用標準的特殊要求。目前國際航天領域已形成包含材料特性、幾何精度、動態性能三大維度共26項專項檢測指標體系,通過多維立體化檢測手段確保軸承在壽命周期內的零失效表現。
1. 材料微觀組織檢測
采用場發射掃描電鏡(FE-SEM)和透射電鏡(TEM)對軸承鋼的晶粒度(要求優于ASTM 12級)、碳化物分布(尺寸≤0.5μm)及殘余奧氏體含量(控制在3-8%)進行納米級觀測。同步開展X射線衍射殘余應力分析,確保表層殘余壓應力值≥1200MPa。針對新型陶瓷混合軸承,需進行能譜分析(EDS)驗證氮化硅材料的氧含量≤0.15wt%,并利用激光共聚焦顯微鏡檢測表面微裂紋(閾值≤2μm)。
2. 幾何精度數字孿生檢測
基于ISO 12181標準構建軸承全參數三維模型,采用白光干涉儀實現溝道曲率半徑(公差±0.5μm)、滾道波紋度(W值≤0.05μm)的亞微米級測量。配置六軸工業機器人搭載激光跟蹤儀,對大型軸承組件(如直徑2.4米的空間機械臂軸承)進行動態形變監測,采樣頻率達2000Hz時可捕捉0.8μm級的瞬時變形量。開發專用算法對1.5TB/小時的點云數據進行實時處理,構建數字孿生體進行虛擬裝配驗證。
3. 極端工況模擬試驗
在真空熱試驗艙內(極限真空度5×10^-7Pa)進行-196℃(液氮冷卻)至+350℃(紅外加熱)的2000次溫度循環試驗,監測保持架間隙變化率(標準值≤0.3%)。采用電磁振動臺模擬發射階段的25g/2000Hz隨機振動,通過光纖Bragg光柵傳感器網絡實時采集256通道應變數據。針對深空探測任務,設計10^-12torr級超高真空摩擦試驗臺,持續監測20000rpm轉速下的扭矩波動(允許偏差±1.5%)。
4. 智能健康監測系統
植入MEMS傳感器陣列(尺寸3×3×1mm3)實現軸承運行狀態在線監測,包括:
? 聲發射系統捕捉早期剝落信號(特征頻率50-150kHz)
? 電容式油膜厚度傳感器(分辨率10nm)
? 分布式光纖測溫(空間分辨率1cm)
通過BP神經網絡對多源異構數據進行融合分析,建立剩余壽命預測模型(誤差≤5%),成功應用于長征五號火箭渦輪泵軸承的在軌健康管理。

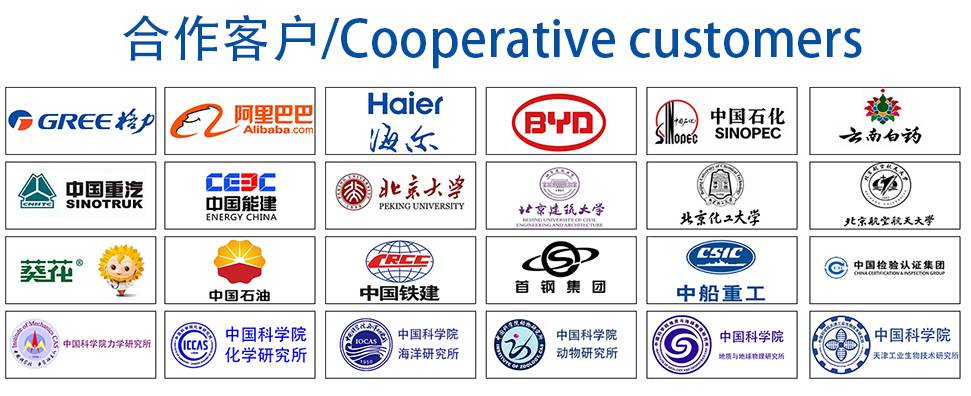