低速擺動自潤滑向心關(guān)節(jié)軸承檢測的重要性
低速擺動自潤滑向心關(guān)節(jié)軸承作為精密機械傳動系統(tǒng)的核心部件,廣泛應用于航空航天、工程機械、機器人關(guān)節(jié)等高精度領(lǐng)域。其特殊結(jié)構(gòu)能在無外部潤滑條件下實現(xiàn)長期穩(wěn)定運行,但復雜的工況環(huán)境(如重載、低頻擺動、粉塵污染等)對軸承性能提出了嚴苛要求。為確保其可靠性、耐用性和安全性,系統(tǒng)化的檢測流程成為產(chǎn)品出廠前及服役周期中的關(guān)鍵環(huán)節(jié)。檢測內(nèi)容需覆蓋材料特性、運動性能、潤滑效果及環(huán)境適應性等維度,通過多維度數(shù)據(jù)驗證設計參數(shù)與實際工況的匹配度,從而避免因微小缺陷導致的系統(tǒng)性失效風險。
核心檢測項目及方法
1. 外觀與尺寸精度檢測
通過高倍率工業(yè)顯微鏡和三維坐標測量儀,對軸承內(nèi)外圈表面進行100%全檢,重點排查劃痕、凹坑、氧化斑點等缺陷,同時驗證溝道曲率半徑、游隙公差等關(guān)鍵尺寸是否符合GB/T 304.3-2019標準。特殊涂層厚度需采用渦流測厚儀進行多點抽樣檢測,確保復合潤滑層厚度偏差≤±0.005mm。
2. 自潤滑性能測試
在專用摩擦磨損試驗機上模擬實際擺動工況(擺動角±15°,頻率0.5Hz),通過連續(xù)72小時耐久試驗記錄摩擦系數(shù)變化曲線。采用紅外光譜儀分析磨屑成分,結(jié)合接觸電阻法評估潤滑膜完整性。標準要求穩(wěn)態(tài)摩擦系數(shù)≤0.12,且磨痕寬度不得超過滾道寬度的15%。
3. 擺動疲勞壽命試驗
依據(jù)GJB 920A-2019軍用標準搭建多軸加載測試平臺,施加額定動載荷的120%進行加速壽命測試。通過聲發(fā)射傳感器實時監(jiān)測微裂紋擴展情況,結(jié)合高速攝像系統(tǒng)捕捉異常振動信號。合格判定需滿足50萬次擺動循環(huán)后,扭矩波動值仍低于初始值的30%。
4. 環(huán)境適應性驗證
在氣候箱中進行極端環(huán)境模擬:-55℃低溫冷啟動測試驗證潤滑劑低溫流動性,150℃高溫老化試驗評估PTFE基復合材料的熱穩(wěn)定性。鹽霧試驗按ISO 9227標準執(zhí)行96小時,要求腐蝕面積率<0.5%。真空環(huán)境(10^-3Pa)下的真空冷焊傾向性測試則用于航天應用場景驗證。
5. 無損檢測與失效分析
采用相控陣超聲檢測技術(shù)對軸承基體進行內(nèi)部缺陷掃描,檢測靈敏度需達到Φ0.4mm平底孔當量。對失效樣品進行斷口SEM分析,結(jié)合EDS能譜查明裂紋源及腐蝕產(chǎn)物成分,建立失效模式數(shù)據(jù)庫以優(yōu)化生產(chǎn)工藝。
檢測技術(shù)的發(fā)展趨勢
隨著工業(yè)4.0技術(shù)的普及,基于數(shù)字孿生的虛擬檢測技術(shù)開始應用于軸承性能預測。通過植入微型MEMS傳感器實時采集溫度、應變、振動等多物理場數(shù)據(jù),結(jié)合機器學習算法構(gòu)建健康狀態(tài)評估模型。同時,基于機器視覺的在線檢測系統(tǒng)將檢測效率提升300%,實現(xiàn)100μm級缺陷的自動識別與分類,推動行業(yè)向智能化檢測方向邁進。

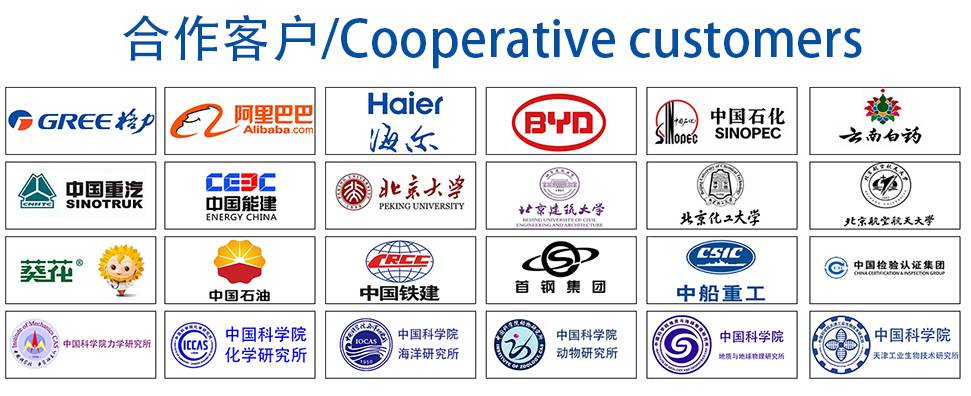