車用壓縮氫氣鋁內膽碳纖維全纏繞氣瓶檢測的重要性
隨著氫燃料電池汽車的快速發展,車用壓縮氫氣鋁內膽碳纖維全纏繞氣瓶(以下簡稱“氫氣瓶”)作為氫能儲存的核心部件,其安全性和可靠性備受關注。這類氣瓶采用輕量化鋁內膽結合高強度碳纖維全纏繞結構,具有耐高壓、耐腐蝕、重量輕等優勢,但長期在高壓、振動、溫度變化等復雜工況下運行,仍需通過嚴格檢測確保性能穩定。檢測項目不僅涉及氣瓶的物理強度、密封性,還包括材料耐久性、環境適應性等多維度評估,是保障氫能汽車安全運行的關鍵環節。
主要檢測項目及技術要點
1. 材料性能檢測
氫氣瓶的鋁內膽和碳纖維纏繞層需分別進行材料性能測試。鋁內膽需檢測抗拉強度、延伸率及微觀缺陷(如氣孔、裂紋);碳纖維則需評估纖維樹脂復合材料的層間剪切強度、纖維含量及均勻性。通過金相分析、掃描電鏡(SEM)等手段驗證材料是否符合GB/T 35544-2017等國家標準。
2. 氣密性檢測
采用氦氣檢漏法或水壓浸泡法,在額定工作壓力(通常為35MPa或70MPa)的1.25倍壓力下測試氣瓶的密封性能。微小泄漏可能導致氫氣積聚引發安全隱患,因此需確保泄漏率低于0.01 NL/h的行業標準。
3. 循環壓力測試
模擬實際使用中頻繁充放氫氣的工況,對氣瓶進行數萬次(如15,000次)壓力循環試驗。過程中需監測氣瓶變形量、殘余應變及纖維層是否出現剝離或斷裂,驗證其抗疲勞性能。
4. 爆破壓力測試
通過逐步加壓直至氣瓶失效,測定實際爆破壓力是否達到設計值的2.25倍以上。試驗需記錄爆破位置、形態及能量釋放特性,以評估氣瓶的極限承載能力。
5. 環境適應性測試
包括高低溫沖擊試驗(-40℃至85℃)、鹽霧腐蝕試驗及振動沖擊試驗,模擬極端氣候和復雜路況下的性能表現。重點關注溫度驟變對材料界面結合力的影響,以及振動是否導致結構損傷。
6. 殘余強度評估
在氣瓶表面制造人工損傷(如劃痕、撞擊凹痕)后,測試其剩余爆破壓力和循環壽命,確保即使發生意外碰撞仍能保持安全閾值。損傷深度通常不超過碳纖維層厚度的10%。
檢測技術發展趨勢
隨著氫能產業規模化,檢測技術正向智能化、高效化發展。聲發射(AE)技術可實時監測氣瓶內部缺陷擴展,X射線計算機斷層掃描(CT)能精確識別微觀結構異常。此外,數字孿生技術結合大數據分析,正在構建氣瓶全生命周期的健康管理模型,進一步提升檢測效率和可靠性。
結語
車用壓縮氫氣瓶的檢測不僅是產品合規的必經流程,更是氫能交通安全的基石。通過多維度、高精度的檢測體系,可最大程度降低氫氣泄漏、爆燃等風險,為氫燃料電池汽車的商業化普及提供關鍵保障。

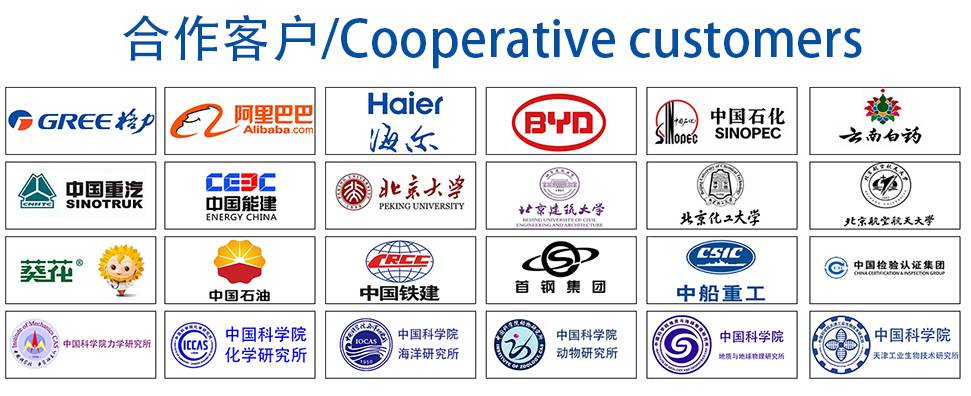