管件檢測的重要性與核心內容
在石油化工、能源輸送、建筑管道等工業領域,管件作為連接、轉向和控制流體的關鍵部件,其質量直接影響著系統的安全性與使用壽命。據統計,約35%的管道事故由管件質量問題引發,因此管件檢測已成為生產流程中不可或缺的環節。通過科學規范的檢測手段,不僅能驗證管件尺寸精度、材料強度等基礎指標,更能發現潛在缺陷,避免因腐蝕、裂紋或焊接缺陷導致的泄漏、爆炸等重大風險。現代檢測技術已覆蓋從原材料驗證到成品驗收的全生命周期管理,為工程安全筑起堅實防線。
管件檢測核心項目解析
1. 尺寸精度檢測
使用三坐標測量儀、光學投影儀對管件的直徑、壁厚、彎曲半徑等關鍵幾何參數進行微米級測量,確保符合GB/T 12459、ASME B16.9等標準要求,特別是對法蘭面平行度、螺紋配合精度等裝配關鍵部位實施100%檢測。
2. 力學性能測試
通過萬能試驗機完成拉伸、彎曲、沖擊試驗,重點檢測屈服強度(≥245MPa)、抗拉強度(≥415MPa)及延伸率(≥30%),模擬管件在高壓、震動等極端工況下的承載能力。硬度測試采用布氏/洛氏硬度計,確保材料硬度值在HB 130-180合理區間。
3. 化學成分分析
運用直讀光譜儀對碳鋼、不銹鋼、合金鋼等材質的C、Mn、Cr、Ni等元素含量進行精確測定,比對GB/T 699、ASTM A234等標準,防止材料摻雜導致的耐腐蝕性下降。X射線熒光光譜(XRF)可實現現場快速篩查。
4. 無損檢測(NDT)
采用超聲波探傷(UT)檢測壁厚均勻性與內部氣孔,磁粉檢測(MT)發現表面微裂紋,滲透檢測(PT)識別0.01mm級以上開口缺陷。對于高壓管件,100%實施射線檢測(RT),確保焊接區域無未熔合、夾渣等缺陷。
5. 耐壓與氣密性試驗
根據TSG D7001標準進行1.5倍工作壓力的水壓試驗,保壓時間≥30分鐘。氣體管路需額外進行氦質譜檢漏,泄漏率控制在1×10?? Pa·m3/s以下,特殊工況下實施-196℃深冷循環試驗驗證低溫密封性。
6. 表面質量評估
使用表面粗糙度儀檢測Ra≤3.2μm的標準,內窺鏡檢查內壁氧化皮殘留。防腐涂層需通過劃格法測試附著力(≥3級),鹽霧試驗驗證500小時無紅銹,電火花檢測確保3.5kV電壓下無針孔缺陷。
全過程質量管控體系
現代管件檢測已形成"原料入廠-過程監控-成品檢驗-使用跟蹤"的四級管理體系。通過MES系統實現檢測數據實時上傳,運用SPC統計過程控制技術分析質量波動趨勢。第三方實驗室 認證報告與二維碼追溯系統的結合,使每件管件具備完整的"質量身份證",為工程安全提供雙重保障。

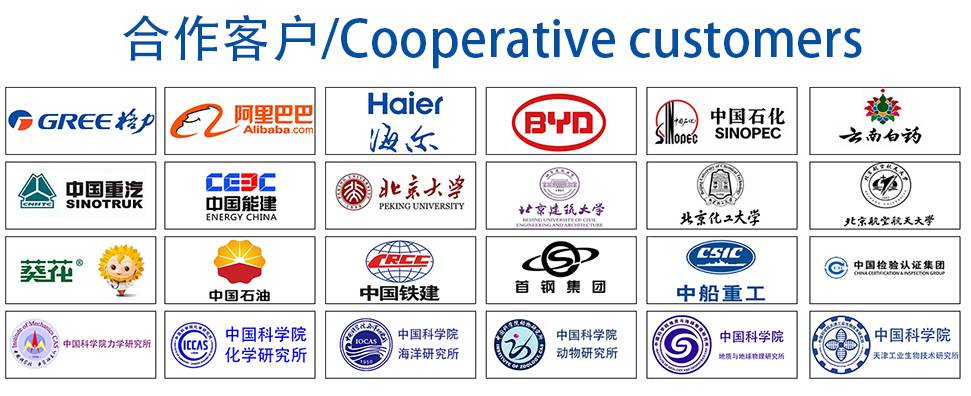