燃料電池模塊作為氫能技術的核心部件,其性能、安全性和可靠性直接影響著燃料電池系統的整體表現。隨著氫能產業的快速發展,燃料電池在交通運輸、分布式發電等領域的應用日益廣泛,而模塊檢測成為保障產品質量的關鍵環節。通過系統化的檢測項目,能夠評估模塊的電化學性能、機械強度、環境適應性以及安全防護能力,確保其滿足行業標準和使用需求。
一、電堆性能檢測
電堆是燃料電池模塊的核心單元,檢測需覆蓋電壓一致性、單電池內阻、極化曲線等關鍵指標。采用多點電壓巡檢設備實時監測各單電池輸出穩定性,并通過電化學阻抗譜(EIS)分析質子交換膜與催化層的工作狀態。耐久性測試需模擬啟停循環、變載工況,驗證電堆在2000小時連續運行下的性能衰減率。
二、氫氣供給系統檢測
氫氣子系統檢測包含氣密性驗證、壓力波動測試和流量控制精度評估。使用氦氣質譜檢漏儀檢測管路連接處泄漏率,確保數值低于10-6 mbar·L/s。通過動態壓力循環測試驗證減壓閥、比例閥的響應速度,同時檢測供氫系統在低溫(-40℃)環境下的防凍結能力。
三、熱管理系統檢測
冷卻液流量均勻性檢測需確保各電堆單元溫差≤3℃。采用紅外熱像儀監測模塊散熱片溫度分布,驗證散熱設計有效性。耐腐蝕測試要求冷卻管路在乙二醇溶液(50%濃度)中持續運行500小時無滲漏,并評估防凍液對金屬部件的電化學腐蝕影響。
四、安全防護檢測
按照GB/T 24549標準進行氫氣泄漏報警測試,傳感器需在濃度達到1%vol時實現0.5秒內響應。過壓保護裝置需在1.25倍工作壓力下自動啟動泄壓閥。緊急停機功能測試包括電源切斷響應時間、殘余電荷釋放效率等,確保故障發生時系統可在200ms內完成安全隔離。
五、環境適應性檢測
高低溫循環測試需在-30℃至85℃范圍內進行20次熱沖擊試驗。振動測試模擬車輛行駛工況,施加X/Y/Z三軸各100小時隨機振動(5-2000Hz)。鹽霧試驗按照ISO 9227標準執行720小時測試,檢測外殼防護等級是否達到IP67要求。
通過上述五大類38項專項檢測,可全面評估燃料電池模塊的工程化應用能力。隨著檢測技術向原位診斷、數字孿生方向發展,未來將實現更精準的故障預測與壽命評估,為氫能裝備的規模化應用提供技術保障。

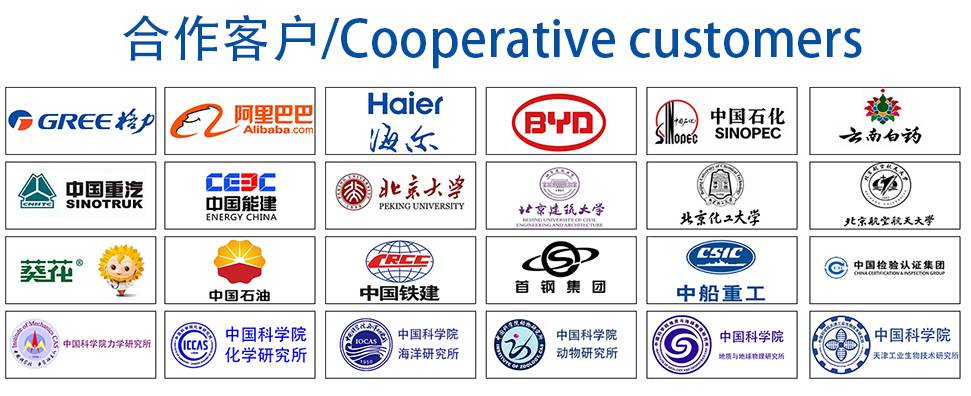