摩托車用鋰電池檢測:守護安全的關鍵防線
隨著新能源技術的快速發展,鋰電池憑借高能量密度、輕量化等優勢,正逐步取代傳統鉛酸電池成為摩托車動力系統的重要組成。然而,鋰電池在充放電過程中存在熱失控、短路等安全隱患,尤其摩托車行駛環境復雜多變,對電池的可靠性提出更高要求。建立完善的鋰電池檢測體系,已成為保障車輛安全運行、延長電池壽命、維護消費者權益的行業共識。國際標準化組織(ISO)與各國監管部門已針對動力電池出臺超過20項強制性檢測標準,覆蓋從原料到成品的全生命周期管理。
核心檢測項目體系
安全性能測試
過充/過放保護測試:模擬異常充電電壓(通常設定為標稱電壓的1.5倍)持續24小時,驗證BMS保護系統的響應速度與切斷精度。短路測試通過強制正負極接觸,檢測電池在極端短路情況下是否能在150ms內啟動保護機制,外殼溫度需控制在80℃以下。
電化學性能驗證
容量衰減測試要求電池在標準充放電循環500次后,容量保持率不低于初始值的80%。低溫啟動測試需在-20℃環境下持續放電至終止電壓,驗證電解液低溫導電性能。脈沖放電測試模擬急加速工況,檢測瞬時大電流(通常為3C倍率)輸出時的電壓穩定性。
機械結構可靠性
振動測試按照GB/T31467.3標準進行XYZ三軸隨機振動,頻率范圍5-2000Hz,持續時間不少于24小時。跌落測試從1.2米高度進行6面3次自由跌落,要求外殼無破裂、電解液無泄漏。擠壓測試采用半徑75mm的半球體施加13kN壓力,保持10分鐘后監測是否發生熱失控。
環境適應性評估
濕熱循環測試需在溫度40℃±2℃、濕度95%RH環境中持續720小時,驗證密封件老化情況。海拔模擬測試通過低壓艙模擬5000米高原環境,檢測氣壓變化對電池殼體形變的影響。鹽霧腐蝕測試依據ISO9227標準進行96小時中性鹽霧試驗,評估金屬部件的耐腐蝕等級。
智能化檢測新趨勢
當前檢測技術正向數字化、智能化方向發展,部分實驗室已引入AI視覺檢測系統,通過高分辨率熱成像儀實時監測測試過程中電池表面的溫度場分布,結合大數據分析預測潛在失效模式。某知名檢測機構最新研發的電池云端監控平臺,能夠同步采集2000+電芯的電壓、溫度數據,檢測效率提升300%。
完善的檢測體系不僅需要齊全的設備支撐,更依賴專業的技術團隊。國內領先的檢測機構已建立包含電化學博士、安全工程師在內的跨學科團隊,提供從單體電芯到電池包系統的全套解決方案。消費者在選擇鋰電池產品時,應重點關注是否通過GB38031-2020《電動汽車用動力蓄電池安全要求》等強制性認證,以及是否具備UN38.3運輸安全測試報告。

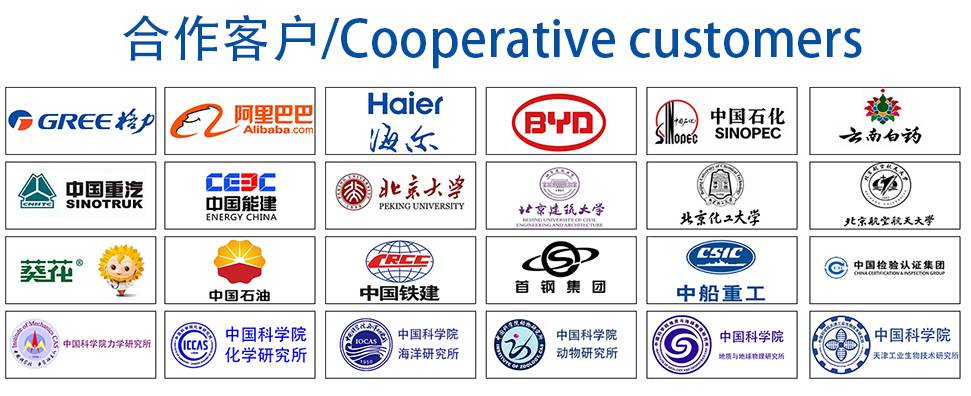