密閉翼環檢測的重要性與核心內容
密閉翼環作為管道系統、壓力容器及特殊設備中關鍵的密封組件,其性能直接影響設備運行安全性與介質防泄漏能力。在石油化工、核電、醫藥制造等高危行業,密閉翼環的失效可能導致嚴重的安全事故、環境污染或生產中斷。因此,系統化的密閉翼環檢測成為設備維護與質量控制的核心環節,需通過科學的檢測項目驗證其設計強度、密封效能及耐久性,確保符合GB/T 12459、ASME B16.9等國家標準或國際規范要求。
密閉翼環檢測核心項目
1. 幾何尺寸與形位公差檢測
使用三維坐標測量儀、激光掃描儀等設備,檢測翼環的內外徑、環體厚度、螺栓孔間距等關鍵尺寸,驗證與設計圖紙的吻合度。重點檢測密封面的平面度、表面粗糙度(Ra≤3.2μm),確保安裝后接觸面緊密無縫隙。
2. 材料成分與力學性能檢測
通過光譜分析儀進行材質驗證,確認不銹鋼、哈氏合金等材料的元素含量符合ASTM A182標準。開展拉伸試驗(屈服強度≥205MPa)、沖擊試驗(-46℃低溫沖擊功≥27J)及硬度測試(HB≤187),評估材料在極端工況下的抗變形能力。
3. 密封性能壓力測試
采用液壓試驗臺進行1.5倍工作壓力的靜態保壓測試,持續時間≥30分鐘,觀察有無滲漏或變形。對于氣體介質系統,需額外進行氦質譜檢漏,泄漏率需≤1×10?? Pa·m3/s,確保在動態工況下的氣密性。
4. 腐蝕防護與表面質量檢測
運用金相顯微鏡檢查鍍層(如鍍鋅、鍍鎳)厚度(30-50μm)及結合力,通過鹽霧試驗(500小時)評估耐腐蝕性。使用滲透探傷(PT)或磁粉探傷(MT)檢測表面微裂紋,缺陷長度應≤0.8mm且無貫穿性裂紋。
5. 安裝配合與疲勞壽命測試
模擬實際工況進行5000次以上的循環加載試驗,檢測翼環與法蘭的配合間隙(≤0.05mm)變化,同時通過有限元分析(FEA)評估應力分布情況,預測在交變載荷下的疲勞壽命是否達到10萬次循環要求。
檢測結果的應用與發展趨勢
通過上述檢測項目生成的量化數據,可為設備安全評級、維修周期制定提供科學依據。隨著智能傳感技術的應用,未來將逐步實現翼環狀態在線監測,結合大數據分析提前預警失效風險,推動檢測方式從定期維護向預測性維護轉型。

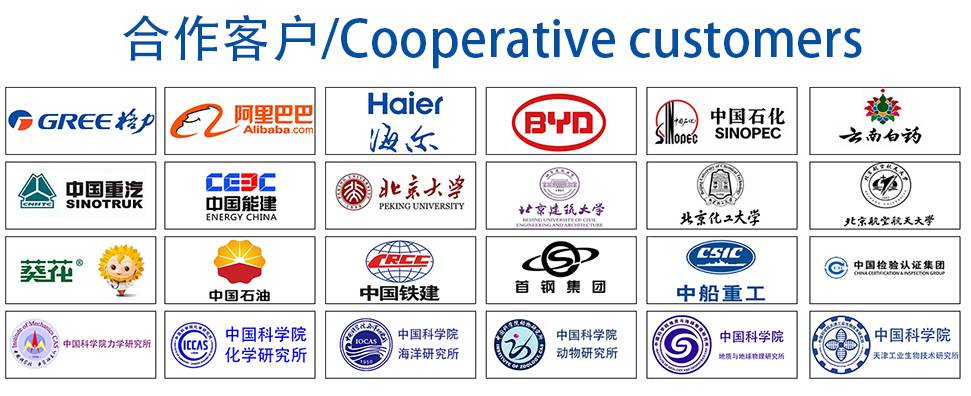