密閉閥門檢測:保障工業安全的核心環節
在石油化工、供熱管網、核電站等特殊工業場景中,密閉閥門作為流體控制系統的重要安全屏障,其性能直接關系到生產安全和環境保護。近年來,因閥門泄漏引發的重大事故屢見報端,使得密閉閥門的定期檢測成為行業監管的重點。依據《TSG D7002-2020壓力管道元件型式試驗規則》及API 598標準要求,一套完整的密閉閥門檢測體系需要覆蓋從基礎性能到極端工況模擬的全方位驗證。
關鍵檢測項目解析
1. 密封性能試驗
采用正壓法/負壓法進行氣密性測試,通過精度達0.25級的壓力傳感器記錄泄漏量。高壓密封試驗需維持1.1倍額定壓力30分鐘,低壓密封(如6bar氮氣)保持15分鐘,泄漏率應低于國際標準化組織ISO 5208規定的A級標準。對于雙向密封閥門,需分別進行雙向加壓測試。
2. 殼體強度試驗
按照ASME B16.34標準,以1.5倍公稱壓力持續施壓。鑄鋼閥門保壓時間不少于3分鐘,焊接閥門延長至5分鐘。試驗過程中借助超聲波測厚儀實時監控壁厚變化,殼體表面不得出現可見滲漏或永久變形。
3. 操作扭矩測試
使用數字式扭矩測量儀記錄閥門從全關到全開過程的扭矩曲線。對比初始裝配數據和周期檢測數據,當操作扭矩增幅超過20%時,提示可能存在閥桿變形、填料老化或密封面損傷等問題。
4. 材料完整性檢測
采用相控陣超聲波檢測技術(PAUT)對閥體關鍵部位進行掃查,檢測靈敏度達到φ2mm當量平底孔。光譜分析儀用于驗證材料成分,確保與設計證書的鉻、鉬等合金元素含量偏差不超過±0.5%。
5. 火災安全測試
依據API 607標準進行火燒試驗,在650℃高溫環境下保持30分鐘,測試后仍需滿足低壓密封要求。防火填料在灼燒后應形成致密碳化層,且外漏通道的泄漏量不超過150mL/min。
6. 低溫性能驗證
對LNG用超低溫閥門進行-196℃液氮深冷處理,檢測材料沖擊韌性變化。保冷層經48小時低溫循環后,表面凝露面積不得超過總面積的5%,確保低溫工況下的密封可靠性。
檢測周期與維護建議
根據NACE SP0592標準,常規工業閥門應每年進行在線檢測,每3年實施解體大檢。對于核級閥門等特殊設備,需建立基于風險檢驗(RBI)的動態管理機制。建議采用智能閥門診斷系統,通過內置傳感器實時監測應力應變、溫度梯度等參數,實現預測性維護。
通過建立包含上述檢測項目的完整質量管控體系,可有效將閥門故障率降低70%以上。特別是在氫能儲運、碳捕集等新興領域,嚴格的檢測程序已成為保障新型介質安全輸送的關鍵技術支撐。

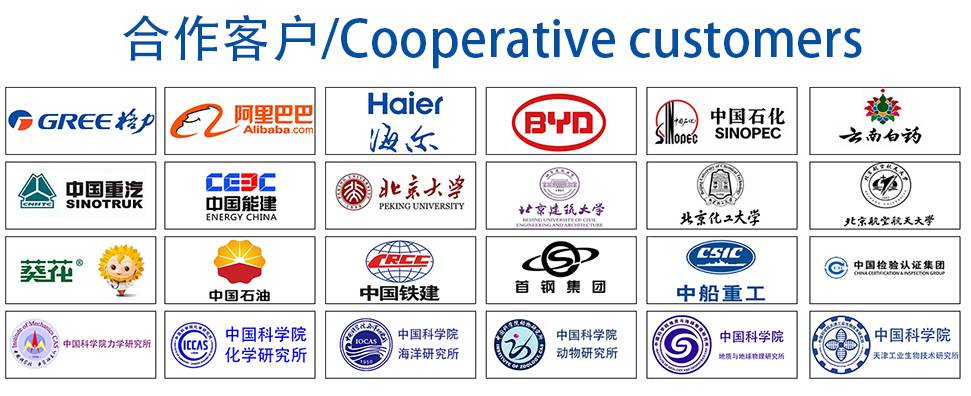