密封圈檢測的重要性與行業應用
密封圈作為工業設備、汽車部件、航空航天等領域的關鍵元件,其性能直接影響系統的密封效果與安全性。在高壓、高溫、腐蝕性介質等復雜工況下,密封圈的失效可能導致設備泄漏、環境污染甚至安全事故。因此,通過系統化的密封圈檢測項目,評估其物理性能、化學穩定性及耐久性,成為保障產品質量的核心環節。國際標準如ISO 3601、ASTM D2000等均對密封圈檢測提出了明確要求,覆蓋從原材料到成品全生命周期的質量驗證。
密封圈檢測的核心項目
1. 尺寸與幾何精度檢測
通過光學投影儀、三坐標測量儀(CMM)等設備,檢測密封圈的內外徑、截面厚度、圓度及表面平整度。重點驗證是否符合設計公差(通常要求±0.1mm以內),確保與配合部件的裝配適配性。
2. 材料性能測試
包括硬度(邵氏A/D)、拉伸強度、斷裂伸長率等指標檢測。例如:橡膠材料需滿足ASTM D412標準,氟橡膠(FKM)的典型硬度范圍在70-90 Shore A,拉伸強度需≥10MPa。同步開展熱老化測試(如70℃×72h)評估材料穩定性。
3. 密封性能驗證
采用氣密性試驗臺或液壓測試系統,模擬實際工況壓力(可達50MPa)。記錄泄漏量、形變恢復率等數據,例如汽車燃油系統密封圈需通過SAE J1203標準要求的1000次壓力循環測試。
4. 耐介質與耐候性測試
將密封圈浸泡于燃油、潤滑油、酸堿溶液等介質中(按ISO 1817標準),檢測體積膨脹率(通常要求<15%)和質量變化。同時進行紫外線老化、臭氧暴露試驗(ASTM D1149),評估抗龜裂性能。
5. 動態工況模擬檢測
通過往復運動試驗機模擬密封圈在活塞、旋轉軸等場景下的長期磨損情況。記錄摩擦系數變化,分析唇口磨損量(如要求500萬次循環后磨損深度≤0.2mm),驗證使用壽命。
檢測技術的創新方向
隨著工業4.0發展,密封圈檢測正朝著智能化方向升級。例如:采用機器視覺自動識別表面缺陷,利用有限元分析(FEA)預測密封接觸應力分布,以及基于AI算法的壽命預測模型。這些技術將進一步提升檢測效率與精度,為高端裝備制造提供更可靠的質量保障。

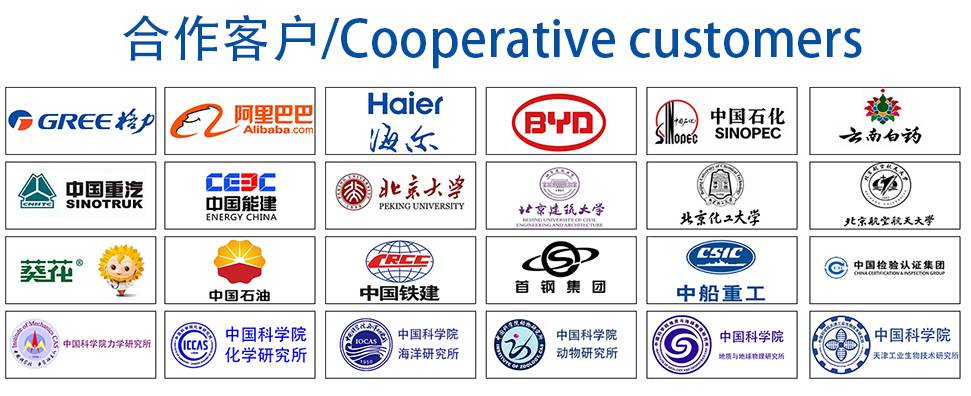