彈簧直接載荷式安全閥檢測的重要性
彈簧直接載荷式安全閥作為壓力容器、鍋爐、管道等承壓設備的關鍵安全附件,其性能直接關系到設備的安全運行和人員生命財產安全。該類型安全閥通過彈簧預緊力與介質壓力的平衡實現啟閉功能,長期使用中可能因彈簧疲勞、密封面磨損、異物卡阻等問題導致失效。定期開展檢測工作,可有效驗證其動作可靠性、密封性能及排放能力,確保符合TSG 21-2016《固定式壓力容器安全技術監察規程》、GB/T 12241《安全閥一般要求》等標準要求,避免因安全閥故障引發的超壓事故。
關鍵檢測項目及技術要求
1. 外觀與結構檢查
使用目視檢測和量具對閥體、閥座、閥瓣、彈簧等部件進行外觀檢查,要求無裂紋、腐蝕、變形等缺陷;核對銘牌信息(型號、整定壓力、制造許可證號)是否完整清晰;檢查彈簧自由高度、同心度是否符合設計要求,彈簧表面應無銹蝕或永久變形。
2. 密封性能試驗
采用液壓或氣壓試驗方法,在90%整定壓力下保壓3分鐘,觀察泄漏情況。根據GB/T 12243標準,允許泄漏率應≤20氣泡/min(液體介質)或通過聽音法判定無持續泄漏(氣體介質)。密封面粗糙度需達到Ra0.8μm以下,接觸寬度不小于閥座密封面寬度的80%。
3. 整定壓力校驗
使用專用校驗臺進行壓力整定測試,重復三次取平均值。允許偏差為±3%整定壓力(當整定壓力≤0.5MPa時允許±0.015MPa)。測試過程中需記錄開啟高度、回座壓力等參數,回座壓力與整定壓力比值應≥80%。
4. 彈簧性能測試
通過彈簧試驗機測量彈簧剛度系數,允許偏差不超過設計值的±10%;檢測殘余變形量(加載至1.5倍工作載荷后,永久變形量應<0.5%自由高度);進行疲勞壽命測試(≥50000次循環無斷裂或剛度衰減)。
5. 排放與復位性能驗證
全量程排放試驗時,安全閥應在達到額定排放壓力后穩定開啟,排放系數不低于0.9;測試后閥瓣應自動回座至密封狀態,無卡滯現象。需特別注意高溫、低溫等極端工況下的動作特性驗證。
6. 材料理化分析
對關鍵部件進行材質復核,包括光譜分析(驗證材料牌號)、硬度測試(彈簧HRC44-52,閥瓣HB180-250)、金相組織檢查(無脫碳、過熱等異常)。密封面堆焊層厚度應≥3mm,結合強度需通過超聲波檢測驗證。
檢測周期與數據管理
根據TSG規范要求,安全閥應每年至少進行一次在線校驗,每3年進行解體檢測。所有檢測數據需完整記錄,建立數字化檔案,異常情況應進行失效分析并制定改進方案,確保設備全生命周期的可追溯性。

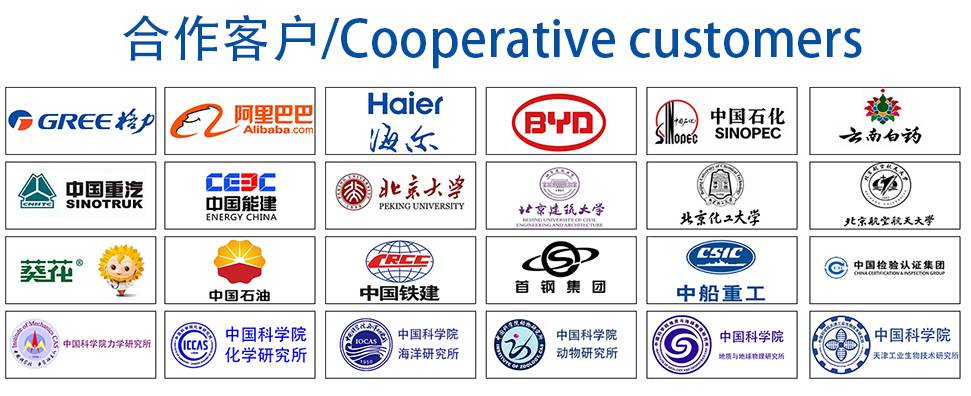