金屬波紋管膨脹節檢測的必要性與重要性
金屬波紋管膨脹節作為管道系統中補償位移、減振降噪的關鍵部件,廣泛應用于石油化工、電力、冶金等領域。長期受介質壓力、溫度變化及機械振動影響,其波紋管、法蘭、導流筒等部位易出現疲勞裂紋、腐蝕、變形等缺陷,可能引發泄漏甚至系統失效。因此,定期開展金屬波紋管膨脹節檢測是保障工業裝置安全運行、預防事故的核心措施。檢測需結合外觀檢查、性能測試、材料分析等多維度手段,依據GB/T 12777、EJMA等標準規范,確保膨脹節的承壓能力、補償性能及結構完整性滿足設計要求。
金屬波紋管膨脹節主要檢測項目
1. 外觀與幾何尺寸檢測
通過目視、放大鏡或工業內窺鏡檢查波紋管表面是否存在裂紋、凹陷、腐蝕穿孔及焊接缺陷,測量波紋高度、波距、層數是否符合設計值。使用卡尺、超聲波測厚儀檢測管壁減薄情況,單邊減薄量超過10%時需判定是否報廢。
2. 壓力試驗與氣密性測試
對膨脹節進行1.5倍設計壓力的液壓試驗,保壓10分鐘無滲漏;爆破壓力試驗需達到3倍設計壓力以上。采用氦質譜檢漏法或肥皂水涂抹法驗證氣密性,泄漏率應小于1×10?? Pa·m3/s。
3. 疲勞壽命與剛度測試
模擬實際工況進行循環次數試驗(通常≥1000次),檢測波紋管是否出現疲勞裂紋。通過軸向/橫向剛度試驗驗證膨脹節的彈性特性,剛度偏差需控制在±15%以內。
4. 材料成分與金相分析
采用光譜儀檢測波紋管材料(如316L、Inconel 625)的化學成分,對比ASTM標準要求。金相顯微鏡觀察晶粒度、夾雜物及熱處理狀態,避免材料劣化導致強度下降。
5. 無損檢測(NDT)
對焊縫及應力集中區域進行滲透檢測(PT)、磁粉檢測(MT)或射線檢測(RT),發現表面及近表面缺陷;超聲波測厚(UT)評估內部腐蝕情況,重點關注U形波谷部位。
6. 位移補償能力驗證
通過三坐標測量儀測試軸向壓縮/拉伸、橫向剪切及角向偏轉量是否滿足標稱補償值,同時監測波紋管局部屈曲變形情況,確保位移過程中無失穩現象。
檢測周期與結果處理
常規檢測周期建議為1-2年,高溫、腐蝕性介質環境下應縮短至6個月。若發現波紋管存在穿透性裂紋、嚴重減薄或殘余變形超過20%,應立即更換。檢測數據需存檔分析,結合運行參數優化維護策略,延長膨脹節使用壽命。

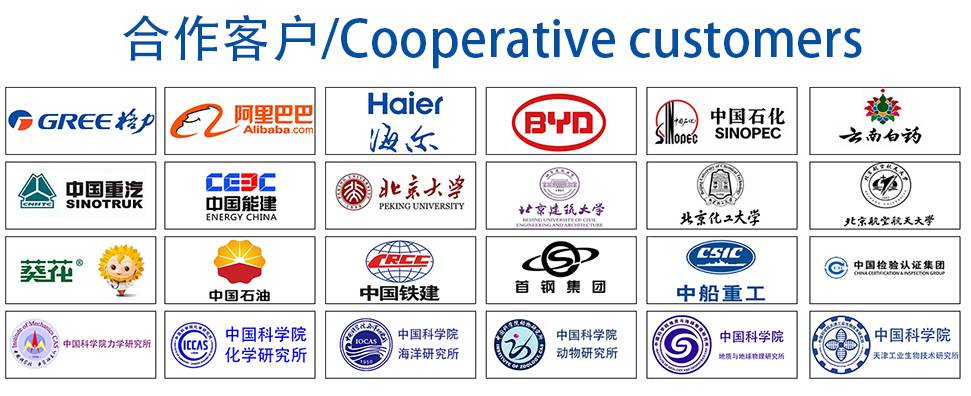