聚乙烯電熔組件檢測的重要性與核心內容
聚乙烯電熔組件作為管道系統中的關鍵連接部件,廣泛應用于燃氣輸配、給排水、工業流體輸送等領域。其質量直接關系到管道系統的密封性、耐壓性和使用壽命。由于電熔連接涉及高溫熔融、材料融合等復雜工藝,組件在焊接過程中易受材料性能、操作工藝及環境因素的影響。因此,通過科學、系統的檢測手段對聚乙烯電熔組件進行全面評估,是保障工程安全、預防泄漏事故的重要環節。
聚乙烯電熔組件的核心檢測項目
1. 外觀與尺寸檢測
通過目視檢查和精密測量工具(如卡尺、激光測距儀)驗證組件表面是否光滑無氣泡、裂紋或雜質;檢查電熔套筒的電阻絲排列是否均勻,同時測量管材與套筒的直徑、壁厚是否符合設計要求。偏差超過標準(如ISO 21307或GB/T 32439)可能導致焊接強度不足。
2. 熔接界面質量檢測
采用非破壞性檢測技術(如X射線成像、超聲波探傷)分析熔接界面是否形成均勻的熔融層,觀察是否存在孔洞、未熔合或冷焊現象。破壞性測試(如剝離試驗)可進一步驗證熔接面結合強度是否達到標準(如ASTM F2634)。
3. 壓力與密封性能測試
通過液壓或氣壓試驗模擬實際工況,驗證組件在標稱壓力(如1.5倍工作壓力)下的耐壓能力,并監測保壓階段的壓力衰減值。使用氦氣檢漏儀等設備檢測微觀泄漏,確保密封性能滿足EN 1555或CJJ 63等規范要求。
4. 材料性能驗證
對電熔套筒及管材進行熔體流動速率(MFR)、氧化誘導時間(OIT)、密度等理化指標測試,判斷原材料是否符合PE80/PE100等級要求。熱重分析(TGA)可檢測是否摻雜再生料,紅外光譜(FTIR)用于鑒別材料成分異常。
5. 焊接工藝參數復核
核查焊接設備的電壓、電流、加熱時間等參數是否與管材規格匹配,并通過熱電偶記錄熔融區溫度曲線,確保符合制造商工藝規范。數據記錄儀的實時監測可追溯焊接過程是否出現異常波動。
檢測標準與認證要求
國內外主流檢測標準包括ISO 13954(剝離試驗)、GB/T 32439(電熔管件)、AS/NZS 4130(聚乙烯管道)等。第三方檢測機構需具備CMA/ 資質,檢測報告應包含焊接參數記錄、缺陷位置圖譜及材料性能數據,為工程驗收提供法定依據。
通過上述多維度的檢測手段,可系統評估聚乙烯電熔組件的可靠性,最大限度降低管道系統運行風險,為城市基礎設施的安全運營提供有力保障。

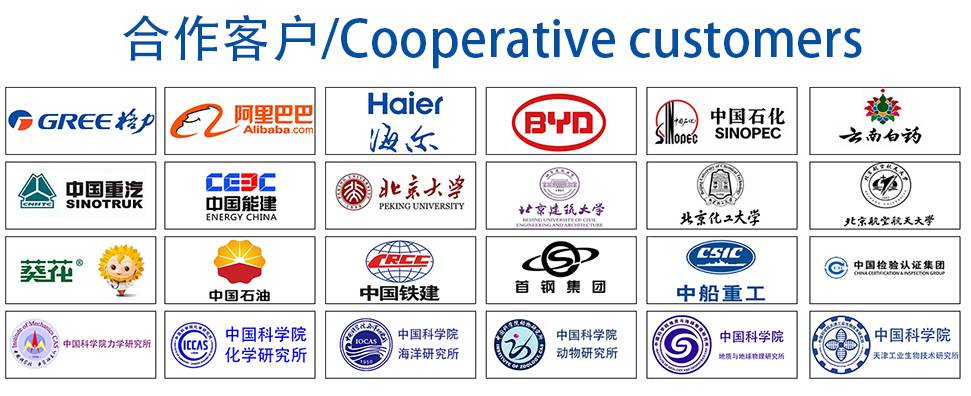