電工電子產品著火危險試驗檢測的重要性
在電工電子產品設計與生產過程中,著火危險試驗檢測是保障產品安全性的核心環節。隨著電子設備復雜度提升和功率密度增加,因電路短路、元件過熱或材料易燃引發的火災風險顯著上升。該檢測通過模擬極端使用環境、電氣故障及材料失效場景,驗證產品抗火性能是否符合國際標準(如IEC 60695系列、GB/T 5169等),避免因設計缺陷導致用戶財產損失甚至人身傷害。尤其對家用電器、新能源汽車電池系統、工業控制設備等高危領域,檢測結果直接影響產品的市場準入與消費者信任。
主要檢測項目與測試方法
1. 材料可燃性測試:評估外殼、絕緣材料等關鍵部件的阻燃等級,常用UL94垂直燃燒試驗和灼熱絲試驗(Glow-Wire Test),檢測材料在接觸火源后的自熄時間和燃燒擴散性。
2. 過載與短路模擬試驗:通過人為制造電路過載或短路故障,監測產品內部溫度變化、電弧產生情況及是否引發明火,驗證保護裝置(如保險絲、斷路器等)的響應有效性。
3. 故障電弧檢測:針對高壓設備(如充電樁、變壓器),使用專用裝置模擬電弧放電,分析電弧能量釋放對周圍材料的引燃風險,確保防護結構設計達標。
4. 熱失控評估:針對鋰電池等儲能器件,通過加熱、針刺或過充方式觸發熱失控,監測火焰蔓延速度和煙霧毒性,為熱管理系統優化提供依據。
檢測流程與標準合規性
典型檢測流程包括預評估、樣品制備、實驗室測試及報告生成四個階段。企業需根據目標市場選擇對應標準體系(如歐盟CE認證的EN標準、中國CCC認證的GB標準),并確保測試機構具備 或ILAC資質。例如,灼熱絲試驗需嚴格遵循IEC 60695-2-11規定的溫度梯度(550℃-960℃)和接觸時間,而針焰試驗(IEC 60695-11-5)則聚焦小火焰對局部材料的引燃能力。
行業挑戰與技術發展趨勢
隨著快充技術、高密度集成電路的普及,傳統檢測方法面臨新挑戰。行業正推動智能化檢測設備(如AI熱成像分析系統)和仿真建模技術的應用,以更精準預測復雜工況下的著火風險。此外,環保阻燃材料的研發與檢測標準更新(如歐盟RoHS對溴化阻燃劑的限制)也在驅動測試方法的迭代升級。
結語
電工電子產品著火危險試驗檢測不僅是合規要求,更是企業社會責任的體現。通過系統性測試與持續改進,可大幅降低火災隱患,為產品安全構筑堅實防線。廠商應盡早介入檢測環節,從設計源頭優化防火性能,提升市場競爭力。

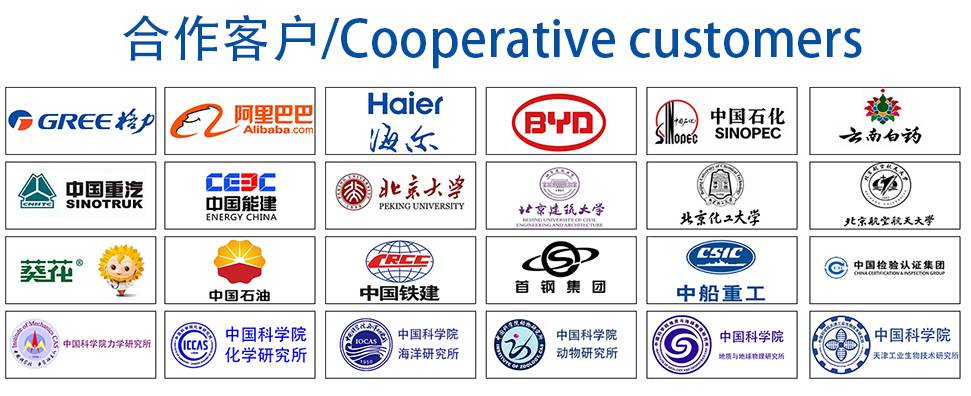