電動汽車用驅動電機系統檢測的重要性與發展背景
隨著新能源汽車產業的快速發展,驅動電機系統作為電動汽車的"心臟",其性能直接決定了車輛的動力輸出、續航里程和運行安全性。根據中國汽車工程學會統計,2023年我國新能源車電機系統市場規模已突破800億元,年檢測需求增長率達35%以上。驅動電機系統的檢測不僅關乎產品質量控制,更是實現"雙碳"目標下能效提升的核心環節。
行業標準GB/T 18488-2015《電動汽車用驅動電機系統》明確規定,驅動電機系統必須通過八大類36項關鍵性能檢測才能投入量產。這些檢測貫穿研發驗證、生產質檢和售后維護全生命周期,形成了覆蓋電氣性能、機械特性、環境適應性等多維度的完整檢測體系。
核心檢測項目體系解析
1. 電氣性能檢測
(1)效率特性測試:在額定電壓下,通過測功機系統測量電機在5%-150%負載范圍內的效率曲線,要求最高效率點不低于94%。采用ISO 8854標準中的MAP圖法繪制全工況效率圖譜。
(2)轉矩-轉速特性:使用高精度扭矩傳感器(精度±0.2%)測試堵轉轉矩、最大轉矩及恒功率區特性,驗證與設計值的偏差不超過±5%。
2. 環境適應性測試
(1)高低溫循環試驗:-40℃至120℃溫度沖擊測試,驗證繞組絕緣電阻(≥500MΩ)和密封件性能。某品牌電機在此項測試中出現密封圈脆化問題,促使行業改進材料耐候性標準。
(2)鹽霧腐蝕測試:按GB/T 2423.17標準進行96小時5%NaCl溶液噴霧,檢測殼體防護等級維持IP67的能力。
3. 電磁兼容性(EMC)檢測
(1)傳導發射測試:在30MHz-108MHz頻段,使用LISN網絡測量控制器的傳導干擾,要求低于CISPR 25 Class3限值。
(2)輻射抗擾度測試:依據ISO 11452-2標準,在電波暗室中進行200V/m場強輻射,確保系統功能不降級。
4. 耐久性驗證
(1)臺架耐久試驗:模擬整車工況進行2000小時連續交變負載測試,功率循環次數超100萬次,檢測軸承磨損和永磁體退磁情況。
(2)振動疲勞測試:按SAE J2380標準施加XYZ三軸隨機振動,峰值加速度達25g,驗證結構件抗疲勞性能。
前沿檢測技術發展趨勢
當前行業正加速應用數字孿生技術,通過構建電機系統的虛擬樣機,實現80%的檢測項目在仿真階段完成。某頭部企業采用AI驅動的預測性檢測系統,使故障預警準確率提升至92%。同時,基于碳化硅器件的高頻化檢測(開關頻率達100kHz)催生新型寬頻測量設備研發,推動檢測技術持續升級。
隨著國際電工委員會(IEC)正在制定的新版電動汽車電機標準,未來檢測體系將更強調系統級能效評價和網絡安全防護,驅動檢測方法向智能化、集成化方向深度演進。

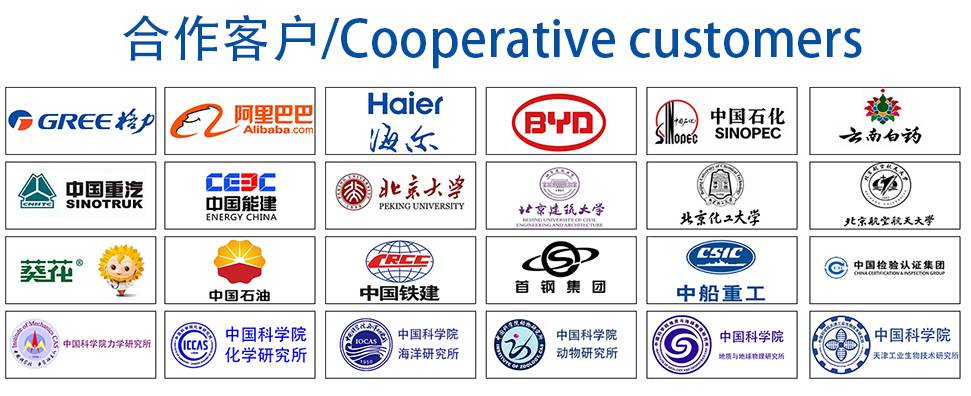