機械連接檢測的重要性及行業應用
在機械制造、航空航天、汽車工業等領域,機械連接作為結構承載的核心環節,其可靠性直接關系到整體設備的安全運行。據統計,機械失效案例中約35%源自連接部位的異常,這使得機械連接檢測成為質量管控的關鍵環節。隨著現代工業對精密制造要求的提升,檢測技術已從傳統目視檢查發展為涵蓋力學性能、材料特性、動態響應等多維度的系統性評估體系。
關鍵檢測項目分類與技術規范
1. 緊固件連接性能檢測
采用扭矩測試儀對螺栓/螺母進行預緊力驗證,配合超聲波應力分析系統可精準測量軸向載荷分布。按ISO 16047標準要求,需對螺紋配合精度、表面硬度(洛氏硬度HRC檢測)及防松性能(振動臺模擬測試)進行綜合評估。
2. 鉚接質量無損檢測
運用X射線探傷技術檢測鉚釘內部空隙率,結合數字圖像相關法(DIC)分析鉚接變形量。航空航天領域需滿足NASM 1312-7標準,對鉚釘墩頭高度、直徑公差(±0.1mm)及剪切強度(≥345MPa)進行嚴格把關。
3. 焊接接頭完整性檢測
通過相控陣超聲檢測(PAUT)掃描焊縫熔深,磁粉探傷檢測表面裂紋。根據AWS D1.1規范,需進行宏觀金相檢驗(放大100倍觀測晶粒度)和顯微硬度測試(HV0.5標尺),重點關注熱影響區硬度梯度變化。
4. 銷軸類連接動態監測
采用三坐標測量儀檢測銷軸圓柱度(≤0.005mm),配合應變片測量接觸應力分布。針對重載設備,需進行50萬次疲勞測試(參照ISO 12107),同步監測磨損量變化曲線,確保極限工況下的連接可靠性。
5. 智能化檢測技術革新
基于機器視覺的自動定位系統可識別0.02mm級裝配偏差,物聯網傳感器實時監測連接部位溫升(精度±1℃)與振動頻譜。最新EN 15085-2標準已強制要求關鍵連接點部署在線監測裝置,實現預測性維護。
檢測標準體系與實施要點
現代機械連接檢測需構建多層級標準體系:基礎層執行GB/T 3098系列緊固件標準,進階層參照ASME PCC-1螺栓連接指南,特殊行業需滿足API 6A井口裝置等專項規范。檢測過程中應特別注意環境補償(溫度補償系數0.003%/℃)、設備校準周期(扭矩扳手每500次標定)及數據溯源性管理。
隨著數字孿生技術的應用,機械連接檢測正朝著虛擬驗證與實體檢測深度融合的方向發展。建議企業建立包含12項核心指標的檢測數據庫,通過大數據分析優化工藝參數,將連接失效風險降低至0.3%以下,切實保障裝備制造質量安全。

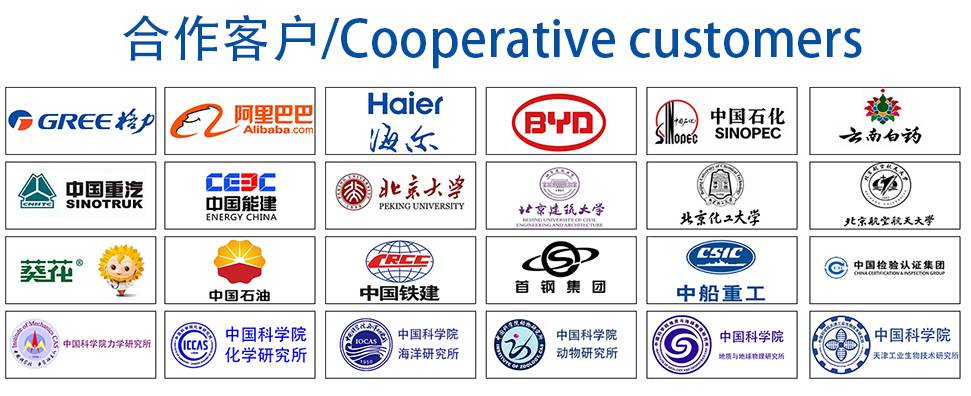