工業閥門殼體試驗檢測
概述
工業閥門是管道系統中關鍵的機械裝置,用于控制液體、氣體、漿料或其他流體的流動。閥門殼體的質量直接影響到整體設備的安全性和功能性。因此,進行閥門殼體的試驗檢測是確保其安全可靠運行的重要步驟。這些檢測包括材料、設計和制造工藝等方面,使閥門在使用過程中能夠承受預計的壓力、溫度和流量。
閥門殼體的材料選擇與制備
閥門殼體的材料選擇尤為重要,因為材料的特性直接決定了閥門的耐用性和適用性。目前常用的材料有鑄鐵、碳鋼、不銹鋼、合金和塑料等。根據具體應用條件,如高壓或腐蝕性環境,選用不同的材料。例如,不銹鋼通常用于抗腐蝕場合,而鑄鐵和碳鋼則常用于普通的工藝流程中。
一旦確定了材料,接下來就是殼體的制備。通常采用鑄造、鍛造或焊接工藝來制造殼體。每種工藝都有其特定的優點和限制,鑄造可以制造復雜形狀,鍛造則更適合于承受高應力的部位,而焊接則靈活性高,適用于組裝復雜結構的焊接件。制備過程中的嚴格工藝控制和質量檢測能夠確保閥門殼體的可靠性。
試驗檢測的方法和標準
閥門殼體的檢測涉及多種試驗,主要包括無損檢測、壓力試驗和耐久性試驗等。無損檢測主要檢查殼體的材料缺陷,如裂紋、氣孔和夾雜物,常用的方法有射線檢測、超聲波檢測、磁粉檢測等。通過這些檢測,可以在不破壞工件的情況下識別潛在的缺陷。
壓力試驗則是通過施加壓力,以檢驗殼體的耐壓性能。常見的壓力測試包括水壓試驗和氣壓試驗。在這些試驗中,閥門殼體會承受比實際工作壓力高出1.5倍的壓力,以驗證其密封性能和結構強度。
標準方面,閥門殼體的檢測需要遵循國際和國家相關標準,如美國機械工程師學會(ASME)標準、國際標準化組織(ISO)標準以及中國國家標準(GB)等。這些標準對材料的選擇、制造過程以及測試過程都有具體規定,確保每一個環節都達到了安全標準。
齊全的檢測技術
隨著科技的發展,閥門殼體的檢測技術也在不斷進步。如今,計算機斷層掃描(CT)技術、三維成像技術和人工智能系統開始被應用于檢測領域。這些新技術能夠在更短的時間內提供更精確的檢測結果。
CT技術通過X射線掃描提供閥門殼體的三維內部結構圖像,方便工程師精確探查隱藏的缺陷。三維成像技術則用于比對實際工件與設計形狀的差異,確保產品符合設計標準。人工智能系統可以利用大數據和機器學習算法分析檢測數據,預測潛在的質量問題,提高檢測的準確性和效率。
實際應用中的挑戰與解決方案
盡管檢測技術不斷進步,閥門殼體在實際應用中仍面臨多種挑戰。復雜的工業環境可能加快材料的退化,甚至導致意外故障。此外,不同國家和地區的標準差異也可能對閥門的質量保證構成挑戰。
為應對這些問題,企業需建立全面的質量控制系統,從設計、生產到最后的成品檢測都要進行嚴格監控。此外,定期的檢修和維護能夠延長閥門設備的使用壽命。對于跨境貿易,企業應熟悉進口國的相關標準和法規,并進行必要的認證,以確保產品的合規性。
結論
工業閥門殼體的試驗檢測是保障其性能和安全性的關鍵環節。隨著行業的發展和新技術的引入,試驗檢測的方法愈加多樣和精密,但無論技術如何進步,確保高質量的材料選擇、制造工藝和嚴格的檢測標準是保證閥門可靠性的基礎。通過持續改進檢測技術和質量管理措施,企業能更好地滿足市場需求,確保其產品能夠在各種環境下穩定、安全地運行。

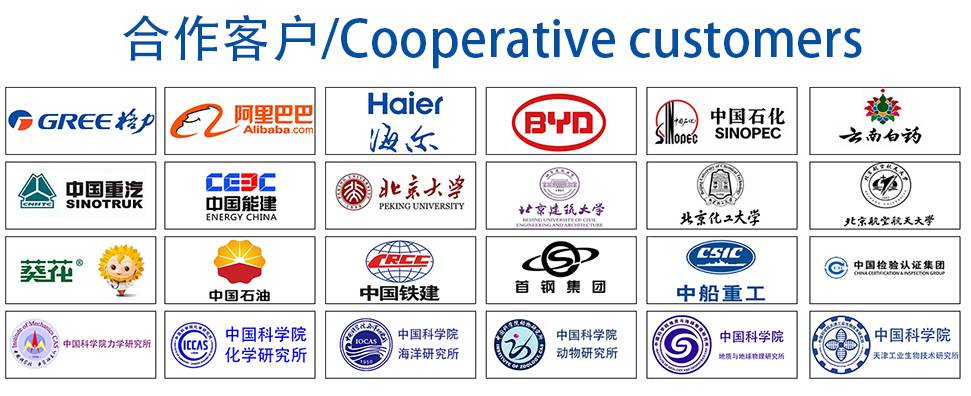