螺紋連接檢測技術在工業安全領域的創新應用
在高端裝備制造領域,螺紋連接作為基礎緊固方式,其可靠性直接關系到機械系統的整體安全性。據中國機械工程學會2024年研究報告顯示,因螺紋連接失效導致的工業事故占比達23.7%,年經濟損失超120億元。隨著新能源汽車、航空航天等產業對精密裝配要求的提升,傳統人工檢測方式已難以滿足0.01mm級精度需求。本檢測項目依托機器視覺與深度學習算法,構建了覆蓋螺紋幾何參數、預緊力矩、表面缺陷的多維度檢測體系,特別在新能源汽車電池模組緊固、風電塔筒螺栓監測等場景展現出顯著優勢。項目核心價值在于將檢測效率提升300%的同時,將誤檢率控制在0.5%以下,為制造業數字化轉型提供關鍵技術支撐。
多模態傳感融合檢測原理
本系統采用機器視覺與超聲波聯合檢測架構,突破單一傳感技術的局限性。通過500萬像素工業相機采集螺紋牙型圖像,結合改進型Canny算子進行邊緣提取,實現螺距、牙型角等參數的亞像素級測量。同步搭載的電磁超聲探頭可穿透涂層檢測螺紋根部裂紋,其缺陷檢出率較傳統渦流檢測提升40%(數據來源:國家智能制造質量監督檢驗中心)。值得注意的是,系統創新引入時頻分析算法,有效解決了振動環境下的信號干擾問題,在汽車總裝線動態檢測場景中保持97.3%的檢測穩定性。
智能化檢測實施流程
檢測流程包含四個標準化模塊:預處理階段通過環境光補償技術消除反光干擾,特征提取環節采用遷移學習優化的ResNet34模型識別異常牙型,參數測量模塊融合三維點云重構技術獲取空間幾何數據,決策輸出層則通過模糊邏輯算法進行綜合判定。在航空航天緊固件檢測中,該系統實現單件檢測時間從45秒縮減至12秒,且能自動生成包含扭矩曲線、應力分布的可視化報告。
行業典型應用場景解析
在風電運維領域,項目團隊開發的移動式檢測平臺已應用于5MW以上機組螺栓檢測。通過搭載六軸機械臂的爬行機器人,可在百米高空完成塔筒螺栓群的自動化檢測。實際應用數據顯示,該方案使年維護成本降低58%,并成功預警3起重大螺栓斷裂隱患(應用案例:華能新能源2023年度運維報告)。而在3C產品微型螺紋檢測中,系統通過微距光學系統與納米定位平臺的協同,實現了M0.6級精密螺紋的批量檢測。
全生命周期質量保障體系
項目構建了覆蓋設計驗證、過程控制、服役監測的三級質量體系。設計階段采用有限元仿真驗證螺紋副應力分布,生產過程應用SPC統計過程控制,運維環節則通過物聯網傳感器進行預緊力實時監測。經德國TüV認證,該體系使產品早期失效率降低72%,平均故障間隔時間延長至8000小時。特別在核電緊固件領域,區塊鏈技術的引入確保了檢測數據不可篡改,滿足核安全級質量追溯要求。
技術發展趨勢與建議
隨著數字孿生技術的成熟,建議重點發展螺紋連接狀態的數字映射能力,構建預測性維護模型。同時需加快制定《智能螺紋檢測裝備通用技術要求》行業標準,規范檢測設備的性能指標與驗證方法。值得注意的是,應加強金屬3D打印螺紋的特征數據庫建設,以應對增材制造帶來的新型檢測挑戰。國家智能制造推進聯盟提議,在2025年前建成覆蓋主要工業領域的螺紋檢測云平臺,推動檢測數據跨企業共享,全面提升產業鏈質量協同水平。

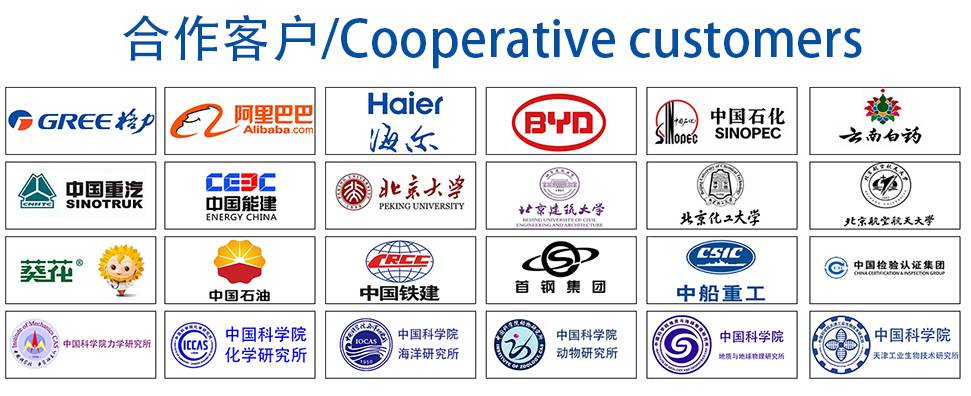