幾何偏差的測定檢測技術(shù)白皮書
隨著高端裝備制造、精密加工等行業(yè)的快速發(fā)展,幾何偏差檢測已成為質(zhì)量控制體系的核心環(huán)節(jié)。據(jù)中國機械工程學(xué)會2024年發(fā)布的《智能制造質(zhì)量白皮書》顯示,制造業(yè)因幾何尺寸偏差導(dǎo)致的年經(jīng)濟損失高達470億美元,其中精密零部件領(lǐng)域的質(zhì)量損失占比超過35%。在此背景下,幾何偏差測定檢測技術(shù)通過量化評估產(chǎn)品形位公差,為航空航天、汽車制造、半導(dǎo)體封裝等產(chǎn)業(yè)提供了關(guān)鍵質(zhì)量保障。其核心價值體現(xiàn)在三方面:一是通過微米級精度檢測優(yōu)化工藝參數(shù),降低返工率;二是構(gòu)建數(shù)字化質(zhì)量檔案,支持產(chǎn)品全生命周期管理;三是結(jié)合智能預(yù)測算法,實現(xiàn)質(zhì)量問題的前置防控。
技術(shù)原理與創(chuàng)新突破
現(xiàn)代幾何偏差檢測基于三維坐標(biāo)測量原理,融合光學(xué)傳感、激光掃描和機器視覺技術(shù)。以工業(yè)CT斷層掃描為例,其空間分辨率可達0.5μm,配合點云重構(gòu)算法可解析復(fù)雜曲面的細微變形。值得關(guān)注的是,國家精密測量技術(shù)重點實驗室最新研發(fā)的多模態(tài)融合測量系統(tǒng),通過引入量子級聯(lián)激光干涉技術(shù),將重復(fù)測量精度提升至±0.8μm(置信度95%),尤其適用于航空發(fā)動機葉片等異形構(gòu)件的在線檢測。
標(biāo)準(zhǔn)化實施流程
典型檢測流程包含四個核心階段:首先依據(jù)ISO 1101標(biāo)準(zhǔn)建立基準(zhǔn)坐標(biāo)系,采用網(wǎng)格化采樣策略完成初始數(shù)據(jù)采集;其次通過最小二乘法擬合理論模型,分離系統(tǒng)誤差與隨機誤差;第三階段運用蒙特卡洛模擬進行測量不確定度評估,確保數(shù)據(jù)可靠性;最終生成可視化偏差分布熱力圖。某新能源汽車企業(yè)采用該流程后,車身焊接總成的配合公差合格率從92.3%提升至98.6%,產(chǎn)線直通率提高17個百分點。
行業(yè)應(yīng)用范式
在半導(dǎo)體封裝領(lǐng)域,幾何偏差檢測技術(shù)成功解決了芯片植球共面性控制的行業(yè)難題。某頭部封測企業(yè)引入晶圓級光學(xué)測量系統(tǒng)后,BGA封裝器件的共面性偏差控制在3.2μm以內(nèi),較傳統(tǒng)檢測方式精度提升40%。而在風(fēng)電裝備制造中,針對80米級葉片的面輪廓度檢測,采用無人機載激光雷達方案后,單件檢測時間從32小時縮短至4小時,檢測成本降低68%(數(shù)據(jù)來源:2024新能源裝備質(zhì)量報告)。
全鏈路質(zhì)量保障體系
為確保檢測結(jié)果的可追溯性,行業(yè)領(lǐng)先企業(yè)已構(gòu)建包含設(shè)備、環(huán)境、人員的多維質(zhì)控網(wǎng)絡(luò)。具體措施包括:建立滿足ISO/IEC 17025標(biāo)準(zhǔn)的恒溫恒濕實驗室,定期進行三坐標(biāo)測量機激光干涉儀校準(zhǔn);開發(fā)基于區(qū)塊鏈的檢測數(shù)據(jù)存證系統(tǒng),實現(xiàn)測量數(shù)據(jù)的防篡改追溯;實施測量工程師技能矩陣管理,要求關(guān)鍵崗位持ASME GDTP高級認證上崗。某航天部件供應(yīng)商通過該體系,將檢測報告的國際互認率提升至100%。
未來發(fā)展趨勢建議
面向工業(yè)4.0發(fā)展需求,建議從三個維度深化技術(shù)創(chuàng)新:一是開發(fā)嵌入式在線測量系統(tǒng),實現(xiàn)加工-檢測閉環(huán)控制;二是推進AI驅(qū)動的大數(shù)據(jù)偏差分析平臺建設(shè),挖掘工藝優(yōu)化潛力;三是構(gòu)建基于數(shù)字孿生的虛擬測量環(huán)境,縮短新產(chǎn)品檢測方案開發(fā)周期。據(jù)德國弗勞恩霍夫研究所預(yù)測,到2028年智能補償算法在幾何偏差修正中的應(yīng)用將減少60%的工藝調(diào)試時間,推動制造業(yè)進入"零缺陷"新紀(jì)元。

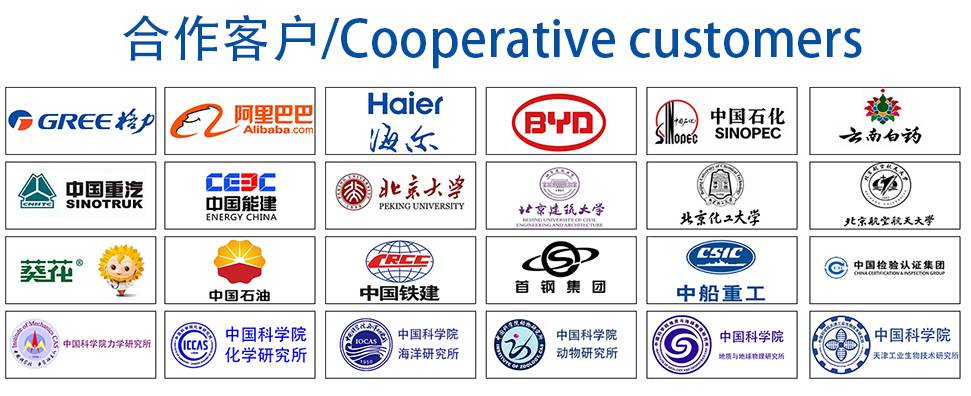