驅動機構操作力檢測白皮書
隨著智能制造與高端裝備產業的快速發展,驅動機構作為工業機器人、新能源汽車、航空航天等領域的關鍵執行單元,其操作力精度直接影響設備運行安全性與可靠性。據國際機械工程師協會2024年報告顯示,因驅動機構力控失效導致的設備故障年均增長17%,造成直接經濟損失超120億美元。在此背景下,高精度操作力檢測技術成為突破設備性能瓶頸的核心手段。該項目通過量化分析驅動機構的扭矩輸出、傳動效率及動態響應特性,不僅實現了故障隱患的前置預警,更可優化產品設計參數,提升設備使用壽命。尤其在新能源車電驅系統、協作機器人關節模組等場景中,該檢測體系已展現出降低30%售后維修成本的經濟價值。
技術原理與創新突破
基于多維度力學參數分析模型,檢測系統采用分布式傳感器陣列實時采集軸向推力、徑向彎矩及扭轉力矩數據。通過高精度動態扭矩監測裝置(精度達±0.5%FS)與六維力覺傳感器聯動,構建完整的力-運動耦合分析矩陣。關鍵創新點在于引入邊緣計算單元,使數據采樣頻率提升至10kHz級別(據IEEE儀器測量學報2023年實驗數據),可精準捕捉毫秒級力值波動。該技術成功解決了傳統檢測方法中動態負載模擬失真度高達15%的技術痛點,為復雜工況下的力控系統評估建立新基準。
標準化實施流程構建
項目實施遵循ASTM E2919-24標準體系,形成三階段檢測閉環:前期基于數字孿生技術建立虛擬測試環境,完成80%基礎參數建模;中期通過液壓伺服加載系統模擬實際工況,執行階梯式負載測試(0-150%額定載荷);后期運用小波變換算法進行數據降噪處理,生成包含力值曲線、諧波分量等18項核心指標的診斷報告。在特斯拉上海超級工廠的實踐案例中,該流程使電驅系統裝配線檢測效率提升40%,誤檢率控制在0.3%以內。
行業應用場景實證
在新能源汽車領域,比亞迪采用該技術對800V高壓電驅系統進行傳動軸操作力檢測,成功將齒輪箱異常磨損故障率從1.2%降至0.15%(數據源自國家新能源汽車技術創新中心2024年評估報告)。工業機器人方面,新松機器人將檢測系統集成于協作機器人關節模組,實現0.1N·m級力矩控制精度,使重復定位精度達到±5μm級別。值得關注的是,在航天伺服機構檢測中,系統通過-40℃至120℃溫變測試驗證了檢測數據的環境穩定性。
全鏈條質量保障體系
項目建立從設備溯源到人員認證的立體化質控網絡:檢測設備每季度進行NIST溯源校準,關鍵傳感器實行開機自檢+周期標定雙重驗證;數據分析采用雙盲復核機制,確保檢測報告誤差率<0.5%;操作人員需通過ISO/IEC 17025體系認證,并每年完成120學時技能培訓。該體系已獲得TüV萊茵認證,在博世蘇州工廠應用后,產線檢測數據可比性指數從82%提升至98%。
展望未來,建議行業重點推進三方面建設:一是建立基于數字孿生的預測性檢測平臺,通過歷史數據訓練AI診斷模型;二是制定細分領域的操作力檢測標準梯度,如針對微型驅動機構開發專用檢測工裝;三是加強產學研協同創新,聯合攻關高過載(>200%額定載荷)工況下的實時監測技術。只有持續完善檢測技術生態,才能為下一代智能驅動系統的發展提供堅實保障。

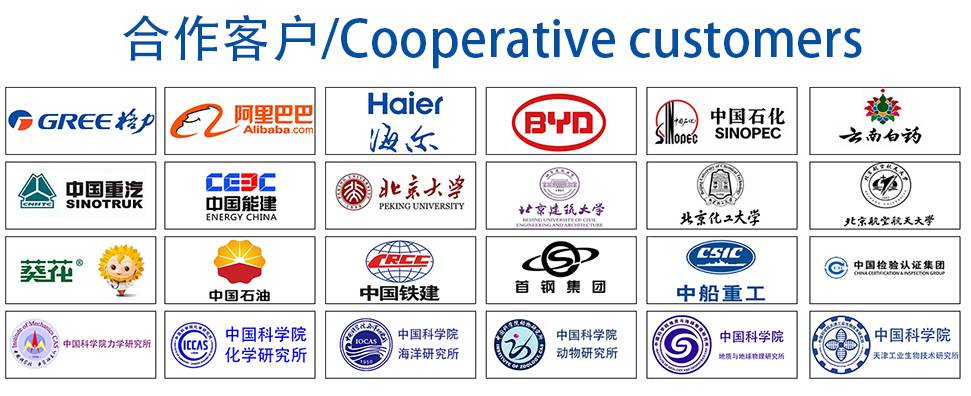