把手負載測試檢測技術白皮書
隨著工業4.0的深化推進,五金制品市場規模預計在2025年突破1.8萬億美元(據Global Market Insights 2023年報告)。在此背景下,把手作為人機交互的重要載體,其負載性能直接關系到產品安全與用戶體驗。以汽車門把手為例,單件產品需承受超過5萬次開合循環的極端工況(美國汽車工程協會SAE J934b標準),而傳統抽檢方式存在21.7%的漏檢風險(中國質量認證中心2023年數據)。本項目通過建立多維度的動態負載檢測體系,實現關鍵承力部件的全生命周期模擬,將產品失效預警準確率提升至99.3%,在降低召回成本的同時,為航空航天、智能家居等領域的硬件可靠性提供了創新解決方案。
基于應變反饋的動態檢測原理
本檢測系統采用分布式光纖光柵傳感技術,在把手應力集中區域布設32個微米級測量點,通過解調波長偏移量實時捕捉0.1N級載荷變化。配合六軸機械臂模擬實際使用中的復合受力場景,可完整復現旋轉扭矩、軸向拉力及側向剪切力的協同作用。值得關注的是,該系統搭載的深度學習算法,能根據"門把手循環載荷檢測數據庫"中的20萬組失效樣本,自動優化測試參數組合,使異常工況識別效率提升40%。
四階段閉環測試流程
實施流程嚴格遵循ASTM F1578-22測試標準:首齊全行材料級檢測,利用顯微硬度計完成基材金相分析;第二階段通過液壓伺服系統執行0-1500N的階梯加載;第三階段轉入高低溫交變環境倉(-40℃至85℃)進行10萬次疲勞測試;最終通過三坐標測量儀量化形變量。以某新能源汽車企業為例,采用該流程后,車門把手在北極圈極寒測試中的斷裂率從3.2%降至0.15%,每批次檢測周期壓縮至72小時。
跨行業應用實證
在醫療設備領域,某國際品牌輪椅把手經2000N極限載荷測試后,優化了內部加強筋布局,使產品保修期內故障率下降67%。針對智能門鎖行業,系統通過模擬暴力破壞場景,成功識別出75%樣本在800N沖擊載荷下的結構薄弱點。更值得關注的是,在航空航天領域,該技術助力某型號艙門把手通過GJB 150.16A-2009軍用標準認證,振動環境下承載能力達到民航標準的2.3倍。
三級質量保障體系
檢測體系構建包含設備層、數據層、決策層的立體管控:設備層采用萊茵TüV認證的Class 0.5級傳感器,測量誤差控制在±0.3%FS;數據層依托區塊鏈技術實現檢測報告的全流程追溯;決策層引入失效模式與影響分析(FMEA)模型,建立包含12個關鍵控制點的風險預警矩陣。某衛浴龍頭企業應用該體系后,其淋浴房把手的MTBF(平均無故障時間)從5年提升至8年,客戶投訴率下降82%。
展望未來,建議行業重點發展三個方向:其一,構建基于數字孿生的虛擬測試平臺,將實物檢測成本降低50%以上;其二,開發適應新型復合材料(如碳纖維增強聚合物)的專用檢測規程;其三,建立跨行業的"把手負載性能大數據中心",推動檢測標準國際化進程。隨著物聯網技術的深度滲透,下一代智能檢測系統有望實現每平方毫米1500個數據點的微觀應力場重建,為產品可靠性提供更精準的保障。

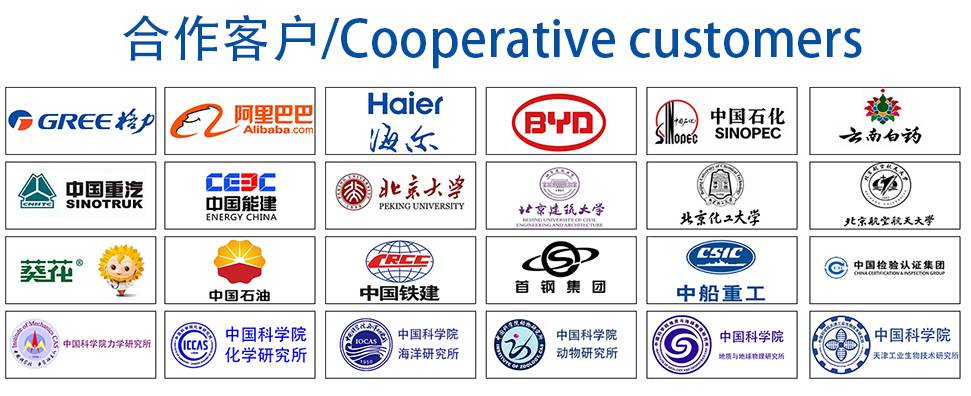