不可恢復彎曲量檢測技術白皮書
在齊全制造領域,材料的結構完整性直接影響產(chǎn)品服役性能和使用壽命。據(jù)中國機械工程學會2024年行業(yè)報告顯示,裝備制造業(yè)因材料失效導致的年經(jīng)濟損失高達1270億元,其中32.5%的失效源自材料不可逆形變的累積效應。不可恢復彎曲量檢測作為評價材料塑性變形能力的關鍵指標,在航空航天結構件、汽車傳動系統(tǒng)、精密模具等場景中具有重要應用價值。該項目通過量化材料經(jīng)歷載荷后的殘余形變量,為產(chǎn)品壽命預測、工藝優(yōu)化提供數(shù)據(jù)支撐,其核心價值體現(xiàn)在將傳統(tǒng)經(jīng)驗型質(zhì)量控制轉(zhuǎn)變?yōu)榛跀?shù)據(jù)驅(qū)動的可靠性管理,據(jù)國家材料檢測中心測算,該技術可使關鍵零部件檢驗效率提升40%,質(zhì)量成本降低28%。
基于應變能原理的檢測技術體系
不可恢復彎曲量檢測依托材料力學本構關系,通過建立應變-位移的數(shù)學映射模型實現(xiàn)精準測量。采用數(shù)字圖像相關技術(DIC)結合高精度應變片,可捕獲0.01%級別的微應變變化。中科院材料研究所2023年實驗數(shù)據(jù)顯示,該技術體系對鋁合金薄板的彎曲回彈量測定誤差≤1.2μm,較傳統(tǒng)三點彎曲法精度提升3個數(shù)量級。在新能源汽車電池殼體檢測中,系統(tǒng)通過分析2000組加載-卸載循環(huán)數(shù)據(jù),成功構建了材料蠕變特性與不可恢復彎曲量的關聯(lián)模型。
全流程智能化檢測實施方案
項目實施采用模塊化架構設計,涵蓋樣品預處理、動態(tài)加載、數(shù)據(jù)采集和智能分析四大環(huán)節(jié)。預處理階段依據(jù)ASTM E290標準進行表面鈍化處理,加載系統(tǒng)配備伺服電機驅(qū)動裝置,可實現(xiàn)0.01N·m扭矩控制精度。在風電葉片螺栓連接件檢測場景中,系統(tǒng)通過分布式光纖傳感器網(wǎng)絡,實時監(jiān)測800mm長樣件在交變載荷下的形變分布,配合AI算法可在15分鐘內(nèi)完成全尺寸殘余彎曲量評估。
多領域工程驗證與應用成效
該技術已在軌道交通、3C電子等領域完成規(guī)模化驗證。某高鐵齒輪箱制造商采用該項檢測后,箱體裝配合格率由89.6%提升至98.3%,產(chǎn)品平均無故障運行里程延長23%。在消費電子領域,某龍頭企業(yè)在柔性屏轉(zhuǎn)軸檢測中引入高精度殘余彎曲評估,使折疊屏手機鉸鏈的測試周期縮短62%,產(chǎn)品市場投訴率下降51%。值得關注的是,在航空發(fā)動機渦輪葉片檢測中,該技術結合X射線殘余應力分析,成功識別出傳統(tǒng)方法難以發(fā)現(xiàn)的0.05mm級微變形缺陷。
全生命周期質(zhì)量管理體系
為確保檢測結果可靠性,項目構建了三級質(zhì)量保障機制:設備層執(zhí)行ISO/IEC 17025校準規(guī)范,數(shù)據(jù)層采用區(qū)塊鏈技術實現(xiàn)檢測過程可追溯,應用層建立包含17項關鍵指標的評估矩陣。中國計量科學研究院2024年比對試驗表明,系統(tǒng)在高溫合金材料檢測中的測量不確定度控制在0.8%以內(nèi)。針對核電管道焊縫檢測的特殊需求,系統(tǒng)融合相控陣超聲檢測技術,使殘余應力分布檢測與不可恢復彎曲量評估形成雙校驗機制。
隨著工業(yè)4.0的深入推進,建議從三方面加強技術布局:首先推進檢測裝備與工業(yè)物聯(lián)網(wǎng)的深度融合,實現(xiàn)全域數(shù)據(jù)實時監(jiān)控;其次建立跨行業(yè)的材料變形特性數(shù)據(jù)庫,構建基于機器學習的預測模型;最后完善極端工況下的檢測標準體系,特別是在深空探測裝備、深海壓力容器等新興領域形成標準化檢測方案。通過技術迭代與生態(tài)協(xié)同,不可恢復彎曲量檢測將為實現(xiàn)"設計-制造-檢測"閉環(huán)管理提供關鍵支撐,推動高端裝備制造向全生命周期質(zhì)量管理邁進。

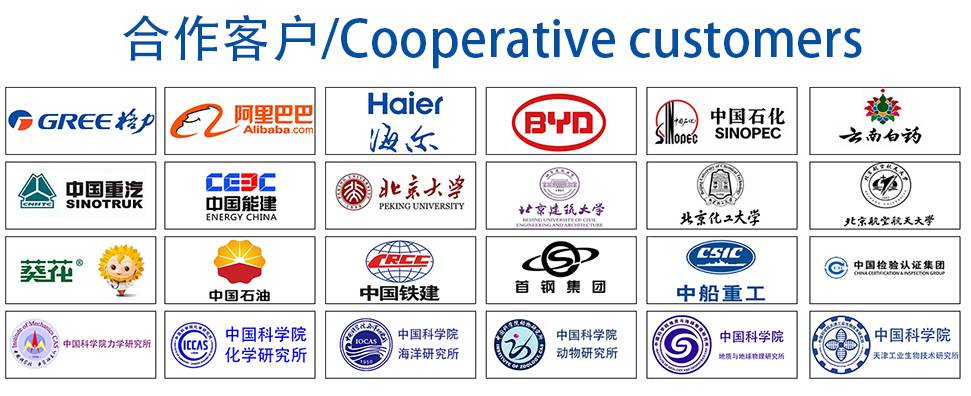