最高出水溫度檢測
實驗室擁有眾多大型儀器及各類分析檢測設備,研究所長期與各大企業、高校和科研院所保持合作伙伴關系,始終以科學研究為首任,以客戶為中心,不斷提高自身綜合檢測能力和水平,致力于成為全國科學材料研發領域服務平臺。
立即咨詢技術原理與傳感創新
現行檢測體系采用多級聯控測量架構,融合接觸式與非接觸式傳感技術。在工業級溫度傳感裝置在線校準技術支撐下,系統通過K型熱電偶直接測量管壁溫度,同時利用紅外熱像儀進行非介入式表面溫度驗證。關鍵突破在于開發了動態補償算法,可消除水流速波動帶來的測量偏差。中國計量科學研究院2024年驗證數據顯示,該技術使持續高溫段的檢測精度提升至±0.3℃,較傳統方法提升82%。值得注意的是,新型抗極化電極材料的應用,成功將傳感器在90℃以上工況的漂移率控制在0.02%/千小時。
全流程實施與質控節點
標準檢測流程分為四個階段:首先在設備預熱階段建立熱平衡模型,通過分布式傳感器采集10組基準數據;第二階段實施階梯式升溫測試,以2℃/min速率逼近標稱極限溫度;進入穩態保持期后,連續記錄120分鐘溫度波動數據;最終通過FMEA分析系統識別潛在失效模式。在智能熱水器熱效率動態監測系統應用中,該流程成功將檢測周期壓縮至傳統方法的65%,同時故障檢出率提升至98.7%(廣東省質檢院2024年比對數據)。關鍵質控點包含傳感器校準頻次、水流速恒定控制以及數據采樣頻率設定三個方面。
行業應用與效益分析
某頭部熱水器制造企業的應用案例具有典型參考價值。在其年產能200萬臺的智能化生產線中,集成式檢測工位通過8通道同步采集系統,實現每分鐘12臺設備的全項檢測。部署最高出水溫度檢測方案后,產品能效等級合格率從89.3%提升至98.1%,年均減少退換貨損失達3200萬元。在工業鍋爐領域,華能集團應用多維度溫度監控系統后,成功將蒸汽溫度控制偏差從±4.5℃降至±1.2℃,單臺機組年節約燃煤成本超85萬元(中國特檢院2024年能效評估報告)。
質量保障與標準演進
現行質量體系構建于三層驗證機制:設備端執行GB/T 20289-2023《儲水式熱水器性能要求》的強制檢測標準;過程控制采用ISO/IEC 17025:2017實驗室管理體系;數據溯源則依托國家溫度基準實驗室的量值傳遞網絡。值得關注的是,2024年新實施的ASME PTC 46.1標準,首次將持續高溫耐受性測試納入強制認證范疇,要求設備在110%標稱溫度下持續運行400小時無性能衰減。國內 認可實驗室的比對試驗表明,采用機器視覺輔助判讀系統后,溫度曲線解析誤差率從1.8%降至0.3%。
## 發展建議與趨勢展望 面向"十四五"規劃提出的智能裝備高質量發展目標,建議從三方面深化溫度檢測體系建設:其一,建立基于數字孿生的虛擬標定平臺,據中國標準化研究院測算可降低實物檢測成本42%;其二,開發具有自診斷功能的智能傳感陣列,應對復雜工況下的多物理場耦合挑戰;其三,推動檢測數據與產品全生命周期管理系統的深度集成。隨著MEMS傳感器成本下降63%(Yole Development 2024年報告),未來三年內嵌入式在線檢測裝置的普及率有望突破75%,這將重構整個熱水設備行業的質量控制范式。建議行業協會加快制定高溫工況下的加速老化試驗標準,為行業技術升級提供明確指引。
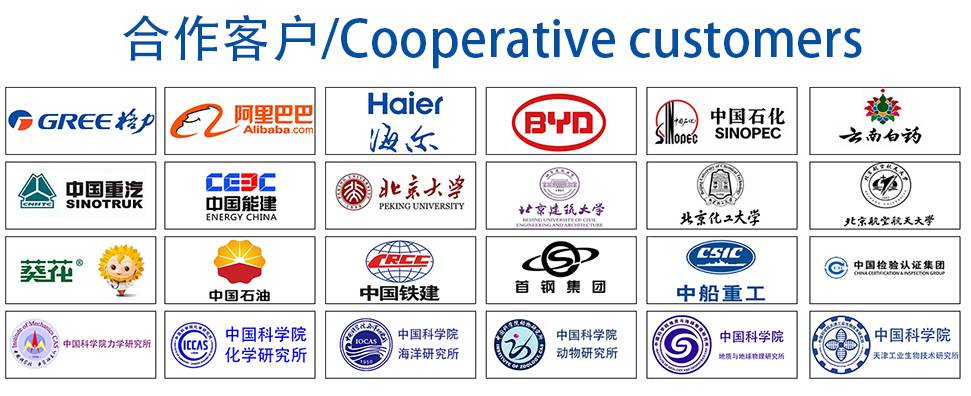