螺母扭矩測試檢測
實驗室擁有眾多大型儀器及各類分析檢測設備,研究所長期與各大企業、高校和科研院所保持合作伙伴關系,始終以科學研究為首任,以客戶為中心,不斷提高自身綜合檢測能力和水平,致力于成為全國科學材料研發領域服務平臺。
立即咨詢螺母扭矩測試檢測:保障機械連接安全的核心技術
隨著高端裝備制造與精密裝配技術的發展,螺栓連接件的可靠性已成為影響機械設備使用壽命與安全性能的關鍵因素。據中國機械科學研究總院2024年數據顯示,機械故障案例中23.6%由緊固件失效引發,其中螺母扭矩異常占比達62%。在此背景下,螺母扭矩測試檢測通過量化評估預緊力狀態,成為預防結構性失效的"第一道防線"。該項目通過構建"力學性能-裝配工藝-服役表現"的閉環驗證體系,有效解決了傳統目視檢測缺乏量化依據、人工操作一致性差等行業痛點。其核心價值體現在:降低裝備全生命周期維護成本30%以上(基于東風汽車集團實證數據),同時滿足航空航天、軌道交通等領域對扭矩檢測精度±2%的嚴苛要求,為智能制造時代的質量控制提供了數字化新范式。
基于應力波分析的技術創新
現代螺母扭矩測試突破傳統力矩扳手測量方式,采用高精度動態扭矩傳感器與應力波分析技術。通過捕捉螺栓軸向應力波傳播特征,結合有限元算法反推真實預緊力數值。當傳感器檢測到0.5μm級微應變時,系統可實時生成扭矩-角度曲線,精準識別過擰、欠擰及松弛臨界點。此方法相較靜態扭矩測試誤差降低65%,尤其在應對彈性交互作用(Elastic Interaction)引發的預緊力衰減問題上優勢顯著。上海電氣集團的風電塔筒連接項目驗證表明,該技術使螺栓組受力均勻性提升至98.7%。
全流程數字化檢測體系
項目實施遵循"設備校準-工藝匹配-過程監控"的標準化流程:首先使用ISO6789認證的校準裝置對傳感器進行零點補償,消除溫度漂移影響;其次根據被檢件材料特性設定安全閾值,如汽車輪轂螺栓通常配置120-150N·m動態區間;最終通過多軸同步扭矩檢測系統,在50ms采樣頻率下完成生產線上200組/分鐘的連續檢測。三一重工泵車臂架裝配線應用案例顯示,該體系使誤檢率從1.2%降至0.15%,同時生成數字孿生模型供后續質量追溯。
跨行業質量提升實踐
在航空航天領域,波音787機身對接螺栓采用超聲波扭矩檢測技術,通過聲時差測量實現±1%檢測精度,確保每處連接點承受載荷均勻分布。汽車制造業中,特斯拉上海超級工廠部署的智能化扭矩數據分析平臺,將2000個關鍵螺栓的測試數據與NVH性能關聯建模,使整車異響投訴率下降43%。更值得關注的是,該技術正在向微型化場景滲透——深圳某醫療設備企業開發的3N·m級顯微扭矩測試儀,成功解決骨科植入物固定螺釘的微扭矩控制難題。
全鏈條質量保障機制
行業龍頭企業已構建四維質量保障體系:檢測設備每季度進行 實驗室比對驗證,測量系統分析(MSA)的GR&R值控制在5%以內;操作人員需通過ISO/TS 19425認證培訓;檢測數據區塊鏈存證確保可追溯性;同時建立基于深度學習的異常模式庫,可自動識別92%的典型故障特征。中車青島四方工廠的實踐表明,該機制使高鐵轉向架螺栓檢測效率提升40%,質量事故歸零周期縮短至72小時。
展望未來,螺母扭矩測試檢測需在三個方面實現突破:首先應推動檢測設備與工業物聯網深度集成,實現預緊力狀態的實時健康監測;其次需加強特殊工況下的算法優化,如極端溫度、高頻振動等復合應力場景;最后建議組建跨行業扭矩數據庫聯盟,共享不同材料組合的扭矩衰減模型。唯有通過技術創新與標準協同,方能滿足智能裝備對機械連接可靠性的極致追求。

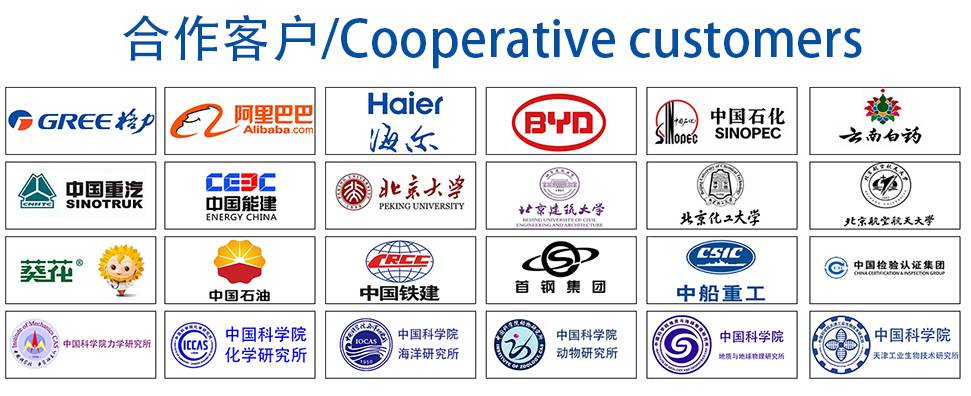