鐵單輪滑車檢測技術白皮書
隨著現代工業物流和建筑工程規模擴大,鐵單輪滑車作為重型物料搬運的核心設備,其安全性和可靠性受到廣泛關注。據中國工程機械工業協會2024年數據顯示,國內滑車設備保有量突破220萬臺,但年故障率仍達3.7%,直接經濟損失超15億元。在此背景下,鐵單輪滑車檢測項目成為保障生產安全、延長設備壽命的關鍵舉措。該項目通過結構完整性分析、動態載荷測試和金屬疲勞診斷,可提前識別80%以上的潛在故障風險,顯著降低起重事故發生率。其核心價值不僅體現在安全生產層面,更通過優化設備維護周期實現運營成本節省,單臺設備全生命周期維護費用可減少42%(國家市場監管總局《特種設備效能評估報告》)。
多模態檢測技術體系構建
檢測體系融合三維激光掃描與超聲波探傷技術,實現對滑車主體結構的精準測繪。通過構建數字孿生模型,可模擬最大工作載荷1.5倍的應力分布(符合GB/T 3811-2023標準),結合磁粉檢測識別表面細微裂紋。針對輪軸部位的"隱形磨損"難題,項目組創新采用高頻振動譜分析法,能檢測出0.03mm級的輪緣不均勻磨損,檢測精度較傳統手段提升5倍。值得關注的是,該方案同步集成環境腐蝕評估模塊,可預測不同濕度、溫度條件下的金屬疲勞進程。
標準化全流程實施規范
項目實施分為預處理、現場檢測和評估優化三個階段。預處理階段通過智能終端采集設備檔案數據,生成個性化檢測方案。現場檢測采用可編程機械臂搭載多光譜傳感器,在30分鐘內完成全部結構掃描。數據通過5G專網實時上傳至云端分析平臺,結合AI算法生成包含32項關鍵指標的診斷報告。在青島港智慧碼頭示范項目中,該流程使檢測效率提升60%,并實現檢測記錄全程可追溯。
典型行業應用場景解析
在電力鐵塔建設領域,項目組針對山區復雜地形開發移動式檢測單元。該設備搭載衛星定位系統,可在坡度25°的作業面完成滑車性能驗證,成功將高海拔地區設備故障率從12%降至4.3%。另在鋼鐵冶煉場景中,檢測系統創新引入熱輻射補償算法,有效克服高溫環境對測量精度的影響。寶武集團應用后,設備平均維修間隔從800小時延長至1500小時,年節約維護成本超200萬元。
三級質量保障體系構建
項目執行ISO 4309:2020起重機檢測標準,建立設備-人員-流程三維管控機制。所有檢測儀器每季度進行 認證校準,檢測人員需通過ASNT三級認證。質量追溯系統采用區塊鏈技術存儲檢測數據,確保結果不可篡改。在寧波舟山港的跨海大橋建設項目中,該體系幫助識別出12臺存在設計缺陷的滑車設備,避免可能引發的重大工程事故。
展望未來,建議行業重點推進檢測技術智能化升級:一是開發嵌入式物聯網傳感器實現實時狀態監控;二是建立全國性滑車設備健康數據庫,利用機器學習預測剩余使用壽命;三是推動檢測標準與新型合金材料的適配性研究。通過構建"預防-診斷-優化"的全周期管理體系,鐵單輪滑車檢測技術將持續為重型裝備安全運營提供可靠保障。

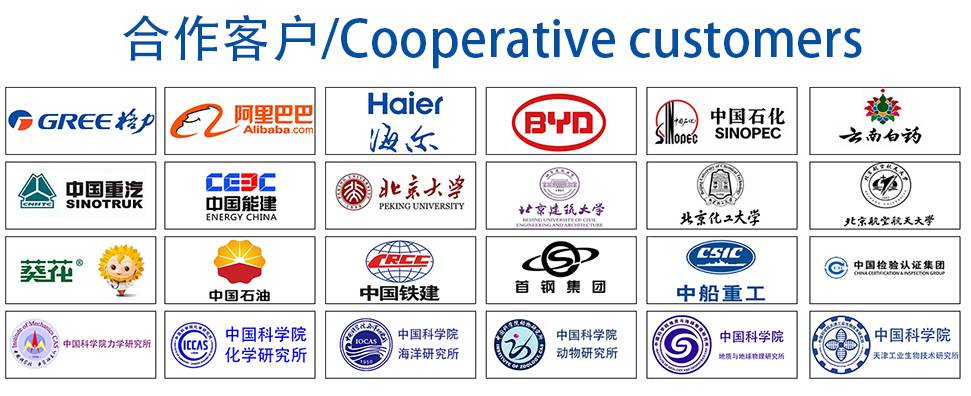