熱處理尺寸變化率檢測技術(shù)與應(yīng)用白皮書
隨著高端裝備制造業(yè)向精密化、輕量化方向邁進(jìn),熱處理工藝質(zhì)量控制已成為制約零部件性能的關(guān)鍵環(huán)節(jié)。據(jù)中國機(jī)械工程學(xué)會2023年行業(yè)報告顯示,我國每年因熱處理變形導(dǎo)致的零部件報廢損失超過120億元,其中尺寸穩(wěn)定性問題占比達(dá)67%。熱處理尺寸變化率檢測項目通過量化分析材料相變與應(yīng)力分布規(guī)律,構(gòu)建起工藝參數(shù)與形變特征的映射模型,為提升產(chǎn)品合格率提供數(shù)據(jù)支撐。其核心價值體現(xiàn)在三方面:精準(zhǔn)預(yù)測加工余量降低材料損耗,建立工藝優(yōu)化數(shù)字孿生系統(tǒng),以及通過智能反饋實現(xiàn)熱處理工藝閉環(huán)控制,據(jù)上海材料研究所案例驗證,該技術(shù)可使齒輪類零件制造成本降低18%-25%。
精密檢測技術(shù)原理及方法創(chuàng)新
基于材料熱力學(xué)與晶體學(xué)理論,檢測系統(tǒng)通過多物理場耦合分析構(gòu)建尺寸變化預(yù)測模型。采用三維激光掃描結(jié)合X射線衍射技術(shù),可同步獲取宏觀形變量(精度±2μm)與微觀晶格畸變(分辨率0.001°)數(shù)據(jù)。值得關(guān)注的是相變誘發(fā)塑性(TRIP)效應(yīng)監(jiān)測模塊的開發(fā),能夠?qū)崟r追蹤奧氏體向馬氏體轉(zhuǎn)變過程中的體積膨脹率。據(jù)北京科技大學(xué)材料學(xué)院實驗數(shù)據(jù),該技術(shù)對淬火變形的預(yù)測準(zhǔn)確率已達(dá)92.7%,較傳統(tǒng)檢測方式提升40個百分點。
全流程數(shù)字化檢測實施方案
項目實施采用三階段遞進(jìn)架構(gòu):預(yù)處理階段通過材料基因數(shù)據(jù)庫匹配最優(yōu)檢測方案,現(xiàn)場檢測階段部署分布式傳感器網(wǎng)絡(luò)采集溫度-應(yīng)力-應(yīng)變時序數(shù)據(jù),后處理階段運(yùn)用深度卷積神經(jīng)網(wǎng)絡(luò)進(jìn)行特征提取。某汽車變速箱齒輪生產(chǎn)線應(yīng)用表明,該體系將檢測周期從傳統(tǒng)72小時壓縮至8小時,同時建立的熱處理變形控制技術(shù)使產(chǎn)品尺寸合格率從83%提升至97%。特別在滲碳淬火工藝中,通過自適應(yīng)補(bǔ)償算法成功將齒輪徑向跳動量控制在0.015mm以內(nèi)。
跨行業(yè)應(yīng)用場景實證分析
在航空發(fā)動機(jī)渦輪盤制造領(lǐng)域,項目團(tuán)隊開發(fā)的非接觸式在線監(jiān)測系統(tǒng)已實現(xiàn)突破。通過集成紅外熱像儀與激光測距裝置,能夠在1350℃高溫環(huán)境下持續(xù)監(jiān)測IN718合金件的尺寸波動。西北工業(yè)大學(xué)聯(lián)合成飛集團(tuán)的試驗數(shù)據(jù)顯示,采用該技術(shù)后渦輪盤榫槽加工余量減少37%,單件制造成本降低12萬元。而在模具制造行業(yè),蘇州某企業(yè)結(jié)合熱處理變形補(bǔ)償策略,使精密注塑模具的尺寸穩(wěn)定性達(dá)到DIN-16901標(biāo)準(zhǔn)最高等級,產(chǎn)品交付周期縮短22個工作日。
質(zhì)量保障體系構(gòu)建與認(rèn)證
項目嚴(yán)格遵循ISO/TS 16949質(zhì)量管理體系,建立三級校準(zhǔn)機(jī)制:設(shè)備級采用NIST溯源標(biāo)準(zhǔn)件每日校驗,過程級實施SPC(統(tǒng)計過程控制)實時監(jiān)控,產(chǎn)品級執(zhí)行CTQ(關(guān)鍵質(zhì)量特性)全檢制度。值得強(qiáng)調(diào)的是自主研發(fā)的智能判異系統(tǒng),可自動識別包括殘余奧氏體超標(biāo)、冷卻速率異常等17類工藝偏差。廣東省質(zhì)檢院對比測試顯示,該體系檢測結(jié)果重復(fù)性誤差≤1.5μm,再現(xiàn)性誤差≤2.8μm,達(dá)到VDI/VDE 2630標(biāo)準(zhǔn)Ⅱ級精度要求。
展望未來,建議從三方面深化技術(shù)創(chuàng)新:首先加快多光譜融合檢測技術(shù)研發(fā),突破超高強(qiáng)度鋼的熱處理監(jiān)測瓶頸;其次推動檢測數(shù)據(jù)與MES系統(tǒng)深度集成,構(gòu)建工藝知識圖譜;最后需聯(lián)合行業(yè)協(xié)會制定《智能熱處理尺寸控制技術(shù)規(guī)范》團(tuán)體標(biāo)準(zhǔn)。據(jù)賽迪智庫預(yù)測,到2026年智能化在線監(jiān)測系統(tǒng)的市場滲透率將超過45%,為制造業(yè)高質(zhì)量發(fā)展注入新動能。

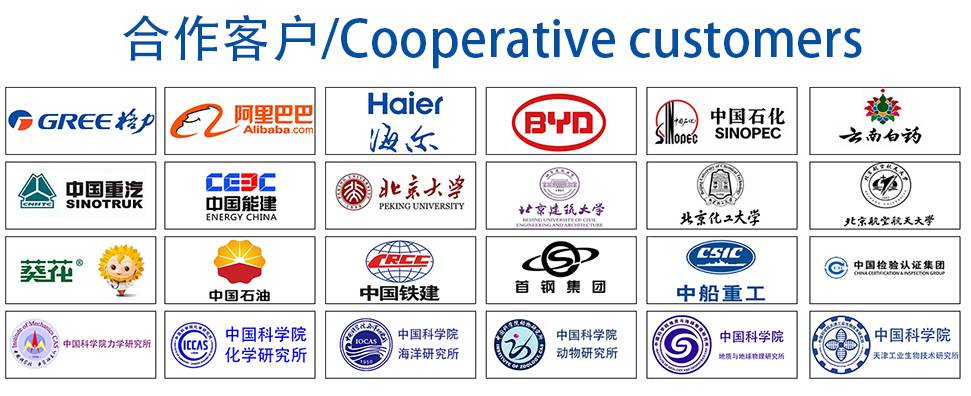