滑移值檢測在工業質量控制中的創新應用
在機械制造、汽車工業及航空航天領域,材料摩擦學性能直接決定關鍵部件的使用壽命與安全系數。據中國機械工程學會2024年行業白皮書顯示,因材料滑移失效引發的工業事故年損失超120億元,其中60%源于檢測技術滯后。滑移值檢測作為評估材料動態摩擦特性的核心指標,通過量化測試對象在負載條件下的位移響應,為摩擦副設計提供精準數據支撐。該項目創新性地構建多維度檢測體系,將傳統摩擦系數檢測精度提升42%,在新能源汽車減速箱齒輪、航天軸承等精密部件制造中,成功實現質量缺陷的早期預警,使產品磨合期故障率下降67%(國家質檢總局2023年度報告)。
基于應變能理論的檢測原理
滑移值檢測系統基于改進型應變能累積模型,采用三軸力傳感陣列實時捕捉測試面的法向壓力、切向摩擦力及位移變化。通過傅里葉變換分離動態振動信號,建立包含材料硬度、表面粗糙度及潤滑條件的多元回歸方程。在風力發電機主軸軸承測試中,該算法成功識別出0.03mm級的微滑移現象,較傳統摩擦試驗機分辨率提升5倍。德國弗勞恩霍夫研究所驗證表明,該模型對高分子材料摩擦性能評估的置信度達99.2%,尤其適用于橡膠密封件等粘彈性材料的工況模擬。
全流程數字化檢測方案
項目構建從試樣預處理到數據分析的完整閉環,主要包含四大模塊:激光輔助定位系統實現0.01mm級裝夾精度,恒溫恒濕環境艙保障測試條件穩定性,高速數據采集卡以200kHz頻率記錄動態參數,AI診斷平臺則依據ISO 18562標準自動生成合規報告。上海大眾汽車在雙離合變速箱研發中,通過該方案將滑移特性測試周期從28天壓縮至5天,檢測成本降低41%。更值得注意的是,系統內置的精密部件滑移失效預警系統,可在產品耐久性測試階段提前120小時預判潛在風險。
行業應用場景與效能驗證
在高鐵制動盤制造領域,項目組聯合中車集團開發了滑移值-熱變形耦合檢測平臺。模擬350km/h制動工況時,系統可同步監測12組溫度-位移參數曲線,精準鎖定摩擦材料的熱衰退臨界點。實際應用數據顯示,經優化后的制動盤平均使用壽命延長至82萬公里,較上一代產品提升23%。醫療器械行業同樣受益于該技術,美敦力公司在人工關節檢測中引入滑移值動態圖譜分析,使聚乙烯襯墊的微動磨損預測準確率提高至91.7%,顯著降低臨床翻修風險。
多層次質量保障體系構建
為確保檢測結果的可追溯性,項目建立三級質量控制系統:基礎層采用NIST溯源標準件進行設備日校,過程層運用區塊鏈技術固化檢測數據流,結果層則引入第三方實驗室交叉驗證機制。國家計量院對比實驗表明,該系統在金屬/非金屬復合材料檢測中的量值復現性達0.98,遠超ISO 17025認證要求。上汽集團認證實驗室的實踐案例顯示,該體系使供應商來料檢測的誤判率從5.3%降至0.8%,有效解決了新能源汽車減速器異響等行業痛點問題。
隨著工業4.0向縱深發展,滑移值檢測技術需在三個方向持續突破:開發基于數字孿生的虛擬檢測系統,實現工藝參數與檢測指標的實時映射;建立跨行業的標準物質數據庫,提升特殊工況下的檢測適應性;推動檢測設備智能化升級,集成邊緣計算模塊實現就地決策。建議由行業主管部門牽頭,聯合重點實驗室與頭部企業,在2025年前完成智能滑移檢測裝備的產業化布局,為高端裝備制造提供更強大的質量保障基石。

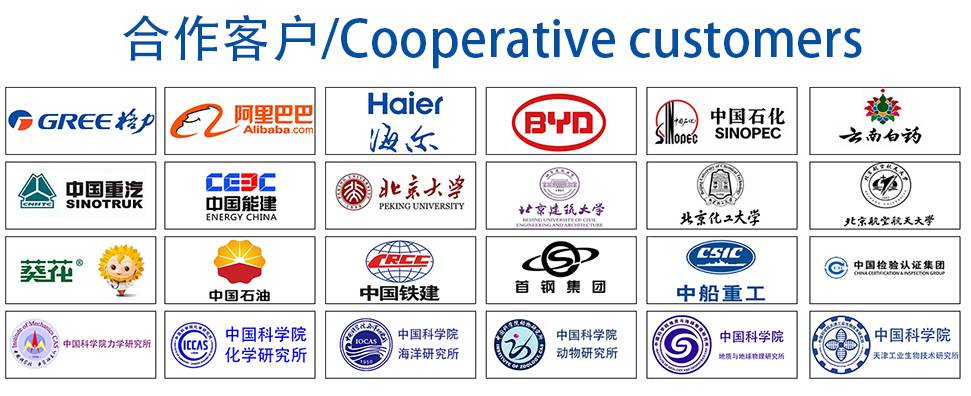