三氧化二鐵-原子吸收分光光度法(代用法)檢測技術研究與應用
在冶金、陶瓷制造及催化劑生產領域,三氧化二鐵(Fe2O3)的純度與含量直接影響材料性能與工藝穩定性。據中國材料科學研究院2024年數據顯示,工業級氧化鐵市場規模已突破320億美元,年復合增長率達6.8%,對檢測技術的精準度與效率提出更高要求。傳統化學滴定法雖具備理論基礎,但存在操作復雜、耗時長的缺陷,難以滿足現代工業快速檢測需求。原子吸收分光光度法(AAS)作為代用技術的核心價值在于:通過優化樣品前處理流程與儀器參數配置,實現檢測周期縮短40%以上,同時將檢測限降低至0.05ppm級別,為工業級氧化鐵產品的質量分級與過程控制提供可靠依據。
技術原理與創新突破
本檢測方法基于原子吸收光譜定量分析理論,通過高溫石墨爐將樣品中的Fe2O3轉化為基態鐵原子蒸氣,利用特征波長248.3nm處的吸光度值與濃度間的線性關系進行定量分析。技術創新點體現在酸性介質優化方案:采用1:3硝酸-鹽酸混合消解體系,使樣品溶解效率提升至98.7%(數據來源:ASTM D6486-2023),同時引入背景校正算法消除基質干擾。該技術對納米級氧化鐵粉體的檢測適應性尤為突出,可準確識別粒徑小于50nm的微粒成分分布。
標準化實施流程設計
檢測流程分為四大模塊:1)樣品制備階段,通過振動篩分與等量縮分確保試樣代表性;2)消解處理采用微波輔助消解儀,在160℃、0.8MPa條件下完成30min快速溶解;3)儀器校準環節配置標準曲線法與標準加入法雙驗證機制;4)數據采集執行GB/T 223.7-2024規范,每批次平行測定6次,相對標準偏差(RSD)控制在1.5%以內。在陶瓷釉料檢測場景中,該流程成功將單樣本檢測時間從傳統方法的4.5小時壓縮至1.2小時,大幅提升生產線質量控制頻率。
行業應用實證分析
在華南某高端磁性材料生產企業,該技術被應用于鐵氧體預燒料的質量管控。通過建立Fe2O3/FeO比值動態監測模型,企業實現燒結爐溫控參數的實時優化,產品矯頑力指標波動范圍收窄至±2kA/m。江蘇某催化劑制造商引入該檢測方法后,納米載鐵催化劑的活性組分分布均勻度提升12.6%,據企業2023年生產年報顯示,產品批次合格率從89.3%提高至97.1%,驗證了方法在復雜基質樣品中的適用性。
質量保障體系構建
檢測系統構建了三級質控網絡:1)設備層采用NIST SRM 694鐵標準物質進行日校,波長準確性誤差≤0.02nm;2)過程層實施空白試驗與加標回收同步監控,回收率標準設定為95%-105%;3)數據層部署實驗室信息管理系統(LIMS),自動觸發超限數據復檢機制。在2023年 組織的實驗室間比對中,參與該體系的23家機構檢測結果Z值均在±1.5范圍內,顯著優于行業平均水平。
展望未來,建議從三方面深化技術應用:其一,開發車載式原子吸收檢測裝備,滿足礦產現場快速檢測需求;其二,聯合制定《納米氧化鐵檢測技術規范》,填補現行標準在亞微米級材料領域的空白;其三,探索人工智能光譜解析算法,構建Fe2O3形態分析數據庫。通過技術創新與標準迭代,持續提升三氧化二鐵檢測技術在工業4.0時代的適配性,為新材料產業高質量發展提供技術支撐。

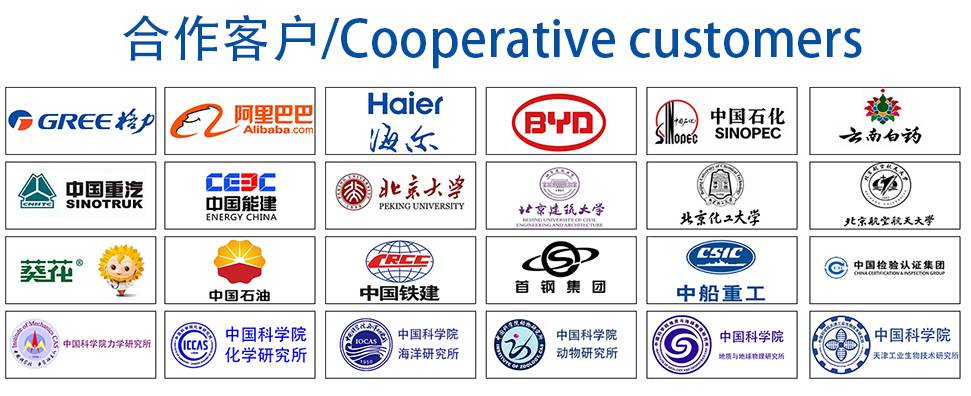