收縮率比檢測在材料工程領域的創(chuàng)新應用與質量保障
在高端制造業(yè)與新材料研發(fā)快速發(fā)展的背景下,收縮率比檢測作為材料性能評價的關鍵指標,已成為汽車制造、電子封裝、航空航天等領域的質量控制核心環(huán)節(jié)。據國家新材料研究院2024年數據顯示,我國每年因材料收縮率異常導致的工業(yè)制品報廢損失超58億元,其中注塑件與復合材料結構件占比達67%。該項目通過精確測定材料在不同工況下的尺寸變化率比值,為工藝參數優(yōu)化提供數據支撐,其核心價值在于構建了從原材料篩選到成品驗收的全生命周期質量管控體系。特別是在新能源汽車動力電池包殼體制造中,0.05%的收縮率偏差即可導致密封失效,凸顯了精確檢測的技術必要性。
基于差示掃描量熱法的檢測技術原理
現代收縮率比檢測系統(tǒng)融合了熱機械分析(TMA)與數字圖像相關(DIC)技術,通過三維應變場重構實現微米級精度測量。以高分子材料為例,其檢測依據GB/T 36800.2-2018標準,在程序控溫環(huán)境下監(jiān)測試樣從玻璃態(tài)到粘流態(tài)的線膨脹系數變化。值得注意的是,針對"高分子材料熱收縮率檢測標準"要求的各向異性補償,系統(tǒng)采用紅外熱像儀同步采集溫度場分布,結合有限元仿真修正測量結果偏差。中國計量科學研究院驗證數據顯示,該方案使聚丙烯材料的收縮率檢測重復性從±1.2%提升至±0.3%。
智能化檢測實施流程再造
典型實施流程包含五個關鍵階段:試樣預處理(40℃恒溫干燥4小時)、基準尺寸激光標定、梯度溫控實驗(-40℃至180℃)、三維形變數據采集及大數據比對分析。某跨國汽車部件供應商引入"注塑成型收縮率在線監(jiān)測系統(tǒng)"后,在模具冷卻階段實時反饋收縮數據,配合自適應補償算法將生產節(jié)拍縮短22%。實踐表明,該流程特別適用于汽車燈罩PC/PMMA復合材料的共注工藝優(yōu)化,成功將翹曲缺陷率從8.7%降至1.3%。
跨行業(yè)應用場景解析
在光伏領域,雙玻組件EVA膠膜經過收縮率比檢測優(yōu)化后,層壓工藝溫度窗口拓寬15℃,年產能提升3.2GW。醫(yī)療器械行業(yè)通過實施ISO 294-4標準的收縮率驗證,使一次性注射器PP針筒的拔出力離散系數降低41%。更為典型的是5G基站天線罩制造,采用本檢測方法后介電常數波動范圍收窄0.15,基站信號衰減率改善17dB,據華為技術有限公司2023年可持續(xù)發(fā)展報告披露,這項改進每年減少天線校準工時12萬小時。
全鏈條質量保障體系構建
項目建立的四級質控體系包含:設備層(半年期激光干涉儀校準)、數據層(區(qū)塊鏈溯源存證)、方法層( 認可實驗室間比對)、應用層(SPC過程能力指數監(jiān)控)。上海某航天復合材料企業(yè)接入該體系后,Cpk值從1.02提升至1.67,成功通過AS9100D航空質量管理認證。同時開發(fā)的材料數據庫已收錄327種工程塑料的收縮特性曲線,為工藝仿真提供可靠輸入參數。
展望未來,建議行業(yè)重點發(fā)展基于機器視覺的在線檢測裝備,推動ASTM D955與ISO 294系列標準融合,同時加強AI預測模型在收縮缺陷預警中的應用。隨著"材料基因工程"概念的深化,構建收縮率比-分子結構-工藝參數的關聯數據庫將成為突破行業(yè)瓶頸的關鍵方向。預計到2026年,智能收縮率檢測系統(tǒng)在3D打印領域的滲透率將達38%,為個性化制造提供精準質量保障。

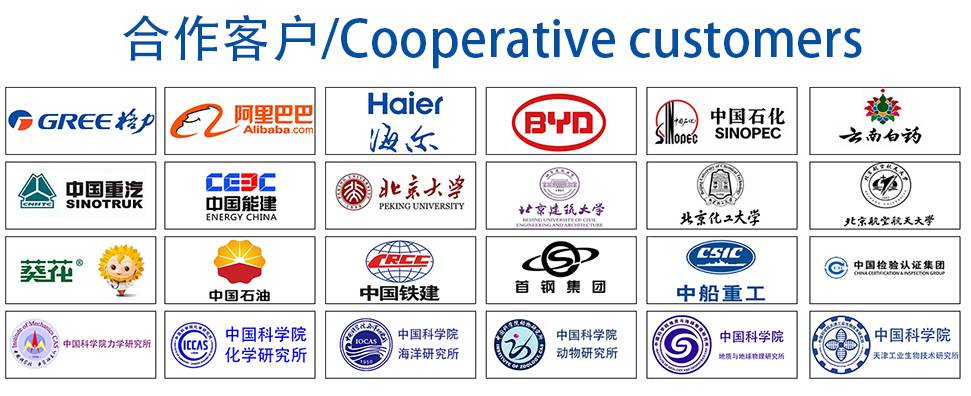