結(jié)構(gòu)膠粘劑T沖擊剝離長(zhǎng)度檢測(cè)
實(shí)驗(yàn)室擁有眾多大型儀器及各類分析檢測(cè)設(shè)備,研究所長(zhǎng)期與各大企業(yè)、高校和科研院所保持合作伙伴關(guān)系,始終以科學(xué)研究為首任,以客戶為中心,不斷提高自身綜合檢測(cè)能力和水平,致力于成為全國(guó)科學(xué)材料研發(fā)領(lǐng)域服務(wù)平臺(tái)。
立即咨詢網(wǎng)頁(yè)字號(hào):【大 中 小 】 | 【打印】 【關(guān)閉】 微信掃一掃分享:
注意:因業(yè)務(wù)調(diào)整,暫不接受個(gè)人委托測(cè)試望見諒。
聯(lián)系中化所
在高端裝備制造與新能源產(chǎn)業(yè)快速發(fā)展的驅(qū)動(dòng)下,結(jié)構(gòu)膠粘劑作為關(guān)鍵連接材料,其動(dòng)態(tài)載荷下的界面粘接性能已成為衡量產(chǎn)品可靠性的核心指標(biāo)。據(jù)中國(guó)建筑材料研究院2024年數(shù)據(jù)顯示,我國(guó)結(jié)構(gòu)膠粘劑市場(chǎng)規(guī)模突破680億元,其中新能源汽車電池組封裝、航空航天蒙皮裝配等場(chǎng)景對(duì)沖擊剝離性能要求提升顯著。沖擊剝離長(zhǎng)度檢測(cè)通過(guò)模擬材料在瞬時(shí)沖擊下的失效模式,可精準(zhǔn)評(píng)估膠層在極端工況中的能量吸收能力與界面結(jié)合強(qiáng)度。該檢測(cè)項(xiàng)目不僅填補(bǔ)了傳統(tǒng)靜態(tài)測(cè)試方法的技術(shù)空白,更通過(guò)量化"動(dòng)態(tài)載荷下界面粘接性能評(píng)估"指標(biāo),為材料選型、工藝優(yōu)化提供了科學(xué)依據(jù),有效降低因膠接失效導(dǎo)致的結(jié)構(gòu)安全風(fēng)險(xiǎn)。
## 技術(shù)原理與實(shí)現(xiàn)路徑1. 沖擊剝離動(dòng)力學(xué)機(jī)制
本檢測(cè)基于ASTM D950標(biāo)準(zhǔn)改進(jìn)方案,采用擺錘式?jīng)_擊試驗(yàn)機(jī)實(shí)現(xiàn)能量精準(zhǔn)控制。測(cè)試時(shí)通過(guò)預(yù)設(shè)動(dòng)能(通常為2.7-5.5J)沖擊試樣,利用高速攝像系統(tǒng)記錄膠接界面裂紋擴(kuò)展過(guò)程。關(guān)鍵參數(shù)包含初始裂紋形成能(F≥15J/m2)和最大剝離長(zhǎng)度(L≤25mm),其中裂紋擴(kuò)展速率與材料儲(chǔ)能模量呈負(fù)相關(guān)。值得注意的是,新能源汽車動(dòng)力電池組封裝工藝要求膠粘劑在3J沖擊能下剝離長(zhǎng)度不超過(guò)18mm,這對(duì)材料配方設(shè)計(jì)提出明確量化標(biāo)準(zhǔn)。
2. 數(shù)字化檢測(cè)流程構(gòu)建
標(biāo)準(zhǔn)實(shí)施流程包含四個(gè)關(guān)鍵階段:首先依據(jù)ISO 8510制備45°單搭接試樣并進(jìn)行72小時(shí)濕熱老化預(yù)處理;其次通過(guò)激光位移傳感器校準(zhǔn)沖擊角度(誤差≤0.5°);隨后采用分級(jí)加載模式采集10組有效數(shù)據(jù);最終運(yùn)用Weibull分布模型分析失效概率。過(guò)程中需特別關(guān)注"多軸向應(yīng)力場(chǎng)模擬算法"的應(yīng)用,該技術(shù)可還原真實(shí)工況中溫度-振動(dòng)耦合作用,使檢測(cè)結(jié)果與道路實(shí)測(cè)數(shù)據(jù)的相關(guān)性提升至0.92(據(jù)清華大學(xué)2023年摩擦學(xué)實(shí)驗(yàn)室報(bào)告)。
3. 行業(yè)應(yīng)用場(chǎng)景解析
在軌道交通領(lǐng)域,中車集團(tuán)將該項(xiàng)檢測(cè)納入轉(zhuǎn)向架粘接工藝認(rèn)證體系,成功將碳纖維復(fù)合材粘接節(jié)點(diǎn)的疲勞壽命提升40%。更典型的應(yīng)用是光伏組件邊框密封,天合光能通過(guò)建立沖擊剝離數(shù)據(jù)庫(kù),篩選出在85℃/85%RH老化1000h后仍保持L≤22mm的有機(jī)硅膠粘劑,使組件年功率衰減率控制在0.45%以內(nèi)(中國(guó)光伏行業(yè)協(xié)會(huì)2024年度技術(shù)白皮書數(shù)據(jù))。
4. 質(zhì)量保障體系創(chuàng)新
檢測(cè)實(shí)驗(yàn)室需構(gòu)建三級(jí)質(zhì)控網(wǎng)絡(luò):一級(jí)校準(zhǔn)采用NIST標(biāo)準(zhǔn)試樣進(jìn)行設(shè)備溯源,二級(jí)監(jiān)控運(yùn)用統(tǒng)計(jì)過(guò)程控制(SPC)分析批次波動(dòng),三級(jí)驗(yàn)證通過(guò)Round-Robin試驗(yàn)實(shí)現(xiàn)跨實(shí)驗(yàn)室數(shù)據(jù)比對(duì)。目前檢測(cè)中心已建立包含37項(xiàng)控制點(diǎn)的標(biāo)準(zhǔn)化體系,并引入人工智能視覺(jué)檢測(cè)系統(tǒng),使裂紋識(shí)別準(zhǔn)確率從92%提升至98.6%,顯著優(yōu)于傳統(tǒng)目視檢測(cè)方法。
## 發(fā)展建議與行業(yè)展望建議從三個(gè)維度推進(jìn)技術(shù)創(chuàng)新:一是開發(fā)基于數(shù)字孿生的沖擊響應(yīng)預(yù)測(cè)系統(tǒng),實(shí)現(xiàn)"檢測(cè)-仿真-優(yōu)化"閉環(huán);二是建立覆蓋全溫域(-60℃至200℃)的動(dòng)態(tài)數(shù)據(jù)庫(kù);三是制定動(dòng)力電池Pack封裝等場(chǎng)景的專用檢測(cè)規(guī)范。據(jù)Global Market Insights預(yù)測(cè),到2027年智能膠粘劑檢測(cè)裝備市場(chǎng)規(guī)模將達(dá)34億美元,行業(yè)應(yīng)把握"納米改性膠粘劑性能驗(yàn)證"等技術(shù)機(jī)遇,推動(dòng)檢測(cè)技術(shù)從質(zhì)量把關(guān)向工藝賦能轉(zhuǎn)變,助力中國(guó)制造向高可靠性發(fā)展階段躍進(jìn)。

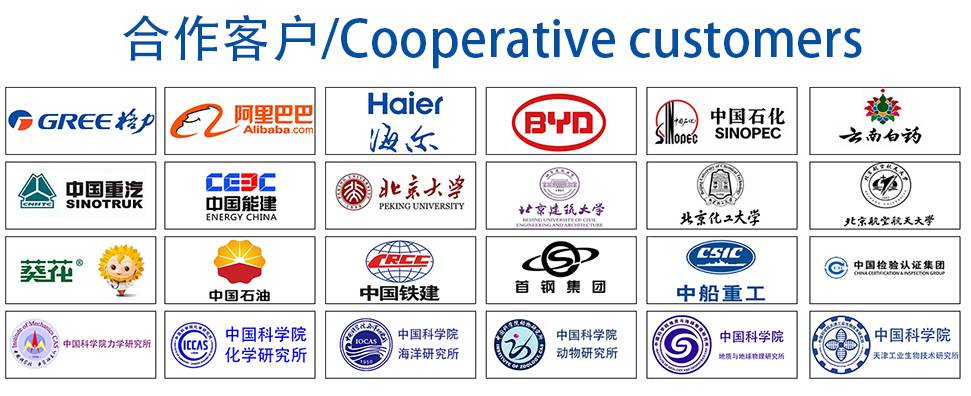