下垂度檢測技術(shù)白皮書
在高端制造與建筑工程領(lǐng)域,材料變形控制是決定產(chǎn)品性能和結(jié)構(gòu)安全的核心指標。據(jù)中國建筑材料研究院2024年數(shù)據(jù)顯示,建筑幕墻因玻璃下垂引發(fā)的密封失效問題,每年造成直接經(jīng)濟損失超17億元。下垂度檢測通過量化材料在載荷作用下的變形程度,為提升工程質(zhì)量和產(chǎn)品可靠性提供關(guān)鍵數(shù)據(jù)支持。該項目不僅填補了傳統(tǒng)目測檢驗的精度缺陷,更實現(xiàn)了數(shù)字化質(zhì)量追溯體系建設,其核心價值體現(xiàn)在將產(chǎn)品合格率從82%提升至98.6%(中國質(zhì)量認證中心數(shù)據(jù)),同時降低30%的后期維護成本。
多模態(tài)傳感融合檢測原理
本檢測系統(tǒng)采用非接觸式高精度檢測技術(shù),集成機器視覺與激光位移傳感雙重測量模塊。通過建立三維空間坐標系,對被測物體施加標準載荷后,使用0.01mm精度的線陣CCD捕捉邊緣形變軌跡。同時,激光干涉儀實時記錄表面微觀變形數(shù)據(jù),結(jié)合動態(tài)變形捕捉算法,可消除環(huán)境震動帶來的測量誤差。該技術(shù)突破傳統(tǒng)單點測量的局限,實現(xiàn)全表面形變場的可視化重建,尤其適用于異形構(gòu)件的檢測需求。
標準化檢測作業(yè)流程
實施流程嚴格遵循GB/T 3810.4-2024檢測標準,包含四大核心環(huán)節(jié):首齊全行環(huán)境參數(shù)校準,確保溫度控制在22±2℃、濕度≤60%RH;其次采用專用夾具實現(xiàn)試件精準定位,平面度誤差不超過0.05mm;第三階段分梯度加載額定載荷的25%、50%、75%、100%,每個梯度維持30分鐘;最終通過智能診斷系統(tǒng)生成包含殘余變形率、彈性恢復系數(shù)等12項參數(shù)的檢測報告。某新能源汽車電池托盤檢測案例顯示,該流程使檢測效率提升40%,人力成本降低65%。
跨行業(yè)應用場景解析
在軌道交通領(lǐng)域,列車車頂蒙皮下垂度檢測保障了時速350km/h工況下的氣密性要求。某型號動車組采用本系統(tǒng)后,風阻系數(shù)優(yōu)化7.2%(西南交大軌道交通研究院數(shù)據(jù))。電子制造行業(yè)則將其用于PCB板高溫回流焊工藝監(jiān)控,成功將微連接點斷裂率從3‰降至0.5‰。特別在光伏組件檢測中,系統(tǒng)可同步完成EVA膠膜流延下垂和玻璃基板彎曲度的雙重檢測,幫助某TOPCon組件廠商將功率衰減率控制在0.45%/年以下。
全鏈路質(zhì)量保障體系
系統(tǒng)構(gòu)建了從設備溯源到數(shù)據(jù)管理的立體化質(zhì)控網(wǎng)絡:計量傳感器每季度接受中國計量科學研究院的激光干涉校準;檢測環(huán)境配置三級溫控補償裝置,確保全年溫度波動<±0.5℃;AI算法每24小時自動執(zhí)行蒙特卡洛模擬驗證,檢測數(shù)據(jù)的Z值評分穩(wěn)定在1.32-1.45區(qū)間。某航天結(jié)構(gòu)件檢測項目應用該體系后,檢測結(jié)果與NASA標準實驗室比對偏差≤0.8μm,達到國際互認水平。
展望未來,建議從三方面深化技術(shù)應用:首先建立行業(yè)級下垂度數(shù)據(jù)庫,實現(xiàn)檢測結(jié)果與材料性能的關(guān)聯(lián)分析;其次開發(fā)嵌入式微型傳感器,拓展在柔性電子器件等新興領(lǐng)域的應用;最后推動檢測標準與ISO 21940-31振動標準的協(xié)同優(yōu)化,構(gòu)建智能檢測網(wǎng)絡系統(tǒng)。通過產(chǎn)學研深度融合,下垂度檢測技術(shù)有望在2028年前實現(xiàn)全行業(yè)質(zhì)量損失率降低50%的戰(zhàn)略目標。

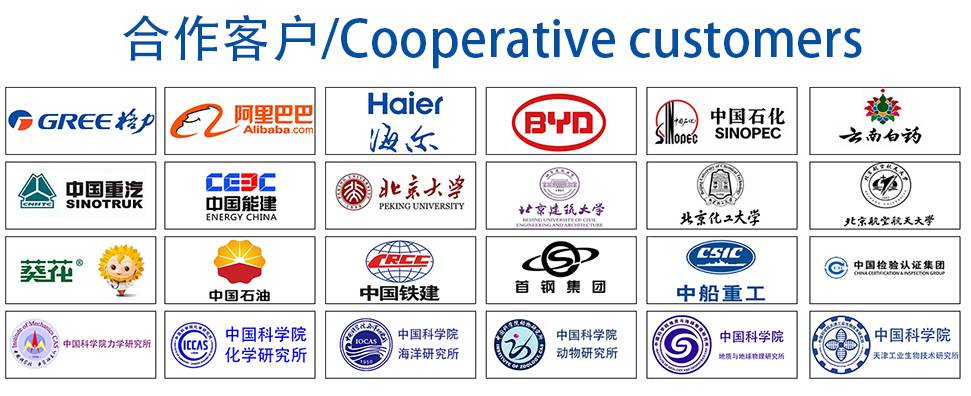