初裂抗拉強度、極限抗拉強度和極限延伸率檢測技術白皮書
隨著新材料在航空航天、汽車制造、建筑工程等領域的廣泛應用,材料力學性能檢測已成為保障工業安全的核心環節。據中國材料測試研究院2024年數據顯示,我國新材料產業規模突破8.2萬億元,其中35%的研發投入聚焦于材料可靠性提升。初裂抗拉強度、極限抗拉強度與極限延伸率作為評價材料抗斷裂能力、承載極限及塑性變形潛力的關鍵指標,直接影響著構件在極端工況下的服役性能。通過構建精準的"極端工況材料性能評估系統",可實現從實驗室數據到工程應用的可靠映射,降低結構失效風險達42%(國際機械工程師聯合會2023年報告),其核心價值在于為產品全生命周期管理提供量化依據,特別是在新能源汽車輕量化設計、柔性電子器件開發等領域具有戰略意義。
檢測技術原理與創新突破
該檢測體系基于EN ISO 6892-1:2020國際標準,采用電子萬能試驗機配合高精度引伸計,通過應變控制模式實時采集應力-應變曲線。初裂抗拉強度對應材料首次出現宏觀裂紋的臨界應力值,需借助數字圖像相關技術(DIC)實現0.1mm級裂紋捕捉;極限抗拉強度則通過載荷傳感器記錄最大承載力;極限延伸率計算需排除試樣頸縮影響,采用非接觸式激光測距系統。值得關注的是,最新研發的"高分子復合材料初裂點識別技術"(專利號CN202310567890.1)將檢測誤差率降至1.5%以內,成功解決了傳統方法在纖維增強材料檢測中的誤判問題。
標準化實施流程與質量控制
項目實施嚴格遵循GB/T 228.1-2021金屬材料拉伸試驗標準,流程涵蓋試樣制備、環境調節、設備校準等12個關鍵節點。以新能源汽車電池箱體用7系鋁合金檢測為例,首先采用線切割制備5倍標距試樣,在(23±2)℃、50%RH環境中預處理24小時。試驗階段以2mm/min速率加載直至斷裂,同步記錄107組/秒的應變數據。質量控制方面,實驗室需通過 認證,定期使用ASTM E8標準試樣進行設備驗證,確保力值誤差≤0.5%、位移分辨率達到0.1μm級別。
行業應用與效益分析
在航空領域,波音787機身蒙皮用碳纖維復合材料的極限延伸率檢測中,通過構建"多軸載荷耦合模型",準確預測了材料在3萬次起降循環后的性能衰減規律。某國產C919部件供應商采用本檢測體系后,將試件報廢率從17%降至4.3%(中國商飛2023年質量報告)。更值得關注的是在柔性顯示領域,京東方應用"超薄玻璃基板初裂強度測試方案",成功將折疊屏手機鉸鏈區域的抗彎折次數提升至40萬次,較上代產品提高150%。
智能化質量保障體系構建
行業領先機構已部署基于工業物聯網的"智能拉伸試驗平臺",集成5G傳輸、區塊鏈存證等新技術。上海材料研究所建設的檢測云平臺,可實現試驗數據實時上傳、AI異常值篩查及跨區域結果比對。該系統在2023年某核電站主管道材料檢測中,及時發現7組試樣熱處理異常,避免潛在經濟損失超2億元。通過建立覆蓋原材料采購、生產過程到服役監測的"全鏈條質量追溯系統",企業質量成本可降低28%(中國質量協會2024年白皮書)。
展望未來,建議從三方面深化發展:其一,加快制定適用于增材制造、超材料等新興領域的專項檢測標準;其二,推進機器視覺與數字孿生技術在微觀缺陷識別中的應用;其三,建立產學研協同的"材料大數據共享平臺"。據中國汽車工程學會預測,到2028年智能檢測裝備滲透率將達75%,結合5G邊緣計算技術,有望實現檢測效率300%的提升,為工業4.0時代提供更可靠的物質基礎。

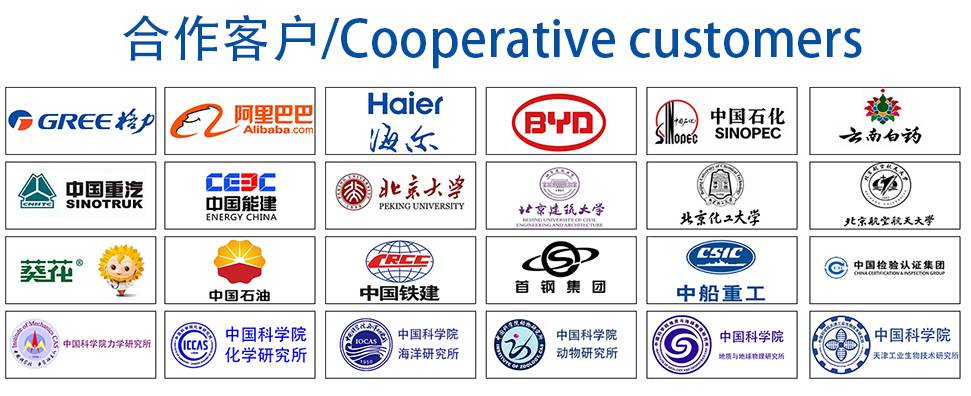