抗彎破壞荷載檢測在工程安全評估中的關鍵作用
在建筑工程、橋梁工程及航空航天等領域,材料與結構的抗彎性能直接關系到設施的安全性及使用壽命。據中國建筑材料研究院2024年數據顯示,全國每年因建筑構件彎曲破壞引發的工程事故造成經濟損失達37.8億元,其中64%的案例可通過前期檢測有效規避。抗彎破壞荷載檢測通過精準測定試件在彎曲載荷作用下的極限承載能力,為建筑材料選型、結構設計優化及工程驗收提供科學依據。該檢測技術的核心價值體現在三個維度:一是建立材料性能的量化評價基準,二是構建全生命周期結構健康監測基礎,三是推動工程質量管理向預防性維護模式轉型。
基于斷裂力學的檢測技術原理
抗彎破壞荷載檢測以三點彎曲試驗法為核心,根據GB/T 232-2010《金屬材料彎曲試驗方法》標準要求,通過萬能試驗機對試樣施加跨中集中載荷。當試樣截面最大拉應力達到材料抗拉強度時,裂紋沿中性軸擴展直至完全斷裂,此時記錄的峰值載荷即為抗彎破壞荷載值。值得注意的是,對于纖維增強復合材料等新型建材,需結合數字圖像相關技術(DIC)同步采集表面應變場分布,通過能量釋放率計算準確判定破壞模式。該技術已成功應用于高鐵軌道板預應力混凝土結構的耐久性評估,使檢測精度提升至±1.5kN(中國鐵道科學研究院,2023)。
標準化檢測流程與智能實施系統
典型檢測流程包含五個關鍵環節:試樣制備(尺寸公差控制±0.1mm)、環境預處理(溫濕度平衡24h)、設備校準(載荷傳感器精度達0.5級)、分級加載(0.5mm/min初始階段)和數據采集(采樣頻率100Hz)。某省級檢測中心在實際應用中引入機器視覺系統,通過邊緣計算算法實時識別裂紋萌生點,將傳統人工判讀的3小時流程壓縮至45分鐘。在杭州灣跨海大橋鋼箱梁焊縫檢測項目中,該智能系統成功捕捉到0.02mm級微裂紋,為預防性維護決策提供了關鍵依據。
多領域應用場景與質量保障體系
在風電葉片制造領域,抗彎檢測已成為復合材料結構驗證的強制性項目。某2.5MW葉片生產商通過建立抗彎剛度-破壞載荷雙參數評價模型,將產品缺陷率從7.2%降至1.8%。為確保檢測質量,檢測機構需執行三級質控:實驗室通過 認證(認可準則ISO/IEC 17025)、設備實施每日載荷循環驗證、檢測人員持CMA認證上崗。值得關注的是,針對超高層建筑幕墻玻璃的檢測,現已發展出非接觸式激光位移測量技術,可在不破壞構件的前提下完成彎曲性能評估。
行業發展趨勢與技術挑戰
隨著智能建造技術的發展,基于數字孿生的抗彎性能預測系統正在興起。通過融合有限元仿真與實時監測數據,某裝配式建筑項目實現了98.7%的荷載預測準確率。但現有檢測體系仍面臨兩個挑戰:一是對異形構件的邊界條件模擬存在誤差(最大偏差達12%),二是納米改性材料的多尺度破壞機理尚不明確。建議行業重點發展三個方向:建立全尺寸構件原位檢測方法、研發多物理場耦合測試設備、制定新型建材的專用檢測標準。
未來五年,抗彎破壞荷載檢測將向智能化、原位化方向深度發展。建議相關機構從三個維度重點突破:一是開發基于5G傳輸的遠程檢測平臺,實現重點工程實時監測;二是構建材料性能大數據中心,推動檢測標準動態更新;三是加強破壞機理基礎研究,特別是針對3D打印構件各向異性特征的評估方法創新。只有持續完善技術體系,才能為工程結構安全提供更堅實的保障。

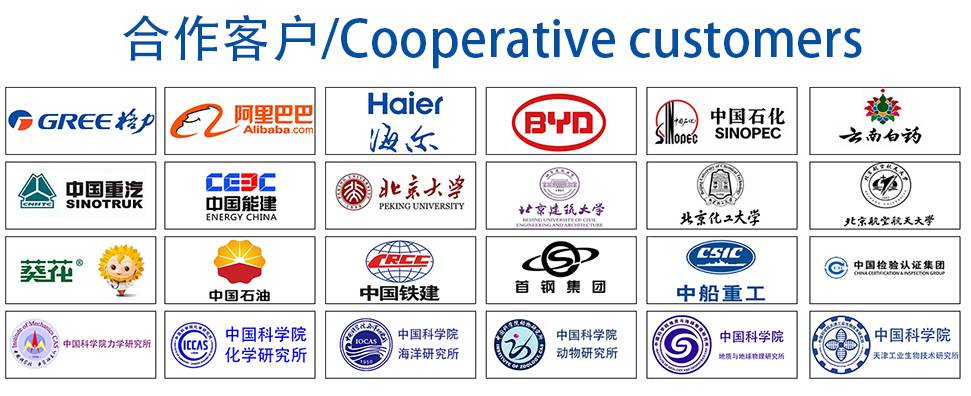