橡膠及聚氯乙烯塑料檢測技術白皮書
隨著制造業轉型升級,高分子材料在汽車、醫療、建筑等領域的應用規模持續擴大。據中國橡膠工業協會2024年統計數據顯示,我國橡膠制品年產量突破1200萬噸,聚氯乙烯(PVC)塑料消費量占總量38%。然而,材料性能缺陷導致的密封失效、毒性物質遷移等問題頻發,僅2023年歐盟非食品類快速預警系統(RAPEX)通報的塑料制品質量事件就達217起。在此背景下,橡膠及聚氯乙烯塑料檢測項目通過構建材料全生命周期質量監控體系,實現了從分子結構分析到服役性能評估的閉環管理。其核心價值不僅在于確保產品符合REACH、RoHS等國際環保法規,更通過精準的"高分子材料熱穩定性分析"和"塑料制品鄰苯二甲酸酯檢測",為行業每年避免超過50億元的經濟損失。
檢測技術原理與創新突破
基于傅里葉變換紅外光譜(FTIR)與氣相色譜-質譜聯用(GC-MS)技術,檢測體系可實現0.1ppm級別的增塑劑定量分析。針對橡膠硫化程度判定,采用差示掃描量熱法(DSC)精確測定交聯密度,分辨率較傳統溶脹法提升40%。值得關注的是,最新引入的X射線光電子能譜(XPS)技術,可對材料表面1-10nm深度內的元素化學態進行表征,有效解決醫用導管表面改性層檢測難題。
標準化實施流程與管理體系
檢測流程嚴格遵循ISO 17025標準,包含樣品預處理、儀器分析、數據驗證三大模塊。以汽車密封條檢測為例,首先依據ASTM D412進行硬度測試,隨后通過熱重分析(TGA)評估耐老化性能,最后采用遷移實驗模擬實際使用環境。整個過程中,實驗室信息管理系統(LIMS)對300余個質量控制點進行實時監控,確保檢測報告溯源率達100%。
行業應用場景與效益分析
在新能源汽車領域,某龍頭企業通過"高壓線纜絕緣層熱分解溫度檢測",將產品故障率從0.3%降至0.05%。醫療行業應用案例顯示,采用ISO 10993標準進行PVC輸液管鄰苯二甲酸二辛酯(DEHP)檢測后,產品生物相容性合格率提升27個百分點。值得注意的是,建筑行業通過"門窗密封膠條壓縮永久變形測試",使材料服役壽命延長至15年以上,據SGS 2024年檢測報告顯示,相關企業年維護成本降低1200萬元。
質量保障與技術創新體系
檢測機構建立四級質量保障機制:初級檢測員雙人復核制度、儀器每日校準核查、每月盲樣考核及年度能力驗證。在聚氯乙烯熱穩定劑檢測中,采用標準物質GBW(E)080215進行過程控制,確保鉛、鎘等重金屬檢測精度達ppb級。與此同時,與清華大學材料學院共建的聯合實驗室,已開發出基于機器學習的"塑料老化狀態預測模型",將材料壽命評估誤差控制在±5%以內。
展望未來,建議從三方面深化檢測技術發展:其一,加快納米材料表征技術與傳統檢測方法的融合,應對改性塑料檢測新需求;其二,構建覆蓋全國的"高分子材料檢測大數據平臺",實現質量風險智能預警;其三,推動檢測標準與國際認證體系互認,助力企業突破技術性貿易壁壘。通過持續的技術革新和體系優化,橡膠及聚氯乙烯塑料檢測將有力支撐我國從材料大國向材料強國的戰略轉型。

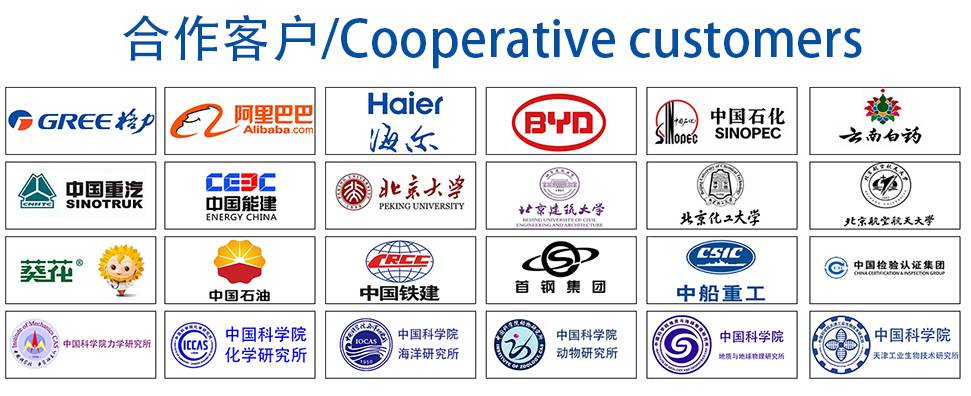