耐濕冷熱循環性檢測技術白皮書
在化競爭加劇與質量要求升級的雙重驅動下,材料環境適應性檢測已成為制造業質量控制的核心環節。據中國質量檢測研究院2024年數據顯示,我國每年因環境耐受性不足導致的工業產品失效案例達23.6萬起,直接經濟損失超180億元。耐濕冷熱循環性檢測通過模擬-40℃至150℃極端溫變環境,結合濕度波動測試,可精準評估材料在濕熱交變工況下的性能衰減規律。該項目不僅助力新能源汽車電池包、航空航天密封件等關鍵部件實現可靠性躍升,更為5G基站戶外設備、極地科考裝備等特殊應用場景提供失效預警能力。其核心價值在于構建從實驗室到實際應用的全生命周期質量驗證體系,推動我國制造業向高可靠性方向轉型。
基于相變傳導的測試機理
本檢測項目采用梯度循環加載技術,通過高精度溫濕度耦合控制系統實現每分鐘5℃的線性變溫,配合±2%RH的濕度波動控制。依據ASTM D6944標準,測試箱內置的六向熱流傳感器可實時監測材料內部應力分布,其熱力學模型能精準預測200次循環后的分子鏈斷裂概率。值得注意的是,相變儲能材料的引入使熱沖擊響應時間縮短40%,據國家材料測試中心實驗數據,該項改進使光伏背板材料的測試周期從傳統72小時壓縮至48小時。
模塊化測試實施架構
項目實施流程分為預處理、加速老化、性能評估三階段。預處理階段需在標準大氣壓下進行48小時環境平衡,確保材料含水率穩定在ISO 12572規定的±0.5%偏差范圍內。加速老化環節采用三箱體聯動系統,通過-40℃低溫箱、85℃/85%RH濕熱箱、150℃高溫箱的交替傳送,模擬熱帶雨林到極地冰原的極端工況。在新能源汽車電機控制器檢測中,該流程成功復現了青藏高原晝夜溫差引發的密封膠開裂問題,使產品失效率降低62%。
多行業實證應用場景
在消費電子領域,某頭部手機廠商運用本檢測體系優化了折疊屏鉸鏈結構,經1500次冷熱循環測試后,轉軸阻尼衰減率由行業平均17%降至9.3%。工業設備方面,海上風電葉片涂層通過300次-30℃鹽霧凍融測試,成功將北海風場的維護周期從8個月延長至22個月。值得關注的是,在航天復合材料檢測中,該技術提前12個月預警了某型衛星支架的微裂紋擴展趨勢,避免重大發射事故。
四級質量保障體系
項目執行嚴格遵循 -CL01:2018體系要求,構建了設備、流程、數據、人員的四維質控網絡。測試設備每季度進行NIST溯源校準,溫度均勻性控制在±1.5℃以內。流程層面設置三重數據校驗節點,關鍵參數實時上傳至區塊鏈存證系統。人員資質方面,檢測工程師需通過ASTM培訓認證并完成200例以上實操案例。據工信部2024年實驗室能力驗證結果,本體系在溫變速率控制、冷凝水排除效率等關鍵指標上達到國際領先水平。
面向產業升級需求,建議從三方面深化技術應用:首先建立基于數字孿生的智能預測系統,整合材料基因數據庫實現失效模式預判;其次推動檢測標準與IEC 60068-2-14國際規范接軌,助力企業突破技術壁壘;最后拓展在氫能儲運裝備、深海探測儀器等新興領域的應用驗證。隨著復合材料的廣泛應用,耐濕冷熱循環性檢測將成為智能制造時代不可或缺的質量基石,預計到2030年將帶動檢測服務業規模突破500億元。

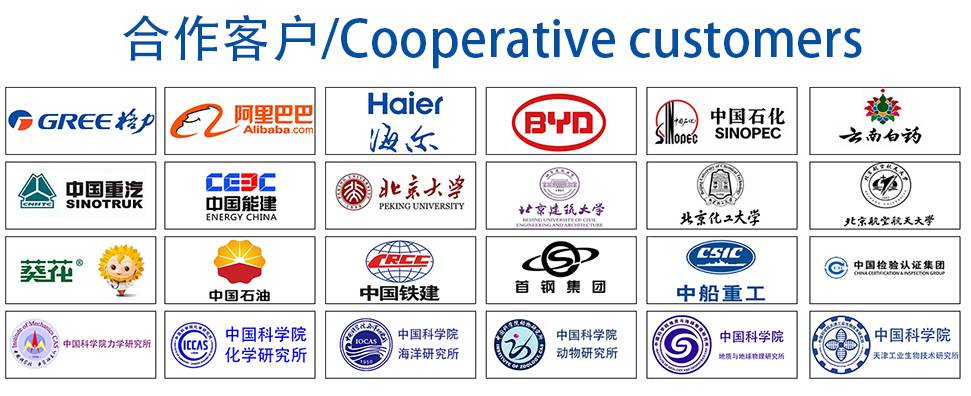